For factories using H13 in demanding hot work applications, understanding its chemical H13 steel composition is key to optimizing processes and tool life. This guide offers direct, practical information on the elements defining H13 tool steel. We Aobo Steel provide a free download of the H13 steel composition PDF file at the bottom of the page.
What Defines H13 Steel?
H13 is a globally recognized 5% Chromium hot-work die steel, prized for its property balance at high temperatures. The specific H13 steel composition dictates its unique characteristics. While minor variations exist, the core chemical profile of H13 is consistent, ensuring reliable performance.
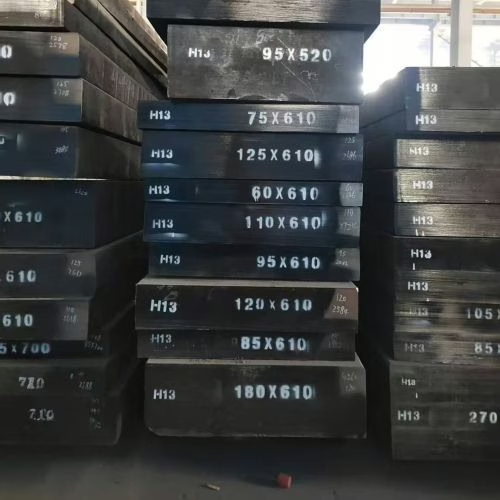
Key Alloying Elements in H13 Steel Composition
The precise control of alloying elements gives H13 steel its sought-after properties. Here’s a breakdown of the typical chemical H13 steel composition:
Element | Typical Range (% by weight) | Key Contributions |
Carbon (C) | 0.32 – 0.45 | Hardness, strength after heat treatment |
Silicon (Si) | 0.80 – 1.20 | Deoxidizer, tempering resistance |
Manganese (Mn) | 0.20 – 0.60 | Hardenability, deoxidizer |
Chromium (Cr) | 4.75 – 5.50 | Hardenability, heat checking resistance, toughness |
Molybdenum (Mo) | 1.10 – 1.75 | Hot strength, secondary hardening, tempering resistance |
Vanadium (V) | 0.80 – 1.20 | Wear resistance, tempering resistance, fine grain size |
Phosphorus (P) | Max 0.030 | Impurity, kept low for quality |
Sulfur (S) | Max 0.030 | Impurity, kept low (ESR grades can be <0.005%) |
Note: Elements like Nickel (Ni) and Copper (Cu) are kept at low levels (e.g., Ni+Cu combined often ≤0.75%).
The Role of Each Element in H13 Steel
Each element in the H13 steel composition is vital for its overall performance:
Carbon (C): Hardness Foundation
Carbon is crucial for H13’s hardness and strength after heat treatment. The typical content (around 0.38%-0.40%) balances hardness and toughness.
Silicon (Si): Material Integrity
Silicon acts as a deoxidizer and improves tempering resistance, helping maintain hardness at high service temperatures.
Manganese (Mn): Aiding Hardenability
Manganese enhances H13’s hardenability, ensuring consistent hardness, even in larger sections, and acts as a deoxidizer.
Chromium (Cr): “5% Chrome” Backbone
Chromium (approx. 5%) significantly boosts hardenability and is key for H13’s resistance to heat checking, also contributing to toughness and high-temperature strength.
Molybdenum (Mo): Hot Work Performance
Molybdenum is essential for H13’s hot work capabilities, enhancing hot strength, secondary hardening, and resistance to softening at high temperatures.
Vanadium (V): Wear Resistance & Stability
H13’s notable wear resistance comes from Vanadium, which forms hard carbides. These carbides resist abrasion, promote a fine grain structure, and improve tempering resistance. The higher Vanadium content (0.80-1.20%) is a key advantage over grades like H11 Mod.
H13 Steel Composition and Performance
The interaction of elements in the H13 steel composition (especially C, Cr, Mo, V) creates specific carbides during heat treatment. These carbides are critical for:
- Good Red Hardness: Retaining hardness at high temperatures.
- Excellent Abrasion Resistance: Due to hard vanadium carbides.
- Good Resistance to Heat Checking: For tools with cyclic heating/cooling.
- High Thermal Fatigue Resistance: Withstanding temperature-induced stress.These properties make H13 ideal for die casting molds, hot forging dies, and extrusion tooling.
Enhanced Quality with ESR H13 Steel
For applications needing superior cleanliness and homogeneity, Electro-Slag Remelted (ESR) H13 is often preferred. The ESR process refines the H13 steel composition by reducing impurities, leading to:
- Improved toughness and ductility
- Better fatigue resistance
- Higher polishability
- Potentially longer tool life
Partner with Aobo Steel for Your H13 Needs
Understanding H13 steel composition helps select the best material. At Aobo Steel, our experience ensures high-quality H13 tool steel that meets rigorous standards. For questions or to source H13 steel, contact our expert team.
Unlock Premium H13 Tool Steel Solutions
With over 20 years of forging expertise, Aobo Steel is your trusted partner for high-performance H13 tool steel. Our dedicated specialists provide tailored solutions and expert advice to meet your precise industrial needs.
- Exceptional Quality & Durability
- Expert Technical Support
- Competitive Pricing
- Reliable Supply Chain
Ready to enhance your operations?
Fill out the form below to discuss your H13 tool steel requirements, request a quote, or get personalized advice from our experts.