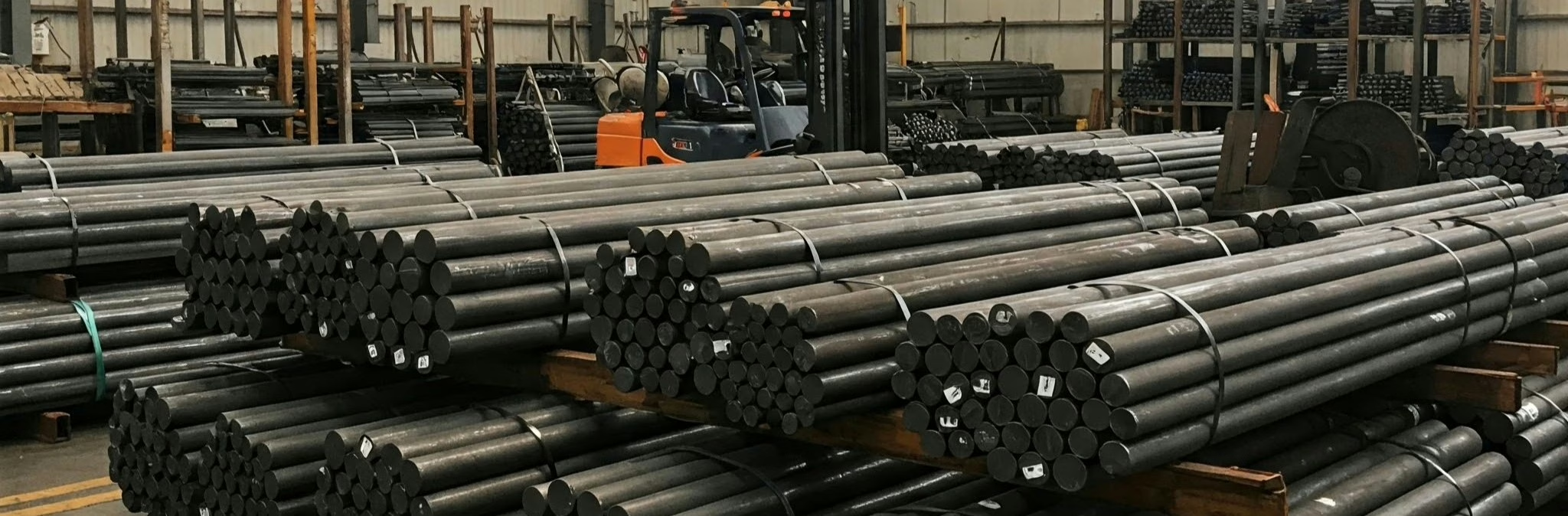
This section explains the importance of selecting tool steel to help our customers choose the right steel for different tooling applications.
First, refer to the article in our blog that explains “What is tool steel.” Then, consider how to choose tool steel.
Importance of Tool Steel Selection
The first step in selecting a tool steel is to confirm its intended application. For example, a drill is used for drilling holes, so it needs to be wear-resistant and resistant to high temperatures. Another example, a punch is used for stamping or shearing, so naturally the material needs to be both wear-resistant and tough (high toughness means it won’t break easily).
Let’s divide tool steel into six categories, according to their applications:
- Cutting: Wear-resistant and heat-resistant steel is needed for drills and milling cutters.
- Shearing and punching: For punches and molds, shear steel or punching must meet the requirements of wear resistance and toughness.
- Molding: Such as plastic molds, forging molds, and steel molds, should be easy to process, and can be polished smoothly.
- Stretching and extrusion: Such as aluminum frames, cold-drawn steel bars, wear-resistant, and not easy to deform.
- Rolling: Rolling round bar, flat plate, wear-resistant, heat-resistant requirements.
- Miscellaneous: hammering, filing, and scraping, with specific needs for each application.
