AISI 4130 alloy steel is a versatile medium-carbon low-alloy steel. It is also categorized as an ultrahigh-strength steel, meaning it’s designed for structural applications that demand very high loads and often require a high strength-to-weight ratio, along with good ductility and toughness. Its Unified Numbering System (UNS) designation is G41300. In Germany, it corresponds to DIN 34CrMo4, and in Japan, it is known as JIS SCM430.
1. Applications
- Automotive Industry: such as axles
- Aerospace and Missile Structures: aircraft and missile structural components
- Welded Structures
- Workpiece Material
- Product Forms: Include seamless and welded tubing, bars, forgings, sheets, rings, billets, and welding wire
2. 4130 Steel Composition1
Carbon (C) | Manganese (Mn) | Silicon (Si) | Chromium (Cr) | Molybdenum (Mo) | Phosphorus (P) | Sulfur (S) | Copper (Cu) |
0.28-0.33 | 0.40-0.60 | 0.20-0.35 | 0.80-1.10 | 0.15-0.25 | ≤0.035 | ≤0.040 | ≤0.35 |
3. 4130 Steel Properties
3.1 Mechanical properties
AISI 4130 mechanical properties vary significantly depending on the heat treating and section thickness.
3.1.1 Water quenched and tempered
Tempering Temperature | Tensile Strength | Yield Strength | Elongation in 50 mm (2 in.), % | Reduction in Area, % | Hardness, HB | Izod Impact Energy | ||||
°C | °F | MPa | ksi | MPa | ksi | J | ft-lb | |||
205 | 400 | 1765 | 256 | 1520 | 220 | 10 | 33 | 475 | 18 | 13 |
260 | 500 | 1670 | 242 | 1430 | 208 | 11.5 | 37 | 455 | 14 | 10 |
315 | 600 | 1570 | 228 | 1340 | 195 | 13 | 41 | 425 | 14 | 10 |
370 | 700 | 1475 | 214 | 1250 | 182 | 15 | 45 | 400 | 20 | 15 |
425 | 800 | 1380 | 200 | 1170 | 170 | 16.5 | 49 | 375 | 34 | 25 |
540 | 1000 | 1170 | 170 | 1000 | 145 | 20 | 56 | 325 | 81 | 60 |
650 | 1200 | 965 | 140 | 830 | 120 | 22 | 63 | 270 | 135 | 100 |
3.1.2 Oil quenched and tempered
Tempering Temperature | Tensile Strength | Yield Strength | Elongation in 50 mm (2 in.), % | Reduction in Area, % | Hardness, HB | Izod Impact Energy | ||||
°C | °F | MPa | ksi | MPa | ksi | J | ft-lb | |||
205 | 400 | 1550 | 225 | 1340 | 195 | 11 | 38 | 450 | — | — |
260 | 500 | 1500 | 218 | 1275 | 185 | 11.5 | 40 | 440 | — | — |
315 | 600 | 1420 | 206 | 1210 | 175 | 12.5 | 43 | 418 | — | — |
370 | 700 | 1320 | 192 | 1120 | 162 | 14.5 | 48 | 385 | — | — |
3.1.3 Effects of mass on typical properties of heat-treated 4130 alloy steel
Bar size | Tensile strength | Yield strength | Elongation in 50 mm (2 in.), % | Reduction in area, % | Surface hardness, HB |
mm | MPa | ksi | MPa | ksi | % |
25 | 1040 | 151 | 880 | 128 | 18 |
50 | 740 | 107 | 570 | 83 | 20 |
75 | 710 | 103 | 540 | 78 | 22 |
3.2 Physical Properties2
- Thermal Conductivity: At 200 °C, the thermal conductivity for quenched and tempered 4130 is 12.2 W/m·K.
- Coefficient of Thermal Expansion: For quenched and tempered 4130, the coefficient of thermal expansion is 14.6 x 10^-6/°C in the range of 20–100 °C and 20–600 °C.
