Among our products, the following materials can be used for cold work dies and punches.

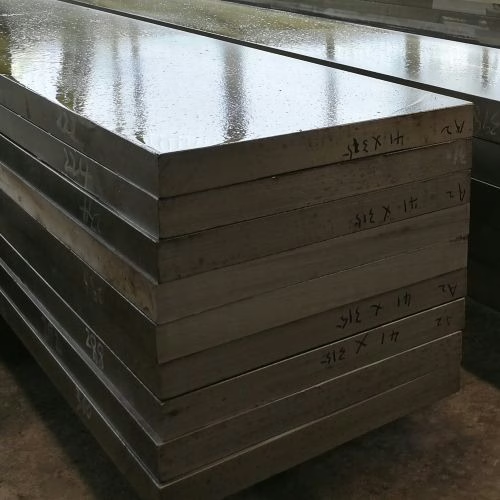
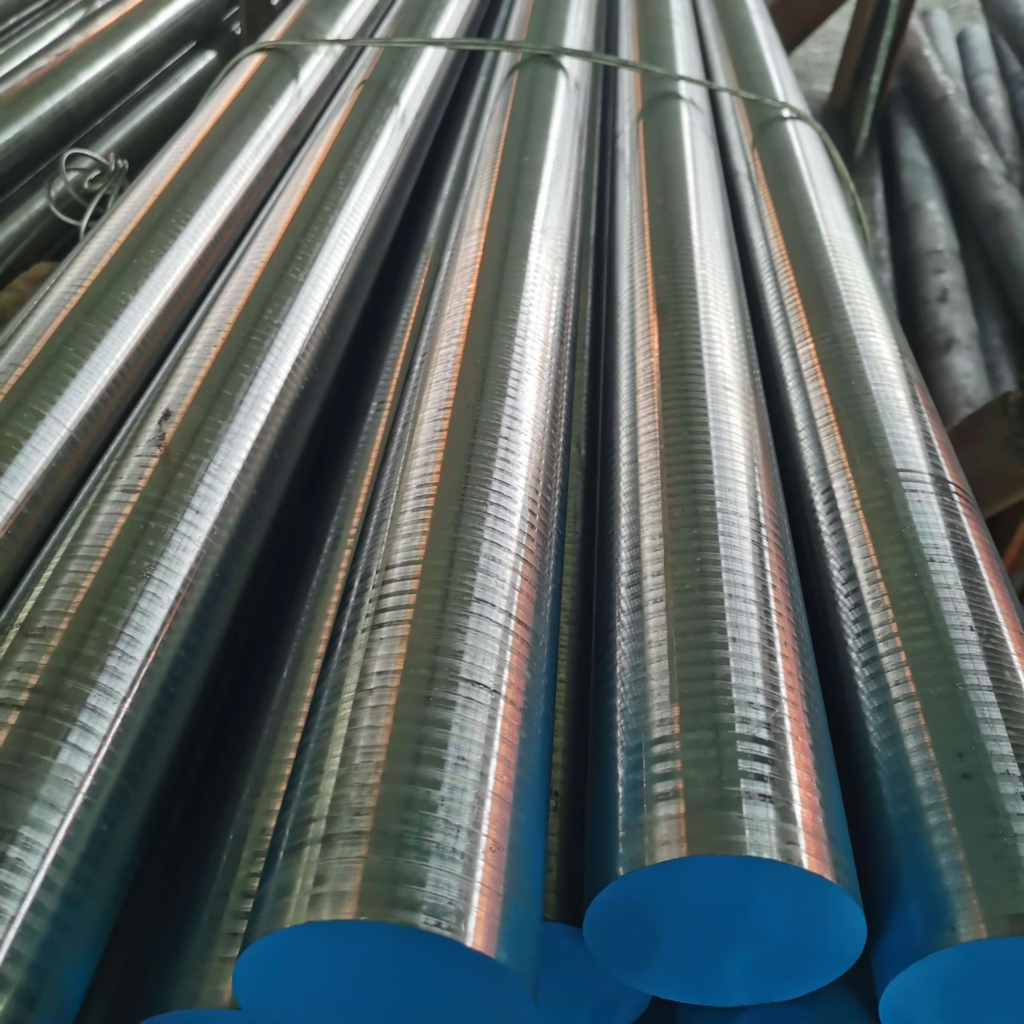
What are cold work dies and punches?
Cold work dies and punches are common tools used in manufacturing to work with metal, such as cutting out shapes or pressing metal into specific shapes. “Cold work” means that these tools work at room temperature, unlike ‘hot work,’ which requires metal heating. Because there is no high temperature to soften the metal, the tool steel must be strong to withstand stress and wear.
Different cold work applications require different types of steel:
- Some require the steel to be very wear-resistant (high abrasion resistance to last longer).
- Some need the steel to be tough (high toughness, not prone to cracking).
- Some may need a balance of both.