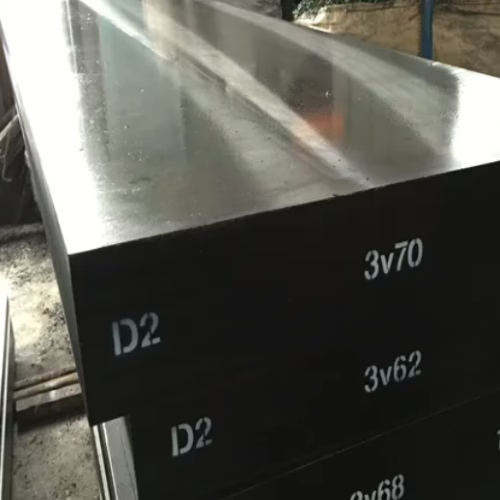
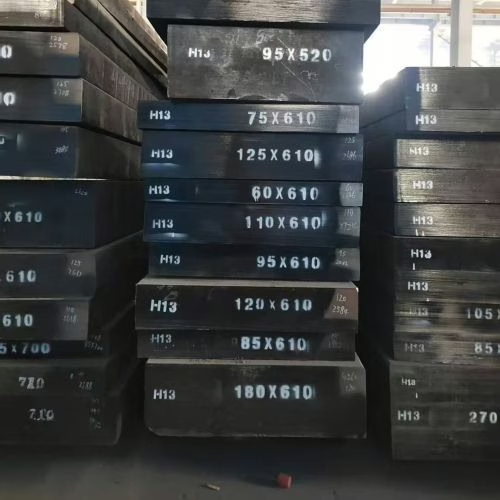
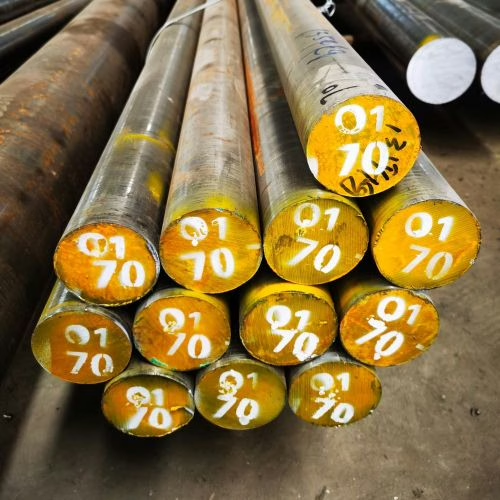
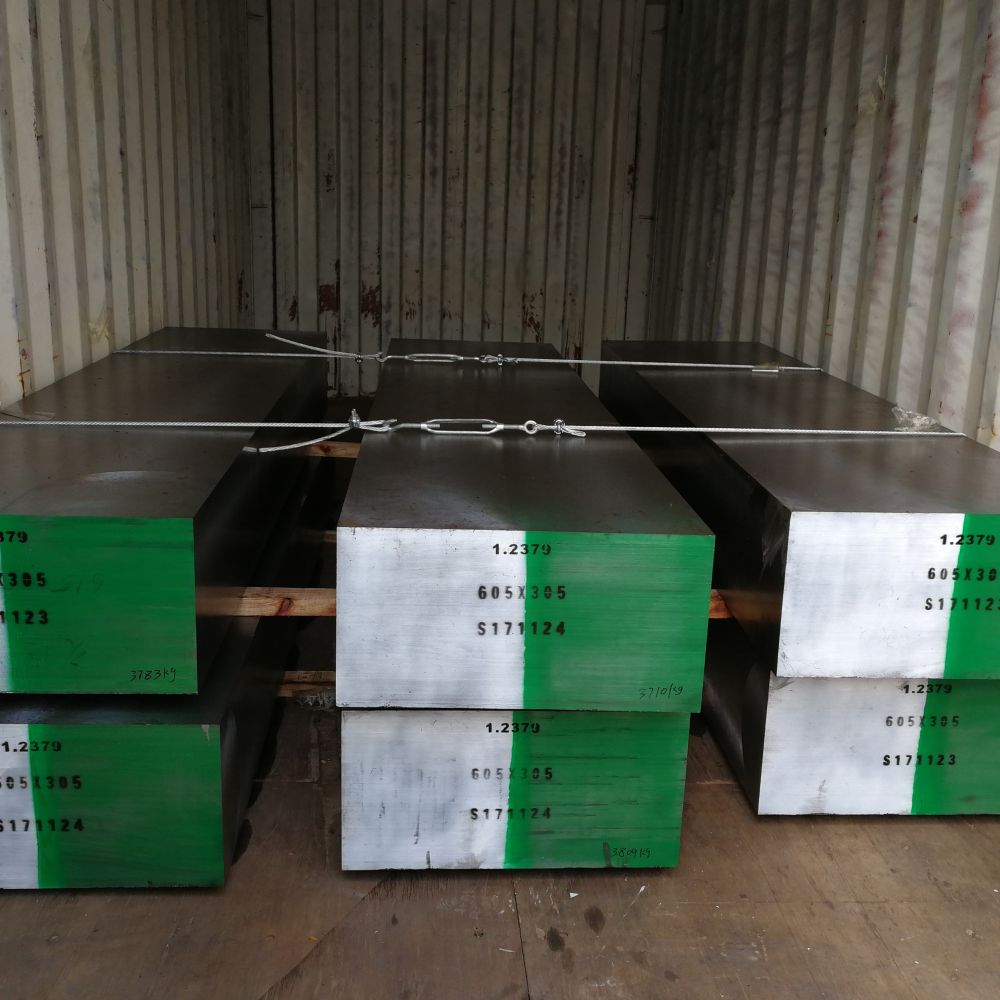
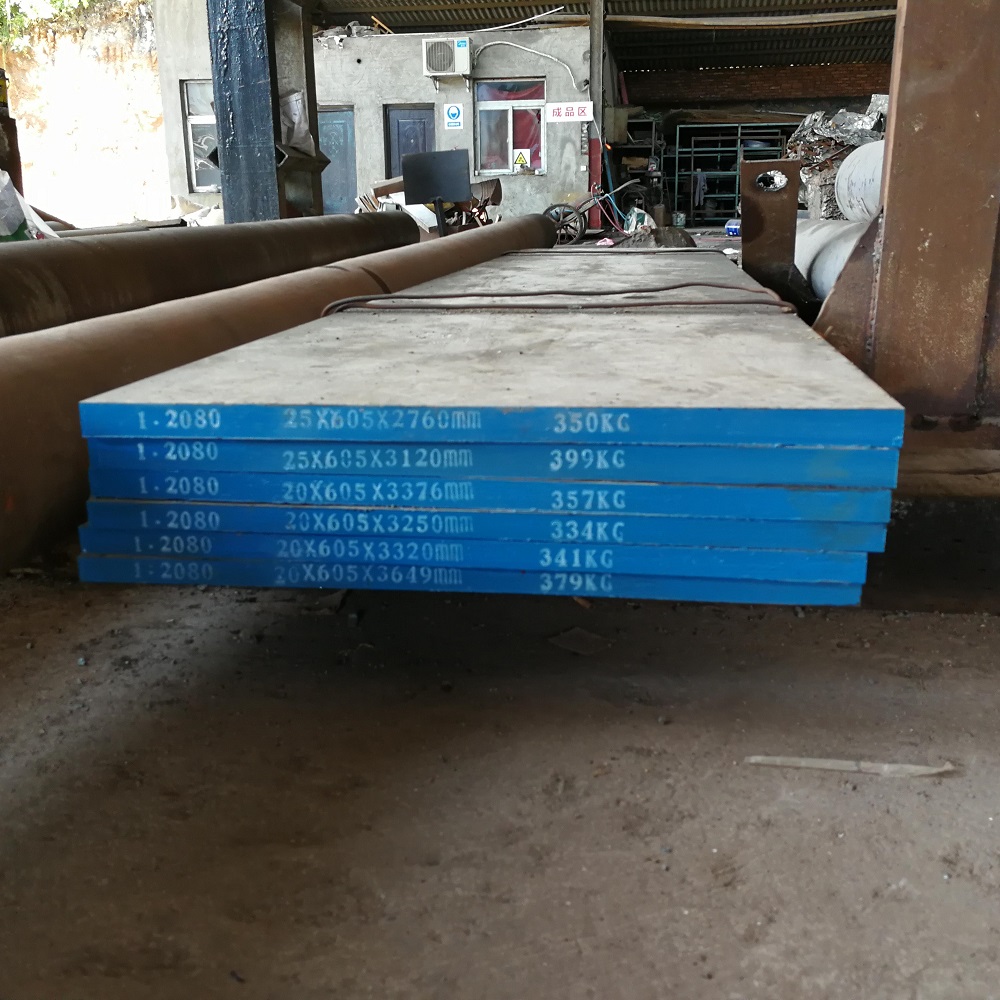
