At Aobo Steel, with our extensive experience in tool steel solutions, we understand the critical role the right material plays in your operations. If you’re exploring S7 tool steel properties, you’re likely looking for a material that offers a unique combination of toughness and versatility. S7 tool steel is a popular choice for demanding applications, and this guide will provide you with the essential technical details to determine if it meets your factory’s specific needs.
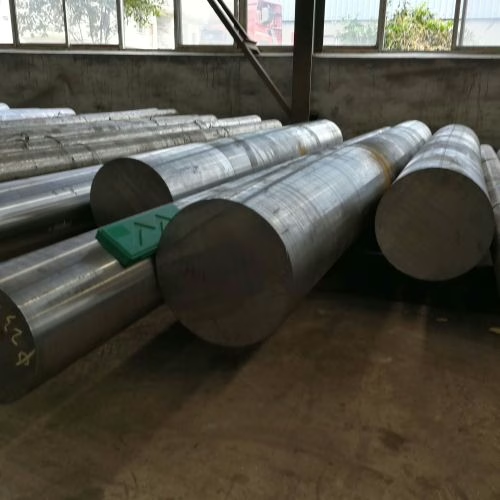
1. Understanding S7 Tool Steel: Classification and Chemical Makeup
To fully appreciate the capabilities of S7, it’s important to understand its classification and what goes into its composition. These factors are fundamental to its renowned performance characteristics.
1.1. Classification of S7 Tool Steel
S7 is primarily recognized as a Shock-Resisting tool steel, indicated by the ‘S’ in its designation. This highlights that superior toughness is a primary design consideration. Additionally, S7 is categorized as an Air-Hardening tool steel. It also falls within the group of hot work tool steels, demonstrating a notable degree of heat resistance.
1.2. Chemical Composition of S7 Tool Steel
The specific S7 tool steel properties directly result from its carefully balanced chemical composition. The key elements include:
Element | Approximate Percentage (%) | Contribution |
Carbon | 0.50 | Influences hardness and wear resistance |
Silicon | 0.25 – 0.50 | Contributes to strength and hardenability |
Manganese | 0.70 | Aids in hardenability and deoxidation |
Chromium | 3.25 | Enhances hardenability and wear resistance |
Molybdenum | 1.40 – 1.50 | Improves deep hardening and hot hardness |
The presence of chromium and molybdenum is particularly significant for S7’s deep hardening capabilities. Notably, the molybdenum content allows S7 to maintain minimal hardness loss even at operational temperatures up to 1,000°F (540°C). Compared to O1 tool steel, S7 has a lower carbon content. Unlike D-grade tool steels, S7 (similar to O1 and S1) has practically no undissolved carbides due to its lower chromium and carbon content, meaning its properties are more governed by the matrix composition.
2. Key S7 Tool Steel Properties
Understanding the core S7 tool steel properties will help you leverage its strengths in your manufacturing processes.
2.1. Exceptional Toughness and Shock Resistance
Exceptional toughness and shock resistance are standout S7 tool steel properties. It boasts the highest shock resistance rating among all tool steels and is considered to have very high to highest toughness within the shock-resisting group. This powerful combination of high toughness and fracture resistance makes S7 an excellent choice for applications involving impact loading, complemented by good strength and wear resistance. It is consistently rated as having “very good toughness.”
2.2. Reliable Wear Resistance
S7 tool steel offers good wear resistance. While its wear characteristics are generally considered somewhat less than O6 tool steel, they are superior to those of 4140/4150 alloys. When compared to other air-hardening grades, S7 typically has less wear resistance than A2 or D2 tool steels. The wear resistance is influenced by the hardness of the martensitic matrix and the amount and type of any undissolved carbides. As mentioned, S7 has minimal undissolved carbides.
2.3. Performance at Elevated Temperatures: Hot Hardness and Heat Resistance
A critical property for certain applications, S7 can withstand temperatures up to 1,000°F (540°C) with minimal softening. Shock-resisting steels like S7 generally exhibit good resistance to softening at elevated temperatures.
2.4. Hardenability and Through-Hardening Capabilities
As an air-hardening steel, S7 possesses higher hardenability than water-hardening grades. It can be achieved through-hardening (uniform hardness throughout the cross-section) by air quenching in sections up to 2 1/2 inches (63.5 mm) thick. For larger cross-sections, achieving full hardness by air cooling may not be possible, and alternative cooling methods might be necessary.
