P20 steel is an AISI (American Iron and Steel Institute) type, medium-alloy mold steel. It is commonly supplied in a prehardened condition, with hardness ranging from approximately 28 to 40 HRC, or around 300 HB, and is also known by DIN 1.2311. The primary uses are Plastic molds, Zinc die-casting dies, and Holder blocks. This article focuses on the P20 steel hardness.
1. Why is Hardness Critical to P20 Steel
In the application of P20 steel in molds and stamping dies, hardness is a very important property. It is mainly reflected in the following aspects:
- Resistance to Deformation and Wear: Adequate hardness enables the steel to withstand the high loads and pressures encountered during molding, preventing plastic deformation. For processing abrasive plastics, sufficient hardness provides the necessary wear resistance to prolong tool life.
- Machinability: P20 is typically supplied in a prehardened state that offers a balance of hardness for application and ease of machining, allowing intricate mold cavities to be created without additional high-temperature heat treatment.
- Polishability: High surface hardness, which can be enhanced by carburization, is essential for achieving the smooth, critical finishes required for transparent plastic molds.
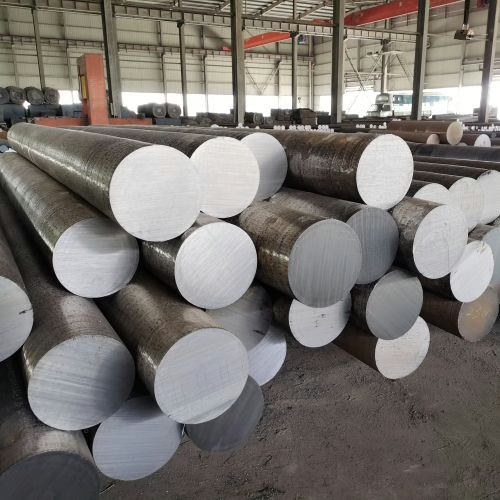
2. Factors Influencing P20 Steel Hardness
2.1 Chemical Composition
P20 steel composition is
Carbon (C) | Manganese (Mn) | Silicon (Si) | Chromium (Cr) | Molybdenum (Mo) | Phosphorus (P) | Sulfur (S) |
0.28 – 0.40 | 0.60 – 1.00 | 0.20 – 0.80 | 1.40 – 2.00 | 0.30 – 0.55 | ≤ 0.030 | ≤ 0.030 |
P20 is a low-alloy tool steel, with its chemical makeup being pivotal for its properties. Key Alloying Elements and Their Contribution to Hardness and Properties:
- Carbon (C): 0.28-0.40%. Influences hardness and strength.
- Chromium (Cr): 1.40-2.00%. Enhances wear resistance and corrosion resistance. The presence of Chromium enhances toughness and hardness.
- Molybdenum (Mo): 0.30-0.55%. Refines grain structure, improving toughness and weldability.
- Manganese (Mn): 0.60-1.00%. Assists in deoxidation, enhances tensile strength without brittleness.
- Silicon (Si): 0.20-0.80%. Assists in deoxidation, enhances tensile strength without brittleness.
- Phosphorus (P) and Sulfur (S): ≤ 0.03% (max). Minor amounts contribute to overall performance. After adding an appropriate amount of S element, the improved P20S steel has better processing performance.
- Nickel (Ni): After adding Ni alloy, the improved steel P20Ni (1.2738) can significantly improve toughness and ductility, which is conducive to processing.
2.2 Heat Treatment Processes
P20 can be oil-quenched and then tempered to achieve specific hardness levels for various applications.
Hardness of P20 steel after quenching and tempering1
Tempering Temperature | Rockwell C Hardness |
As quenched | 51 |
400°F / 205°C | 49 |
600°F / 315°C | 47 |
800°F / 425°C | 44 |
1000°F / 540°C | 39 |
1100°F / 595°C | 33 |
1200°F / 650°C | 26 |
1250°F / 675°C | 21 |
- Preheat Temperature: 1200°F / 650°C (If used on larger mass parts.)