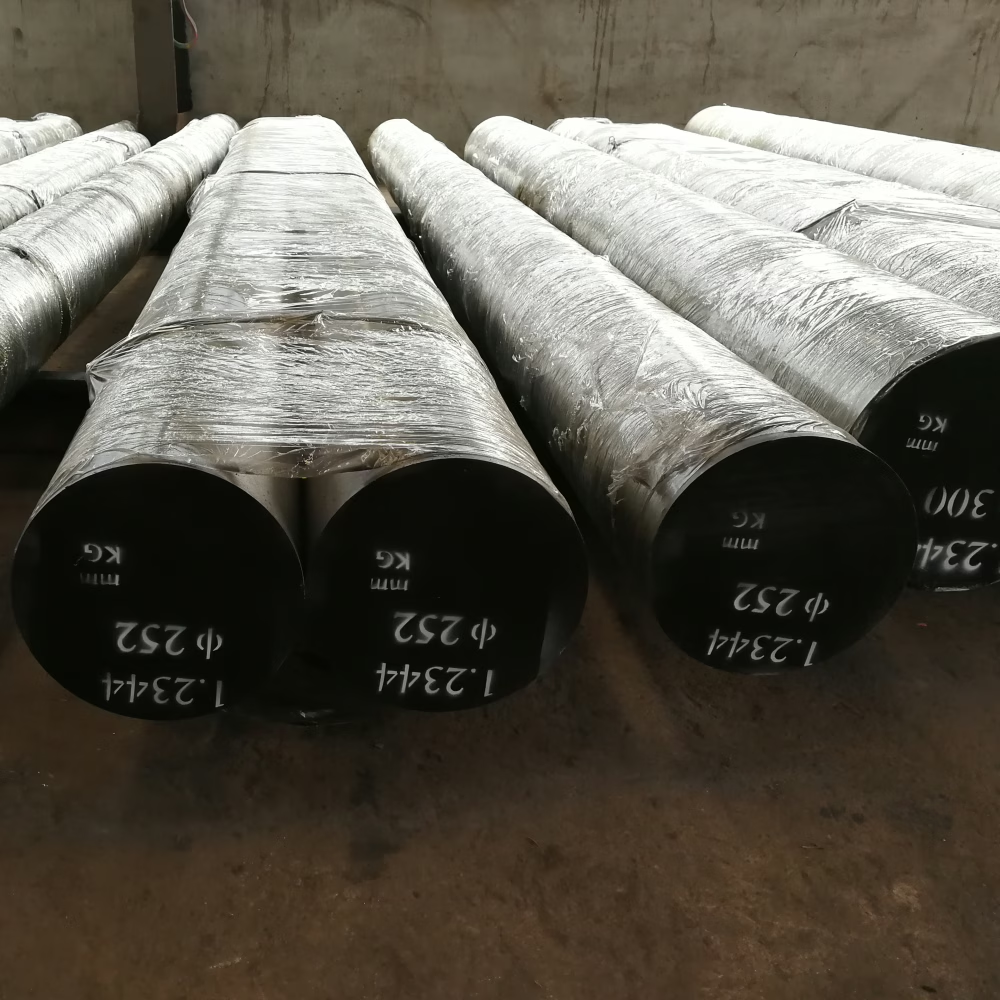
Performance characteristics of tool steel
We divide tool steel properties into primary and secondary properties:
Primary Properties
These are the core characteristics of the steel:
- Wear Resistance: The ability of the steel to resist wear and tear. For example, cutting tools need to stay sharp for a long time.
