What is interchangeable with H11 tool steel? When looking for alternatives to H11 hot-work tool steel, the most common and closely related options are H12 and H13 tool steel. While often used in similar applications, the best choice depends on specific needs: H13 generally offers better wear resistance, while H11 tool steel provides slightly higher fracture toughness, and H12 might be preferred for minimizing warpage in complex designs.
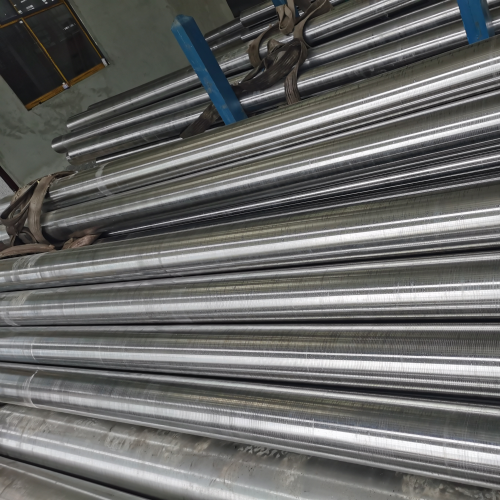
Understanding H11 Tool Steel
H11 tool steel is a staple in the world of hot-work applications. It’s a 5% chromium tool steel known for its excellent performance at elevated temperatures. Here’s what makes it tick:
- Composition: Primarily a 5% chromium hot-work die steel.
- Hardening: It’s an air-hardening steel. This is a significant advantage as it minimizes distortion and residual stress compared to liquid quenching methods.
- Tempering: H11 tool steel benefits from secondary hardening. Tempering it correctly, typically around 510°C (950°F), develops its optimal strength and stability for use in temperatures ranging from 75°C to 540°C (100°F to 1000°F).
- Workability: It’s readily forged and can be welded, although its air-hardening nature requires careful post-weld cooling and annealing procedures.
Typical applications include die casting dies, extrusion dies (for materials such as aluminum and magnesium), and hot forging dies.
Interchangeability: H11 vs. H13 vs. H12
While H11, H12, and H13 belong to the same 5% chromium family and share many applications, “interchangeable” doesn’t mean identical. Subtle differences in composition and properties dictate which grade is best suited for a particular job.
H13: The Popular Counterpart
H13 is arguably the most widely used hot-work tool steel in this group today.
- Similarity: Very close to H11 in composition and heat treatment response. Both offer an outstanding balance of cost-effectiveness, hardenability, and resistance to thermal fatigue.
- Key Difference: H13 typically contains more vanadium than H11. This results in more complex vanadium carbides, giving H13 superior wear resistance.
- Trade-off: H11 generally exhibits slightly better fracture toughness compared to H13.
- Usage: Despite H11’s toughness advantage, H13’s wear resistance often makes it the preferred choice in many modern hot-work tooling applications.
H12: The Stability Specialist
H12 is another close relative within the 5% chromium series.
- Key Advantage: H12 is sometimes recommended over H11, specifically when minimizing warpage and ensuring dimensional stability during heat treatment is critical, especially for complex die shapes.
Making the Right Choice
Selecting between H11, H12, and H13 requires evaluating the specific demands of your application:
- Need Maximum Toughness? H11 might be the edge.
- Need Superior Wear Resistance? H13 is often the go-to.
- Dealing with Complex Geometries Prone to Warpage? H12 could offer better stability.
While other grades, such as H14, H19, or different series like A8 or D2, exist for specialized hot-work or specific wear requirements, H13 and H12 remain the primary functional alternatives to H11 for a broad range of die casting, extrusion, and forging tasks. Understanding these nuances helps ensure you select the most effective and durable material for your tooling needs.
Get a Quick Quote + Free Technical Support for H11 Tool Steel!
- 🔹 Direct Factory Price — Save your cost from the source.
- 🔹 Professional Support — Over 20 years of forging and technical expertise.
- 🔹 Sample Available — Small pieces available for quality checking.
- 🔹 Priority Shipping — Fast delivery arrangement for urgent needs.
👇 Send us your size and quantity now. We will reply within 12 working hours!👇