- Hardening Temperature: 1525°F / 830°C
- Quenching Method: Oil Quench and Carburize
- CHEMISTRY: Carbon 0.30%, Manganese 0.75%, Silicon 0.50%, Chromium 1.65% , Molybdenum 0.40%
2.3 Carburized and Hardened Condition
P20 steel can be carburized and then P20 steel hardened to increase surface hardness and wear resistance. After carburizing and hardening, the surface hardness of P20 steel can reach 65 HRC. The core hardness after carburizing is typically about 45 HRC.
The carburizing temperature impacts the resulting surface hardness. For example, specimens carburized at 845 °C (1550 °F) achieved a surface hardness of 65.6 HRC, while those carburized at 980 °C (1800 °F) resulted in 58.6 HRC.
Tempering a carburized P20 steel will cause a decrease in its surface hardness, and its resistance to softening during tempering is considered relatively low, similar to plain carbon steel.
2.4 Nitriding and Tufftriding
Nitriding and Tufftriding (a type of ferritic nitrocarburizing) significantly increase the surface hardness of P20 steel, primarily through the formation of hard nitrides and a diffusion zone.
Nitriding at 525°C in ammonia gas can result in a surface hardness of approximately 650HV.
Tufftriding at 570°C can give a surface hardness of approximately 700HV with a surface hard layer of approximately 0.1mm after two hours of treatment.
Nitriding also increases corrosion resistance.
3. Mechanical Properties (Interrelated with Hardness)
- Tensile Strength (Ultimate). P20 steel, after oil quenching from 845 °C (1550 °F) and tempering for 2 hours at 205 °C (400 °F), has a tensile strength of 1310 MPa (190 ksi).
- Yield Strength. Under the same heat treatment conditions as above, it has a yield strength of 1172 MPa (170 ksi).
- Elongation at Break. After oil quenching and tempering, the elongation in 50 mm (2 in.) is 13%.
- Impact Toughness (Charpy V-Notch). Under the same heat treatment conditions as above, it has a Charpy V-notch impact energy of 43 J (32 ft·lbf).
- Compressive Strength. Approximately equal to the tensile yield strength.
- Elastic Modulus. 190-210 GPa, or 30 x 10^6 psi (207 GPa).
- Density. 7855.1 kg/m^3 (7.855 g/cm^3).
- Thermal Conductivity. 24 Btu/ft/hr/°F (41.5 W/m/°K), or 34.0 W/(m.K). Important for dissipating heat during machining and in molding.
- Poisson’s Ratio. 0.27-0.30
- Thermal Expansion Coefficient. 12.8 x 10^-6/°C (20-425°C).
4. P20 Steel Machinability and Surface Finish (Relationship to Hardness)
P20 steel has excellent machinability at about 60-65% of 1% carbon steel or 65% compared to a 1% carbon tool steel benchmark (rating of 100). Pre-hardened P20 can be machined directly without further heat treatment, but the heat generated during machining may cause work hardening and dimensional inaccuracy. Solutions include:
- Use low cutting speeds and high feed rates to reduce heat.
- Employ tools coated with materials like titanium nitride (TiN).
- Apply coolants effectively to dissipate heat and lubricate.
- Bryson, W. E. (2007). Heat Treatment, Selection, and Application of Tool Steels (p. 195). Hanser Publications. ↩︎
Looking for High-Performance P20 Tool Steel?
Partner with Aobo Steel, your trusted experts with over 20 years of experience in forging superior tool steels. We provide top-quality P20 solutions, precisely tailored to meet your manufacturing needs and enhance your operational efficiency.
Whether you need standard P20 or a custom specification, our specialists are ready to assist you with material selection and provide a competitive, no-obligation quote.
Ready to Get Started? Fill out the form below to connect with us!