What’s the main difference between H13 and A2 tool steel? The bottom line is this: H13 is your go-to for hot work applications where tools operate at high temperatures. A2, on the other hand, is designed for cold work applications, excelling in tasks where dimensional stability and good wear resistance at ambient temperatures are key.
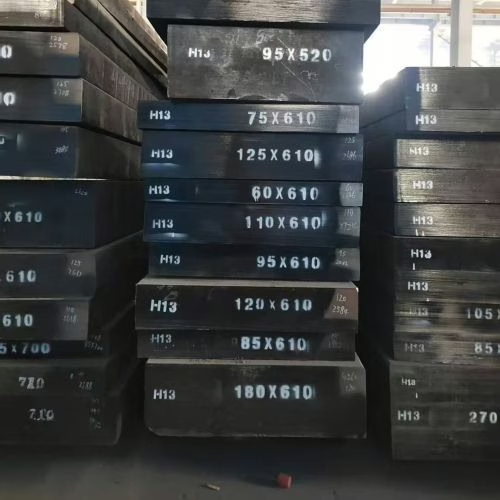
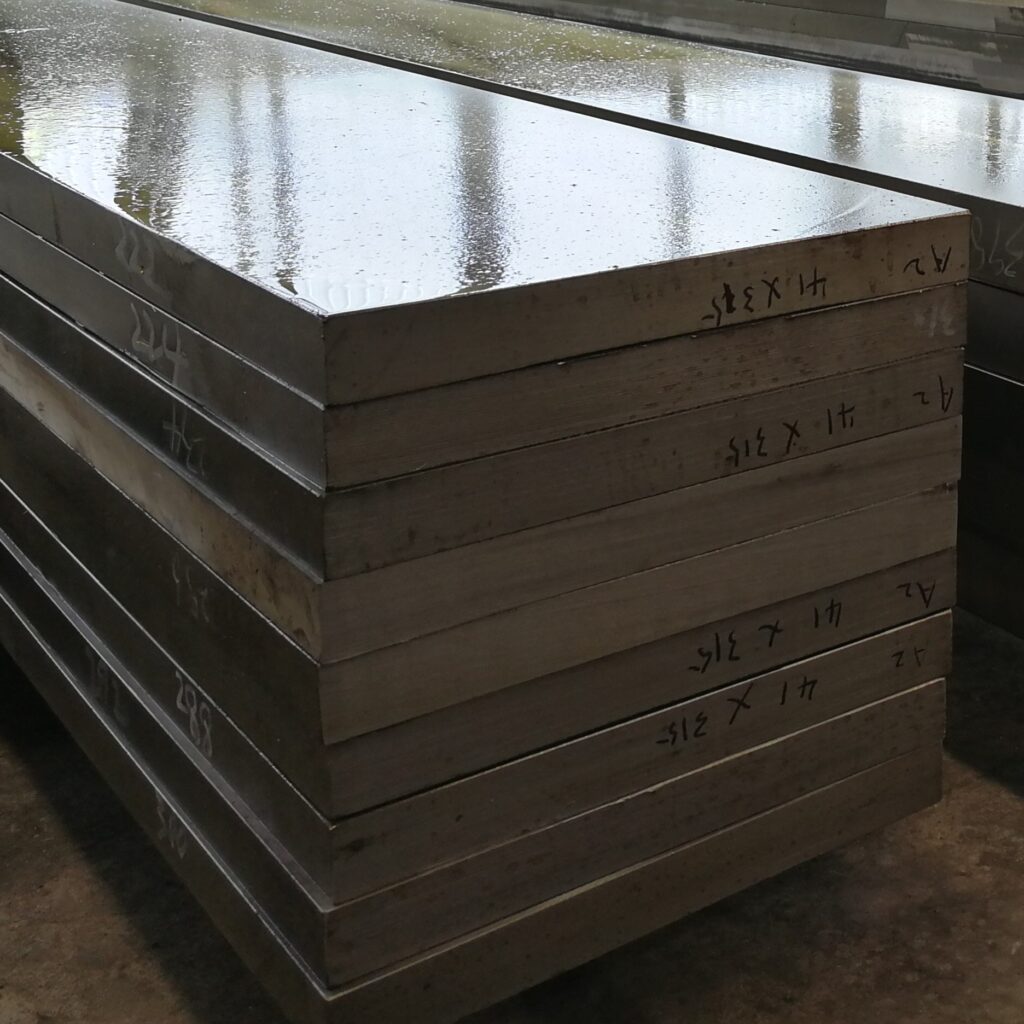
Understanding the Basics: Classification and Purpose
Tool steels are categorized based on their intended use and properties. Both H13 and A2 are well-respected, but they belong to different groups:
H13: The Hot Work Specialist
H13 is classified as a Hot Work tool steel, part of the ‘H’ series in the AISI (American Iron and Steel Institute) system. Specifically, it’s a chromium-based hot-work steel. Its entire design philosophy revolves around maintaining strength and resisting wear and thermal fatigue when things get hot – think forging, die casting, or extrusion.
