When selecting an air-hardening tool steel, the choice between A2 and A4 is often a consideration. The key takeaway is this: Neither A2 nor A4 is inherently superior; they offer different balances of wear resistance, toughness, and dimensional stability. The optimal choice depends entirely on the specific demands of your tooling application. Making the proper selection requires understanding the distinct characteristics of each grade.
At Aobo Steel, with over two decades of specialization in tool steel forging, we understand these nuances. Let’s clarify the differences to help you make an informed choice.
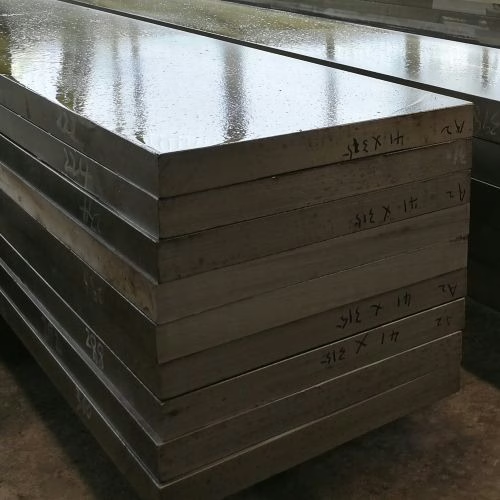
A2 Tool Steel – The Versatile Workhorse
A2 steel is a popular and versatile air-hardening tool steel. Its typical composition includes approximately 1.00% Carbon, 5.00% Chromium, 1.00% Molybdenum, and 0.20% Vanadium.
Key Properties of A2
- Wear Resistance: A2 steel offers excellent abrasion resistance, significantly superior to simpler carbon or oil-hardening steels, such as O1 tool steel. However, it provides less wear resistance than high-carbon, high-chromium steels, such as D2 tool steel or some high-speed steels (e.g., M4). It’s suitable for applications needing solid, but not extreme, wear performance.
- Toughness: A2 steel generally exhibits good toughness, superior to many oil-hardening and D-series steels. While tough, if edge chipping occurs in demanding applications like punching, a steel with higher toughness, such as S1 tool steel or S7 tool steel, may be necessary.
- Dimensional Stability and Hardenability: A significant benefit of A2 steel is its minimal distortion during air quenching. It provides excellent safety in hardening and achieves deep hardening, with a hardness of 60 HRC in the center of 125 mm sections. Expect minimal size change (approximately 0.001 in/in expansion) after heat treatment.
- Machinability: A2 steel is considered relatively easy to machine compared to other tool steels.
- Working Hardness: Typically used at 56-64 HRC, depending on the specific die application.
Common Applications for A2
Due to its balanced properties, A2 steel is widely used for:
- Bending and blanking dies
- Mold inserts
- Punches
- Aluminum extrusion dies
- Thread-rolling dies
- General-purpose tooling requires a good balance of wear and toughness, as well as stability.
A4 Tool Steel – Prioritizing Toughness and Stability
A4 steel is also an air-hardening tool steel, but it belongs to a group (often including A6 and A10) characterized by lower chromium content (~1%) and higher manganese content (~2%) compared to A2 steel. This compositional difference shifts its property balance.
Key Properties of A4
- Wear Resistance: Due to lower carbon and chromium content relative to A2, A4 offers lower wear resistance.
- Toughness: The lower carbide content generally results in higher toughness compared to A2. For applications where toughness is paramount, A4 holds an advantage.
- Dimensional Stability and Hardenability: A4 (like other low-Cr, high-Mn A-series steels) can be hardened from lower temperatures than A2. This contributes to superior resistance against distortion during heat treatment, a critical factor for complex or precise tooling.
- Machinability: A4 is generally expected to be easier to machine than A2, partly due to its composition.
Suitable Applications for A4
A4 is a strong candidate when:
- Maximum toughness is required.
- Minimal distortion during heat treatment is critical.
- Wear resistance requirements are moderate, less demanding than typical A2 steel applications.
- It can be an excellent choice for intermediate-service cold work tools and dies, where stability is key.
Conclusion: Making the Informed Choice
Selecting between A2 and A4 is a matter of prioritizing properties based on your specific operational needs:
- Choose A2 for a reliable, all-around performer where a good balance of wear resistance, toughness, and excellent dimensional stability is needed. It remains a go-to for many general cold-work applications.
- Choose A4 when the application demands higher toughness or the absolute minimum distortion during heat treatment, even if it means accepting lower wear resistance compared to A2. Its lower hardening temperature can also be an advantage.
Understanding the specific failure modes of your current tooling or the precise requirements of a new application is crucial. At Aobo Steel, we leverage our extensive experience to help clients select the most effective tool steel grade. If you require additional assistance, please don’t hesitate to contact us.
Looking for A2 Tool Steel? Get a Free Expert Consultation + Quick Quote Within 12 Hours!
- 🔹 20+ Years Forging Experience
- 🔹 Direct Factory Price, No Middleman
- 🔹 Over 40 Reliable Supplier Partners, Always in Stock
- 🔹 Custom Sizes & Heat Treatment Available
- 🔹 100% Material Certificate & Quality Guarantee
👇 Contact Us Now and Get a Special Discount for Your First Order!👇