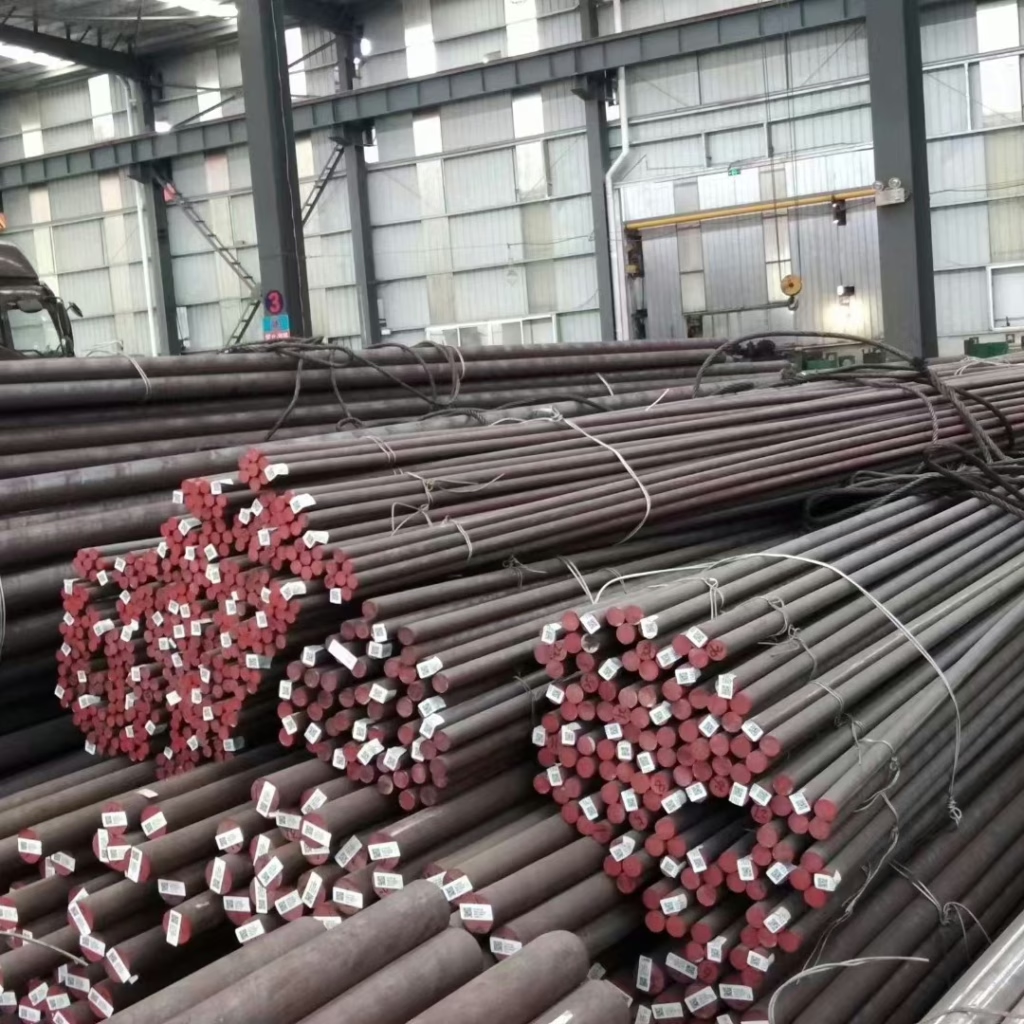
Looking for 4130 steel?
Please fill out the following form to contact us today!
4. Heat treatment
The heat treatments for 4130 steel include normalizing, annealing, hardening, tempering, and stress relief.
4.1 Normalizing
The purpose of normalizing is to refine the grain size and obtain a complete solution of the original structure with the formation of austenite.
We suggest that the normalizing temperature be 870-925°C (1600-1700°F), with a soaking time of at least 1 hour or 15 to 20 minutes per 25 mm (1 inch) of maximum section thickness, followed by air cooling.
4.2 Annealing
Annealing is used to soften AISI 4130, thereby increasing its workability and machinability.
The annealing temperature range is 830 to 870°C (1525 to 1600°F), with the holding time varying depending on the section thickness or furnace load. It is then cooled at a rate of 15 °C/h (30 °F/h) to 480 °C (900 °F) and finally air-cooled.
4.3 Quenching
This aims to transform the 4130 steel’s microstructure into martensite or bainite, providing high hardness and toughness.
The quenching medium is water or oil. The hardening temperature is 860 to 885 °C (1575 to 1625 °F) for oil quenching or 845 to 870 °C (1550 to 1600 °F) for water quenching.
