Are P20 and 4140 steel grades similar? The answer is no. While both are alloy steels, they differ significantly in composition, properties, and applications. P20 is primarily used for mold making in the plastics industry, whereas 4140 is a versatile steel employed in various structural and mechanical applications. This article explores the characteristics of each steel grade and outlines their key differences to help you choose the right material for your needs.
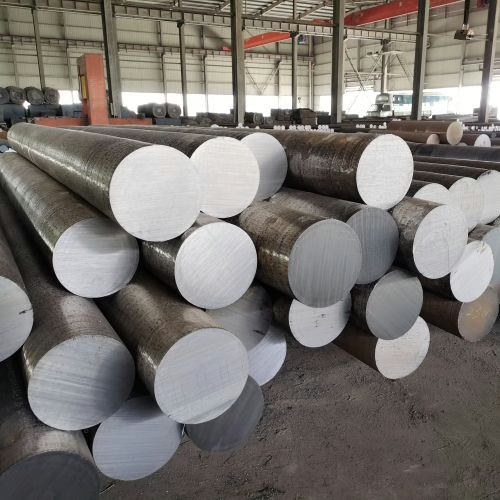
P20 Steel: A Mold Maker’s Choice
P20 is a low-alloy steel tailored for mold making, particularly in the plastics industry, and for die casting low-melting alloys. Its standout features include:
- Excellent Machinability: P20 is renowned for being easy to machine, making it ideal for crafting detailed mold designs.
- Adequate Hardenability: It offers sufficient hardenability for most mold cavities, though very large molds may require alternative grades.
- Low-Temperature Oil Quenching: Hardening through oil quenching at a lower temperature reduces dimensional changes compared to water-quenched steels.
- Carburizing Option: P20 can be carburized to boost wear resistance and surface hardness when needed.
- Industry Suitability: It excels in molding plastics and casting low-melting alloys.
Modified versions, such as DIN 1.2738, 1.2311, and 1.2312, are widely used in the plastics manufacturing industry. These grades strike a balance between hardness, hardenability, machinability, and polishability, making them cost-effective choices, especially for larger molds. Their fully bainitic microstructure after oil quenching and tempering ensures consistent hardness across sections.
4140 Steel: A Versatile Alloy
4140 is a medium-carbon chromium-molybdenum alloy steel valued for its adaptability and strength. It’s commonly used in components such as bars, forgings, and tubing across multiple industries. Its key attributes are:
- Defined Composition: Standardized under specifications like ASTM A322, SAE J404, and JIS G4053 (SCM 440), it typically includes 0.38-0.43% carbon, 0.75-1.00% manganese, 0.80-1.10% chromium, and 0.15-0.25% molybdenum.
- Customizable Properties: Heat treatments, such as annealing, quenching, and tempering, allow hardness to range from 150-200 HRC (annealed) to 375-425 HRC (tempered), adjusting strength and ductility as needed.
- Strength and Toughness: These qualities make 4140 ideal for shafts, gears, and structural parts.
- Heat Treatment Versatility: Processes like induction hardening enhance surface properties, perfect for high-duty applications.
Variants such as 4140 mod with tellurium or 4142H offer additional advantages, like improved machinability or higher yield strength (up to 1140 MPa in tempered states).
Key Differences Between P20 and 4140
Though both are alloy steels, P20 and 4140 serve distinct purposes due to differences in composition, application, and processing:
- Composition: P20 has a lower alloy content, while 4140’s higher chromium and molybdenum levels enhance its strength and toughness.
- Applications: P20 is specialized for mold making in plastics, whereas 4140 supports a wide range of mechanical and structural uses, from automotive parts to machinery.
- Heat Treatment: P20 uses low-temperature oil quenching to limit distortion, while 4140 supports varied treatments for tailored properties.
- Machinability: P20’s superior machinability is a cornerstone for mold production; 4140 is machinable but prioritizes strength over ease of machining.
- Hardenability: P20 suits most molds, but 4140 excels in through-hardening larger sections.
These distinctions highlight that P20 and 4140 are not interchangeable—each is optimized for specific roles.
Conclusion
In summary, P20 and 4140 steel grades are not similar. P20 is a mold-making specialist, offering excellent machinability and heat treatment benefits for the plastics industry. Conversely, 4140 is a robust and versatile alloy well-suited to diverse mechanical applications due to its strength and flexibility. Recognizing these differences ensures you select the steel best matched to your project’s demands.