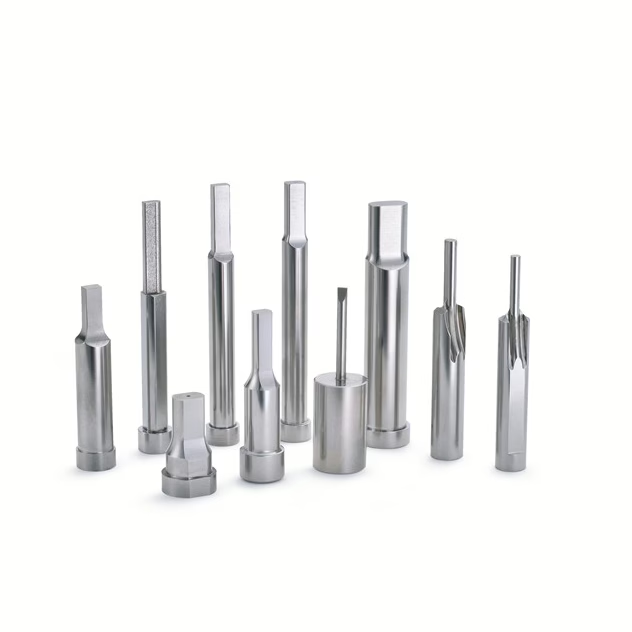
Selection of Steels for Cold-Work Dies and Punches
The selection of materials for cold work dies and punches centers on balancing wear resistance and toughness depending on the application:
- Use simple steel (e.g. W1, O2) for small molds.
- Advanced steels (e.g. A2, D2) for large molds or high requirements.
- Impact-resistant steels for thick materials (e.g. S1, S5).
- Cost and punch ratio should also be considered.
What are wear resistance and toughness?
The two most important properties when choosing steel are wear resistance and toughness:
- Wear resistance is the ability of steel to resist friction or wear. Tools always rub against metal, and they will soon wear out if they don’t have good abrasion resistance.
- Toughness: the ability of steel to absorb energy without breaking when a force is applied. For example, a tool may crack if it is hit suddenly and has low toughness.
Comparison of steel ratings
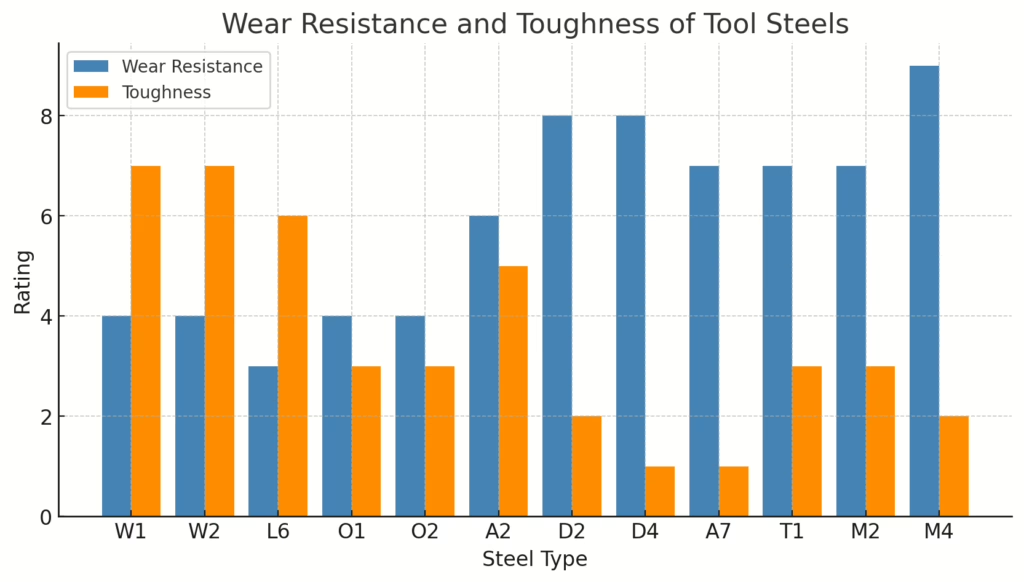
W1 and W2: Toughness is the highest (7), and abrasion resistance is medium (4).
A7 and D7: highest abrasion resistance (9), but very low toughness (1 or 2).
A2: more balanced abrasion resistance (6) and toughness (5).
D2 and D4: very high abrasion resistance (8) but low toughness (2 or 1).
Characteristics and uses of different steels
Different steels are suitable for different situations:
1. water-hardening steels. W1, W2: These steels are hardened by water quenching (heating and cooling in water). They are characterized by high toughness, medium wear resistance, low cost, and suitability for small molds.
2. Oil-hardened steels, such as O1, O2, are characterized by wear resistance and toughness, and are medium, suitable for small and medium-sized molds
3. Air-hardening steels, such as A2, D2, and D4, are cooled and hardened in air, with small dimensional changes, suitable for large parts. A2 has a balance of wear resistance and toughness and is commonly used in punched parts up to 76.2 mm (3 inches) in width. D2 and D4 have high wear resistance but low toughness and are suitable for molds that must be abrasion-resistant.
4. High-speed steel, such as M2 and M4, contains tungsten, molybdenum, and other alloys. Its wear resistance is very high, but its toughness is low. Thus, it is suitable for high-speed cutting tools or for ultra-wear-resistant occasions.
5. Impact-resistant steel such as S1 and S5, when the thickness of the material is more than 6.35 mm (0.25 inches), with S1 or S5, are suitable for machining thick material molds.
Key factors in choosing steel
There are several things to look at when selecting steel:
1. Size
- Small molds: W1, W2, or O1 is sufficient.
- Use air-hardening steels such as A2 and D2 for large molds (e.g., punched parts with a width of 76.2 mm).
2. Requirements for use
- If you need wear resistance (lasting a long time), choose D2, D4, A7, and D7.
- If you need toughness (impact resistance), select W1, W2, S1, or S5.
- Balance performance: choose A2.
3. Cost
- The cost of steel is not a high percentage of the total cost of the tool. For small production runs, the D2 cost is about 10%; for thicker material (12 mm), it may be 50%.
- Although high-grade steel is expensive, it may be more cost-effective with good performance.
4. Punch and material ratio
- The ratio of punch diameter to material thickness affects steel selection
- Smaller ratios, higher tool pressures, and higher toughness are required.