A2: The Cold Work Performer
A2 falls into the ‘A’ series, designating it as an Air-Hardening, Medium-Alloy Cold-Working tool steel. As the name suggests, it’s engineered for jobs done at or near room temperature. For A2, the priorities are maintaining its shape accurately during heat treatment and providing a good combination of wear resistance and toughness for tasks like stamping, forming, and cutting.
What’s Inside? A Look at Chemical Composition
The distinct properties of H13 and A2 come down to their chemical makeup. The alloying elements are carefully chosen to deliver specific performance characteristics.
H13 Composition Highlights
- Carbon (C): Around 0.35-0.45%. This moderate carbon level contributes to its toughness, which is vital for hot work applications that often involve impact.
- Chromium (Cr): About 5%. Chromium is key for hardenability, corrosion resistance, and high-temperature strength.
- Molybdenum (Mo): Roughly 1.35-1.4%. Mo enhances hot strength, toughness, and hardenability.
- Vanadium (V): Around 1%. Vanadium is crucial for forming hard carbides, which boosts wear resistance, especially at elevated temperatures, and helps refine the grain structure.
- Silicon (Si): Approximately 1%. Silicon improves high-temperature strength and oxidation resistance.
This composition, particularly the balance of Cr, Mo, and V, gives H13 its ability to withstand the rigors of hot work.
A2 Composition Highlights
- Carbon (C): Around 1.0%. This higher carbon content is a primary contributor to A2’s greater hardness and wear resistance in cold work scenarios.
- Chromium (Cr): Also around 5%. Like in H13, chromium aids hardenability and wear resistance.
- Molybdenum (Mo): Typically 1.0-1.1%. Mo contributes to hardenability and toughness.
- Vanadium (V): A smaller amount, usually 0.2-0.25%. While less than in H13, it still plays a role in wear resistance.
A2 generally has a different balance, suited for cold work applications.
The higher carbon in A2 is a significant differentiator, gearing it towards hardness and wear for cold applications.
Heat Treatment: Unlocking Performance
Heat treatment transforms these steels from their softer, machinable state into hard, durable tools. Both H13 and A2 have user-friendly heat treatment characteristics.
Hardening and Hardenability
Both H13 and A2 are air-hardening steels. This is a big advantage. It means they can be hardened by cooling in still air after being heated to their austenitizing (hardening) temperature. Air hardening minimizes the internal stresses that can lead to distortion or cracking, which is especially beneficial for complex tool shapes. Both steels also have good hardenability, meaning they can harden to a significant depth, making them suitable for larger tools.
Tempering and Dimensional Stability
After hardening, tool steels are tempered to relieve stresses and achieve the desired balance of hardness and toughness.
- H13 exhibits secondary hardening. This means that when tempered at higher temperatures (typically around 510°C or 950°F), it actually gains hardness due to the precipitation of fine alloy carbides. This characteristic is vital for its hot work performance, as it helps H13 retain hardness even when exposed to high operating temperatures. It’s often double tempered to ensure stability and toughness.
- A2 also shows a secondary hardening peak, though typically less pronounced than H13. Its main advantage during heat treatment is its excellent dimensional stability. A2 is known for minimal size change and low distortion after hardening and tempering, which is critical for precision tooling.
Surface Treatments
For enhanced surface properties, treatments like nitriding can be applied to both H13 and A2. Nitriding creates a very hard surface layer, significantly improving wear resistance and, in some cases, fatigue strength. H13, in particular, benefits greatly from nitriding for applications like die casting dies, where it faces both high temperatures and abrasive wear.