Because 4130 material has low hardenability, its section thickness must be carefully considered when aiming for high hardness or strength. When compared to 4140 steel, which has higher carbon content and thus greater hardenability, 4130 material is less prone to cracking and distortion during quenching.
4.4 Tempering
Tempering is performed after hardening to reduce internal stresses, increase ductility and toughness, and adjust hardness to the desired level.
The tempering temperature range for 4130 steel is broad, from 200 to 700 °C (400 to 1300 °F). The specific temperature chosen will depend on the desired final properties. Tempering should occur as soon as the 4130 parts reach 52 to 65 °C (125 to 150 °F) after quenching.
Tempering significantly influences the room-temperature mechanical properties of AISI 4130, including tensile strength, yield strength, and Izod impact energy.
4.5 Stress Relieving
Stress relief heat treatment is used to eliminate stresses generated in 4130 material during processing, such as straightening, forming, or machining.
We recommend a temperature range of 650 to 675°C (1200 to 1250°F). For hardened 4130 material, the stress relief temperature should not exceed the tempering temperatures previously applied.
5. Equivalent Grades
- ASTM: A322, A29/A29M
- SAE: J404
- JIS (Japan): SCM 425, SCM 430
- Germany: DIN 34CrMo4
- ASM International. (1991). ASM Handbook, Volume 4: Heat Treating (p. 496). ASM International. ↩︎
- ASM International. (1991). ASM Handbook, Volume 4: Heat Treating (pp. 500-501). ASM International. ↩︎
FAQ
No, 4130 is not classified as a high-carbon steel; it is a medium-carbon, low-alloy steel.
Yes. While 4130 steel contains chromium, it is not in sufficient quantities to provide the corrosion resistance found in stainless steel. Therefore, it is prone to rust. Molybdenum does improve its resistance to localized corrosion, such as pitting.
4130 alloy steel is a strong material, categorized as a medium-carbon low-alloy steel within the family of “ultrahigh-strength steels”. Its strength can vary significantly depending on its condition, such as heat treatment (annealed, normalized, quenched, and tempered), processing (drawn, cast), and even the section size.
4130 steel is machinable, but the ease or difficulty of machining it depends significantly on its heat treatment and resulting hardness.
4130 steel can be bent, especially when it has been annealed or appropriately tempered to enhance its ductility and reduce its yield strength.
Yes, 4130 steel has good weldability because of its lower carbon content, which reduces weld hardening and cracking risk. Standard processes like GTAW (TIG) or SMAW can be used. Best practices include preheating for sections thicker than 0.12 inches (to about 300°F/150°C), using a suitable filler material like ER70S-2, avoiding excessive heat, and allowing mild cooling. Post-weld heat treatment may be necessary for critical applications to relieve residual stresses and improve weld toughness.
4130 steel is a type of low-alloy steel commonly known as Chromium-Molybdenum (Chromoly) steel. It is popular across various industries for its strength, relatively lightweight, and good weldability.
In the SAE-AISI four-digit classification system, the first digit (4) indicates it belongs to the molybdenum alloy steel class. The second digit (1) specifies an approximate concentration of 1% chromium and molybdenum by mass. The last two digits (30) represent the carbon content, which is 0.30%.
“Chromoly” is an informal term for the SAE 41xx family of steel grades. These steels, including 4130, are alloyed with chromium and molybdenum, giving them an excellent strength-to-weight ratio and making them considerably stronger and harder than standard 1020 steel.
The primary alloying elements are Chromium (Cr) and Molybdenum (Mo). Carbon (C) increases strength and hardness. Chromium improves hardenability, corrosion resistance, and wear resistance. Molybdenum enhances high-temperature strength, creep resistance, and toughness, and refines the grain structure.
4130 steel primarily consists of Carbon (C) (0.28% – 0.33%), Chromium (Cr) (0.8% – 1.1%), and Molybdenum (Mo) (0.15% – 0.25%). It also contains Manganese (0.40% – 0.60%) and Silicon (0.15% – 0.35%).
4130 steel has a tensile strength ranging from 560 MPa (81,000 psi) to 725 MPa (105,000 psi) and a yield strength of approximately 460 MPa (67,000 psi), depending on heat treatment. It offers good impact resistance and exhibits high ductility (elongation at break between 21.50% and 25.5%). Its Rockwell B hardness is typically 92-95.
