What are the D2 tool steel disadvantages? While D2 tool steel is highly regarded for its excellent wear resistance in cold-work applications, it presents challenges including difficult machining and grinding, moderate toughness, potential dimensional instability due to retained austenite after heat treatment, susceptibility to quench cracking, and significant difficulty in welding. Understanding these limitations is crucial for selecting the right material.
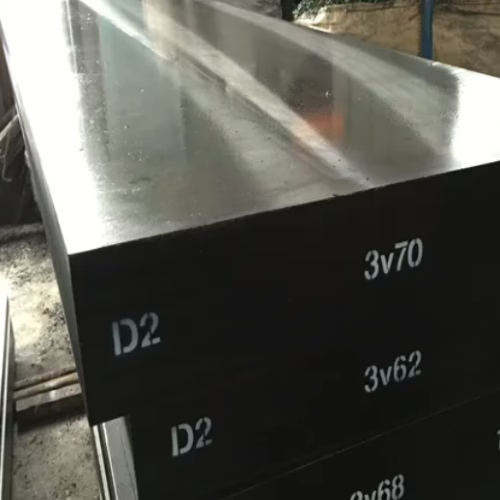
Working with D2 Steel: Machinability and Grinding
Let’s get straight to the point. D2 steel, a high-carbon, high-chromium air-hardening tool steel, is known for its exceptional abrasion resistance. That’s its strength. However, this same composition, particularly the high chromium (around 11.50%) and carbon (around 1.50-1.55%), makes it tough to work with.
Machining Challenges
Compared to a standard 1% carbon steel (rated 100 for machinability), properly annealed D2 scores only about 45. This means more time and effort are required in the workshop. Its high alloy content contributes significantly to this difficulty. If ease of machining is a top priority, D2 might not be the best fit. Click here for more information about Why is D2 tool steel so hard to sharpen?
Grinding Considerations
The same factors that make machining difficult also apply to grinding. The high wear resistance means it resists material removal, which can complicate grinding operations.
Toughness Limitations
While D2 offers good wear resistance, its toughness is generally considered moderate or fair. It holds up well in many applications, but if your project demands significantly higher toughness, D2 might fall short. Trying to increase toughness by greatly lowering hardness isn’t typically effective and can make heat treatment control difficult. For high-toughness needs, looking at alternative steel grades specifically designed for that property is often a better strategy.
Heat Treatment and Dimensional Stability
D2 is an air-hardening steel, known for relatively good dimensional stability during the hardening process compared to some other tool steels. However, there are still important factors to consider.
Retained Austenite
A key technical point is the potential for retained austenite after standard heat treatment, sometimes as much as 20%. This retained austenite isn’t stable and can transform over time at room temperature, causing dimensional changes. For applications requiring extremely tight tolerances, this instability can be problematic.
Quench Cracking Susceptibility
Air-hardening steels like D2, due to their complex structure designed for wear resistance, tend to be more susceptible to quench cracking than typical oil-hardening grades. Careful process control is essential.
Resistance to Softening and Tempering
D2 offers fair resistance to softening at elevated temperatures. Tempering choices are important: tempering around 515°C (960°F) maximizes wear resistance but can introduce some temper embrittlement. If better toughness is the goal, tempering lower, around 205°C (400°F), is recommended.
Welding Difficulties
Welding is often necessary for factory maintenance or modifications. Be aware that D2 tool steel is notoriously difficult to weld using conventional methods. Its high carbon and carbide content make it very sensitive to cracking. If welding absolutely cannot be avoided, it demands extreme caution and specific procedures, often involving lower preheat temperatures than standard.
Conclusion: Is D2 Right for Your Application?
D2 tool steel is a valuable material for its wear resistance in long production runs, especially in cold-work tooling. However, its disadvantages – challenging machinability/grinding, moderate toughness, potential dimensional shifts from retained austenite, quench crack sensitivity, and welding difficulties – must be carefully weighed against your specific operational needs, part geometry, and tolerance requirements.
At Aobo Steel, with over 20 years of forging experience, we understand these nuances. We can help you evaluate if D2 is the optimal choice or guide you towards other tools or alloy steels that might better suit your application. Let’s talk about your requirements.