- Toughness: Steel can resist fracture. For example, the punch needs to withstand the impact.
- Heat resistance: Steel can also maintain performance at high temperatures. For example, high-speed drill bits will be affected by friction heat.
Hardness is also a very important point, but it is not one of nature’s properties. It needs the right heat treatment to adjust. The higher the hardness, the less deformable it is, making it suitable for high pressure.
Secondary Properties
These are characteristics that affect the tool-making process:
- Machinability: the material can be easily machined into the tool’s shape.
- Grindability: How easily the steel can be ground (polished).
- Polishability: whether the material can be polished smoothly, such as plastic molds needing a smooth surface.
- Safety in Heat Treatment: Heat treatment of steel can increase its susceptibility to cracking.
- Distortion in Heat Treatment: The shape of the material after heat treatment changes greatly.
- Heat Treating Range: The range of heat-treating temperatures that steel can accept.
- Availability: This material is not readily available on the market.
- Price: the cost is not high, of course.
Trade-offs in selecting tool steel
When choosing a tool steel, there is a trade-off between properties: increasing wear and heat resistance usually decreases toughness, while increasing toughness may deteriorate wear and heat resistance.
For example, a punch that needs to be wear-resistant might be made of A2 steel, but it is not tough enough and is prone to cracking. If we changed to S7 steel, which has better toughness and is less prone to deformation during heat treatment, the wear resistance would be worse than that of A2.
That’s why we say no one steel is perfect for all needs. According to the application, the best combination of primary and secondary properties is important.
Example of tool steel selection
When stamping 3/8-inch thick steel plates with A2 steel, the problem of edge cracking may stem from its lack of toughness. Although A2 steel has good wear resistance, it appears weak when subjected to impact. To fix this problem, let’s consider choosing the more ductile L6, A8, S1, S5, or S7 steels. S7 steel may be superior due to its heat-treatment safety and low distortion. However, the trade-off is that S7 steel has reduced wear resistance compared to A2 steel, which may lead to faster wear. It’s a mouthful. Therefore, in practice, no one steel is 100% perfectly suited to all situations and must be selected based on the application.
Other considerations
In addition to selecting tool steel, it is important to consider whether the tool design is appropriate. Let me give you an example of whether the shape of the punch is suitable. Is the heat treatment process correct, and do the temperatures and times affect performance? Whether the tool is properly used and maintained, and whether it is adequately serviced. In addition to tool steel, consider materials such as martensitic aging steels, steel-jointed carbides, and copper-beryllium alloys. Simply replacing the steel will not necessarily solve the problem; a thorough examination and analysis are necessary.
To summarize
Tool steel selection aims to achieve the lowest cost per product or the fewest production problems with the most appropriate tool steel. However, tool steel is not a panacea and cannot be expected to never break down. When selecting steel, a combination of use, performance, and cost needs to be considered, and full communication with the steel supplier, the tool manufacturer, and the heat treatment specialist is very important. Feel free to contact us. Our company offers the most common tool steels on the market. For more information, please click on tool steels.