The density of 4130 steel is 7.85 g/cm³ (0.284 lb/in³).
Yes, 4130 Chromoly steel has very high creep and fatigue resistance. This property is crucial for applications involving repeated stress or cyclic loading.
4130 steel is considered more machinable than higher carbon steels like 4140, mainly due to its lower carbon content. It offers less resistance to cutting tools, resulting in cleaner cuts, longer tool life, and less chip formation. Its average machinability rating in the annealed condition is around 70%.
Tempering is critical because 4130 steel in its as-quenched condition is very brittle due to its high hardness and internal stresses. Tempering (reheating to a lower temperature) relieves these stresses, reduces brittleness, and improves toughness and ductility while maintaining some of the increased hardness from quenching.
Yes, 4130 Chromoly Steel can undergo work hardening processes. Mechanical processes like cold working can further increase its hardness, tensile strength, and yield strength.
4130 steel is extensively used in applications requiring a balance of strength, toughness, and weldability. Common uses include:
Aerospace: Aircraft fuselage components, landing gear, engine mounts.
Automotive/Motorsports: Roll cages in race cars, suspension components, drivetrain parts, chassis.
Bicycle Frames: High-end mountain bike and custom frames.
Oil and Gas: Drill collars and wellhead components.
Firearms: Barrel sleeves and receiver components.
Industrial Machinery: Bearings, gears, shafts, axles, and some tooling.
The primary difference is the carbon content: 4130 has a carbon content of 0.28%-0.33%, while 4140 has a carbon content of 0.38%-0.43%. This higher carbon makes 4140 stronger and harder (higher tensile and yield strength), but 4130 offers a better balance of strength and toughness with slightly better impact resistance. 4130 is also more machinable and has better weldability than 4140. 4130 is generally slightly less expensive. For more information, please read 4130 vs 4140 steel.
No, 4130 steel is an alloy steel, specifically a low-alloy steel. Mild steel (e.g., 1018 carbon steel) is generally weaker and less durable, lacking the specialized alloying elements that give 4130 its enhanced properties, such as higher tensile strength, toughness, and fatigue resistance.
4130 steel is known for its excellent strength-to-weight ratio. While aluminum typically has a higher stiffness-to-weight ratio, steel (including 4130) has a higher strength-to-weight ratio. 4130’s yield strength (435 MPa) significantly surpasses that of most aluminum alloys.
Stainless steels (e.g., 304) offer superior corrosion resistance due to their higher chromium content. However, stainless steels tend to be denser and generally do not match 4130’s exceptional strength-to-weight ratio. While 4130 is weldable, stainless steel may require more precise heat control during welding to maintain its properties.
After quenching, 4130 steel can achieve its maximum hardness, potentially ranging from 20 HRC to 50 HRC (Rockwell C scale), depending on the specific heat treatment parameters and tempering temperature. For practical applications where toughness is also desired, a more common hardness range after proper tempering is 38 HRC to 42 HRC. In its annealed condition, it has a hardness of around 155 HB (Brinell Hardness), and after normalization, it ranges from 165 to 220 HB.
Get a Competitive Quote for 4130 Alloy Steel
With over 20 years of forging expertise, Aobo Steel is your trusted partner for high-performance 4130 alloy steel. We provide not just materials, but solutions. Leverage our deep industry knowledge and reliable supply chain for your project’s success.
✉ Contact us by filling out the form below.
Explore Our Other Products
D2/1.2379/SKD11
D3/1.2080/SKD1
D6/1.2436/SKD2
A2/1.23663/SKD12
O1/1.2510/SKS3
O2/1.2842
S1/1.2550
S7/1.2355
DC53
H13/1.2344/SKD61
H11/1.2343/SKD6
H21/1.2581/SKD7
L6/1.2714/SKT4
M2/1.3343/SKH51
M35/1.3243/SKH55
M42/1.3247/SKH59
P20/1.2311
P20+Ni/1.2738
420/1.2083/2Cr13
422 stainless steel
52100 bearing steel
440C stainless steel
4140/42CrMo4/SCM440
4340/34CrNiMo6/1.6582
4130
5140/42Cr4/SCR440
SCM415