2.5. Dimensional Stability in Heat Treatment
S7 is known for its excellent dimensional stability during heat treatment, exhibiting low distortion. When air quenched, it is expected to expand approximately 0.001 inch per inch. Air quenching is preferred as it helps minimize distortion and promotes this stability.
2.6. Machinability of S7 Tool Steel
When properly annealed, S7 tool steel has a good machinability rating. It is generally rated at 70 (compared to a 1% carbon steel baseline of 100), with some sources suggesting a rating as high as 95. It is noted to machine slightly better than O1 tool steel.
3. Heat Treatment Guidelines for S7 Tool Steel
Proper heat treatment is crucial to unlocking the optimal S7 tool steel properties. At Aobo Steel, we emphasize adherence to precise heat treatment protocols.
3.1. Hardening Process
- Hardening Temperature: Typically 1,725°F (941°C).
- Soak Time: Generally 1 hour per inch of thickness.
- Quenching: Air quenching is the standard method.
3.2. Tempering Recommendations
Multiple tempering cycles are recommended for S7 to achieve the desired balance of hardness and toughness.
- General Use: A first temper at 450°F (230°C) followed by a second temper at 425°F (220°C) is often suggested. The recommended tempering range for general use is 400-450°F (204-232°C).
- Duration: Each tempering cycle should last for 2 hours per inch of thickness.
- Hot Work Applications: For tools used in hot work, temper at a temperature 25-50°F (14-28°C) above the expected working temperature of the tool.
3.3. Annealing Protocol
- Heating: Heat to 1,550°F (843°C).
- Soaking: Soak for 1.5 hours per inch of thickness.
- Cooling: Cool slowly at a rate of 25°F (14°C) per hour down to 900°F (482°C).
- Final Cooling: After reaching 900°F, the steel can be air-cooled to room temperature.
3.4. Protective Measures During Heat Treatment
To prevent decarburization (loss of carbon from the surface), annealing and hardening processes should ideally be conducted in a controlled atmosphere, vacuum furnace, or neutral salt bath furnace.
3.5. Stress Relief Considerations
A stress-relief temper is strongly recommended after significant machining, welding, or Electrical Discharge Machining (EDM). This is typically performed at a temperature 25-50°F (14-28°C) below the last tempering temperature used.
4. Achievable Hardness Levels with S7 Tool Steel
The hardness of S7 tool steel can be tailored through heat treatment to suit various applications.
Hardness Type | Typical Value(s) | Notes |
Working Hardness | 56-58 HRC | Best working range often achieved by tempering at 450°F (230°C), yielding ~58 HRC. |
As-Quenched Hardness | 59-60 HRC | Maximum obtainable hardness is typically 60 HRC. |
Annealed Hardness | Approx. 230 HB (Brinell) | Maximum hardness in the annealed state. |
It’s also possible to case harden S7 after heat treatment to increase surface hardness up to approximately 64 HRC. However, it’s important to note that this process will reduce its inherent shock resistance.
5. Typical Applications: Where S7 Tool Steel Excels
The versatile S7 tool steel properties, particularly its exceptional toughness, make it suitable for a wide array of applications:
- Medium Cold-Work Tools and Dies: Including punches, cold forming dies, and shear blades.
- Plastic Molding Dies: Valued for its durability and ability to withstand molding pressures.
- Medium Hot-Work Dies: When tempered appropriately for heat resistance.
- Impact Tools: Such as chipping chisels, rivet sets, and knock-out pins.
- Component Parts: Including grippers and other parts requiring high shock resistance.
In summary, S7 tool steel offers an excellent balance of very high toughness and shock resistance, combined with good wear resistance and moderate hot hardness. Its good dimensional stability and machinability further enhance its utility, especially in applications involving impact or moderate operational heat.
6. Discuss Your S7 Tool Steel Requirements with Aobo Steel
Understanding the specific S7 tool steel properties is key to leveraging its full potential. If you have particular applications in mind, require further technical details, or need to compare S7 with other grades for your factory’s needs, Aobo Steel is here to assist. Our expertise ensures you select the right material for optimal performance.
Contact us today to discuss your S7 tool steel requirements.
Unlock the Potential of S7 Tool Steel for Your Applications!
Experience the superior toughness, impact resistance, and machinability of our premium S7 Tool Steel. Whether you need it for chisels, punches, or high-impact tooling, Aobo Steel delivers quality you can trust. With over 20 years of forging expertise, we are your reliable partner.
Ready to discuss your S7 requirements or get a personalized quote?
Simply fill out the form below, and our specialists will get back to you promptly!