Understanding S7 tool steel hardness is crucial for factory operations using S7 tool steel. Aobo Steel offers this guide to help you maximize S7’s performance in your applications by detailing its essential hardness properties. We provide a free download for the S7 tool steel hardness PDF at the bottom of the page.
1. What is S7 Tool Steel?
S7 tool steel is an air-hardening, shock-resisting steel known for exceptional impact strength. Its versatility suits:
- Medium cold-work tools and dies
- Shear blades
- Medium hot-work dies
- Component parts needing high shock resistance
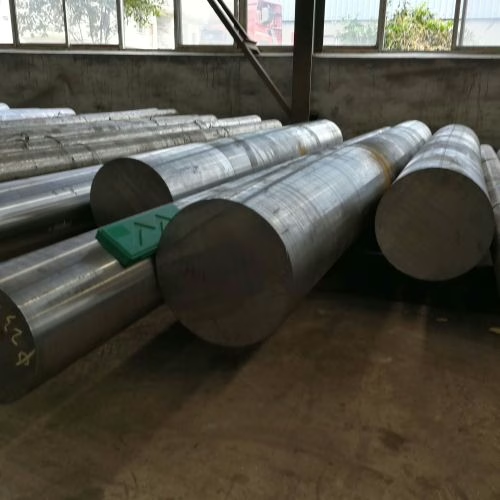
2. Key Hardness Properties
S7’s hardness is adjustable through S7 tool steel heat treatment. Key values include:
2.1 Annealed Hardness: The Starting Point
In its annealed state, it typically has 192 to 223 Brinell Hardness (HB), sometimes up to 230 BHN. This state is for machining before hardening.
2.2 As-Quenched Hardness: Maximum Potential
When air quenched, S7’s surface hardness reaches 59–60 Rockwell C Hardness (HRC). The maximum obtainable as-quenched S7 tool steel hardness is generally 60 HRC.
2.3 Recommended Working Hardness: Balancing Strength and Toughness
The optimal balance for S7 is a working hardness of 56–58 HRC, though 50-56 HRC is also used. This S7 tool steel hardness is achieved by tempering after quenching.
Tempering Temperature | Approximate Rockwell C Hardness (HRC) | Key Characteristics Achieved |
400–450 °F (204–232 °C) | 56–58 HRC | Optimal balance of toughness and strength |
Significantly Higher Temps | Varies (e.g., 46 HRC at 1100°F/595°C) | Increased ductility, reduced wear resistance |
Note: Refer to specific heat treatment guides for precise parameters.
Tempering to 58 HRC hardness often provides the best combination of S7’s toughness and strength.
2.4 The Impact of Higher Hardness Levels
Increasing S7 tool steel hardness (e.g., 60–61 HRC) reduces its toughness, making it more prone to chipping or cracking under shock loads.
2.5 Case Hardening S7 Tool Steel: Surface Enhancement
S7 can be case hardened (e.g., nitriding) after primary heat treatment, increasing surface hardness up to 64 HRC. This improves wear resistance but can reduce core shock resistance.
2.6 Through-Hardening Capability of S7 Tool Steel
S7 is a deep-hardening steel, fully through-hardening up to 2.5 inches (63.5 mm) sections when air quenched. Larger sections may not achieve full S7 tool steel hardness throughout.
2.7 Hot Hardness at Elevated Temperatures
S7 maintains good hardness at elevated temperatures due to its molybdenum content, suiting it for medium hot-work applications. It withstands up to 1000°F (540°C) with minimal hardness loss. Tempering at 1100°F (595°C) yields about 46 HRC.
For more S7 properties, please click S7 tool steel properties.
3. Achieving Optimal Hardness in Your Operations
Precise heat treatment control is vital for S7 performance.
3.1 Tempering Recommendations for S7 Tool Steel
- Target Working Hardness: Aim for an S7 tool steel hardness of 56-58 HRC for the best toughness/strength balance.
- Tempering Range: Typically 400–450°F (204–232 °C) after quenching.
- Consult Experts: Use detailed heat treatment data or consult a metallurgist.
3.2 Considerations for Section Size
For sections over 2.5 inches (63.5 mm), discuss requirements with your steel supplier to ensure the desired core hardness.
4. Your Partner for S7 Tool Steel
Aobo Steel leverages extensive experience to support clients. Understanding S7 tool steel hardness is fundamental to its successful application. We provide quality S7 and technical insights for optimal results.
Contact our experts for questions about S7 tool steel hardness or material selection.
Unlock the Power of S7 Tool Steel for Your Applications
Discover the exceptional toughness, superior impact resistance, and excellent machinability of our premium S7 tool steel. Aobo Steel is dedicated to providing high-quality S7 solutions tailored to your precise engineering needs.
Ready to elevate your project? Fill out the form below to connect with our S7 steel specialists and receive your competitive, no-obligation quote today!