Key Mechanical Properties: The Nitty-Gritty
Let’s compare some of the most important mechanical properties for a tool user:
Hardness
- A2 is generally used at higher working hardness levels, typically 56-61 HRC (Rockwell C Hardness). This higher hardness is a direct result of its higher carbon content and is ideal for resisting wear in cold work.
- H13 is typically used at working hardness levels ranging from 42-54 HRC, depending on the specific application. For instance, die-casting tools might be in the 44-48 HRC range, while applications requiring more shock resistance might be slightly softer. Its as-quenched hardness is lower than A2’s.
Hot Hardness (Resistance to Softening at Temperature)
This is where H13 truly excels and the primary reason it’s a hot work steel. It retains a significant portion of its hardness even at elevated temperatures (up to around 550°C or 1020°F, and can withstand short exposures even higher). This “red hardness” prevents the tool from softening and deforming when in contact with hot workpiece materials.
A2, being a cold work steel, does not have good hot hardness. Its strength drops off rapidly at temperatures much above 200-260°C (400-500°F), making it unsuitable for hot work.
Toughness
Toughness is the ability of the steel to absorb energy and resist fracture, especially under impact.
- H13 offers excellent toughness and impact strength, particularly for a hot work steel. This is crucial for applications like forging dies that experience repeated impact loads. Its lower carbon content (compared to A2) contributes significantly to this.
- A2 provides good toughness for a cold-worked steel, offering a better balance of toughness and wear resistance than some other cold-worked grades like the D-series. It’s tougher than oil-hardening steels but generally not as tough as dedicated shock-resisting steels (S-series).
Wear Resistance
Wear resistance is the ability to resist abrasion and material loss from friction.
- A2 offers good to high abrasion resistance for cold work applications. Its higher carbon content and the resulting carbides provide this property. It generally sits between the S-series (lower wear resistance) and the D-series (higher wear resistance) tool steels.
- H13 also provides good wear resistance, especially at elevated temperatures. The vanadium carbides in its structure contribute to this. When nitrided, H13’s wear resistance is significantly enhanced. However, for purely abrasive cold wear without high temperatures, A2 would typically have an edge.
Machinability
In their annealed (softened) state, H13 generally offers better machinability than A2. This can be a practical consideration when manufacturing complex tools.
Typical Applications
Understanding their properties helps explain their common uses:
H13 Applications
Given its strength at high temperatures, H13 is the go-to for:
- Die casting dies for aluminum, zinc, and magnesium
- Hot forging dies and punches
- Extrusion tooling (dies, mandrels, liners) for aluminum and brass
- Plastic injection molds, especially for abrasive or high-temperature engineering plastics
- Hot shear blades
- Mandrels and cores
A2 Applications
With its excellent dimensional stability and good balance of wear resistance and toughness, A2 is widely used for:
- Blanking and forming dies
- Coining dies
- Trimming dies
- Shear knives and slitter knives
- Punches and mandrels for long production runs
- Gauges and measuring tools
- Molds requiring high precision
Making the Right Choice for Your Factory
So, when you’re deciding between H13 and A2, the first question to ask is: Will the tool see significant heat in operation?
- If the answer is yes (typically above 200-250°C or 400-480°F), H13 is almost always the better choice. Its ability to retain hardness and strength at elevated temperatures and its good toughness and resistance to thermal fatigue (heat checking) make it ideal for hot work.
- If the application is cold work, A2 is a strong contender. Its excellent dimensional stability during heat treatment means your tools will maintain their precise shape. It offers a good combination of wear resistance and toughness for various stamping, forming, and cutting operations.
Both H13 and A2 are excellent tool steels when used in the proper context. Understanding their fundamental differences in terms of temperature capability, hardness, toughness, and wear resistance will help you select the most effective and cost-efficient material for your factory’s needs.
If you have specific applications in mind or need further guidance, don’t hesitate to reach out. We have extensive experience in tool steel and can help you pinpoint the perfect solution.
Take the Next Step to Superior Steel Solutions!
Our seasoned experts at Aobo Steel are ready to assist you in selecting the perfect tool steel for your specific requirements. Benefit from competitive pricing, unparalleled service, and our extensive industry knowledge.
👇 Fill out the form below to connect with our sales team today! 👇
(You’ll find the contact form just below this section)