Your Trusted H13 Tool Steel Supplier
Leading Supplier of H13 Hot Work Tool Steel: Benefit from our extensive experience and commitment to excellence in H13 supply.
Aobo Steel supply H13 tool steel for your project
What is H13 tool steel? It is an air-hardening hot work tool steel and is one of the most widely used steels among all hot work tool steels. Compared to H11 tool steel, this steel offers higher thermal strength and hardness. Additionally, since it can be air-hardened, it exhibits low quenching deformation and residual stress and a minimal tendency for surface oxidation. Furthermore, it can produce secondary hardening, boasts excellent thermal stability, and effectively resists the erosion of aluminum alloy molten liquid.
Manufacturers widely use this steel to produce hot extrusion dies and mandrels, forging dies for drop hammers, and forging press dies. Additionally, it is commonly utilized for inserts in precision forging machines and die-casting molds for aluminum, copper, and their alloys. This versatility makes it a preferred choice for demanding industrial applications.
The designation in the U.S. ASTM A681 system is H13, and the name in the American AISI system is AISI H13 steel. Similarly, other national standards use comparable designations, such as ISO 40CrMoV5, Japan/JIS SKD61, USA/UNS T20813, Germany/DIN X40CrMoV5-1, Germany/W-Nr. 1.2344, and Czech Republic (CSN) 19554. For consistency, we will use H13 steel as a substitute in the following article. Next, we will discuss the properties of H13 tool steel in detail.
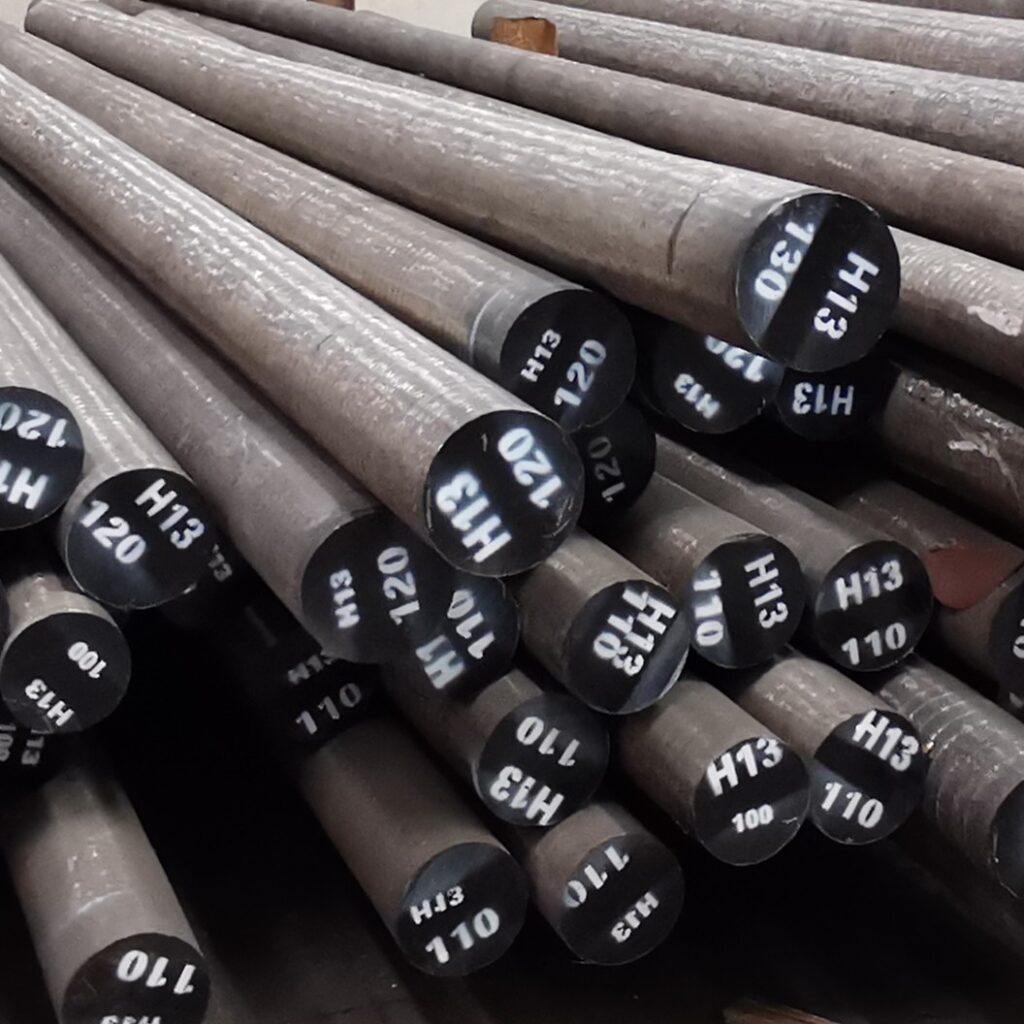
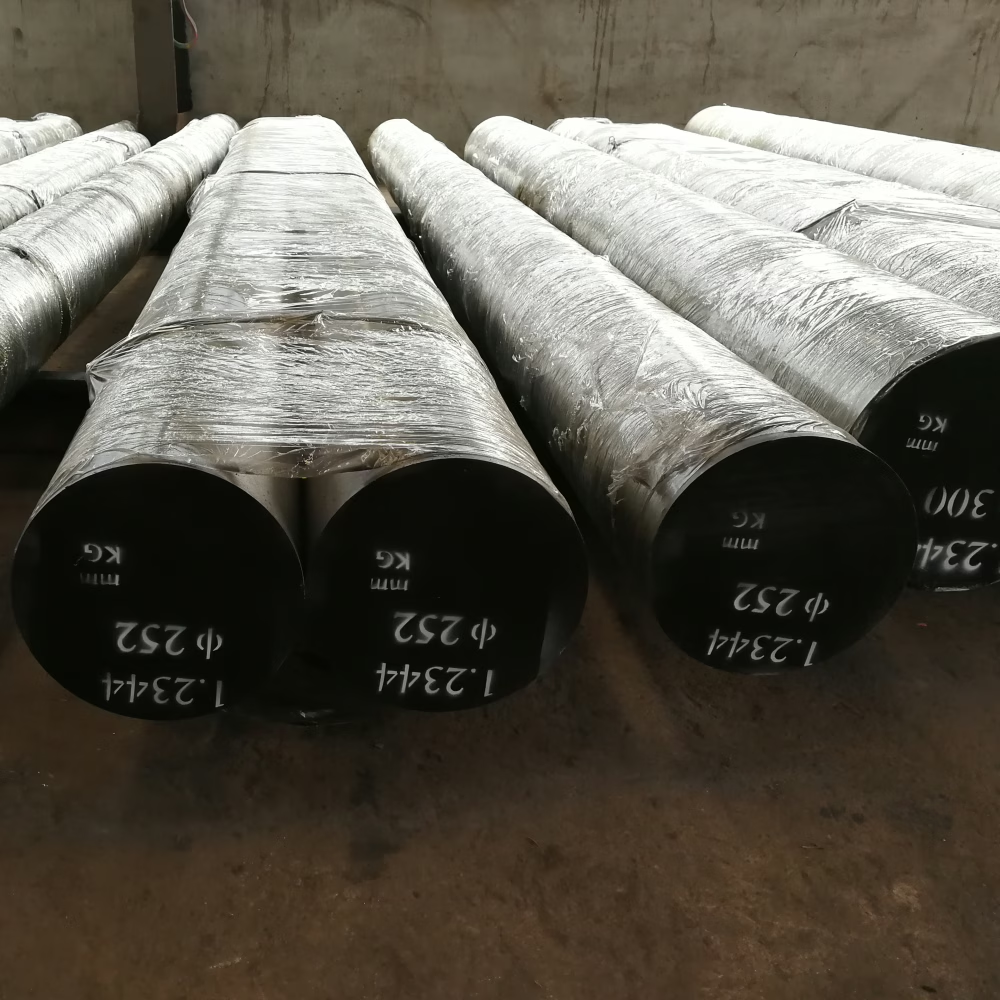
H13 tool steel Applications
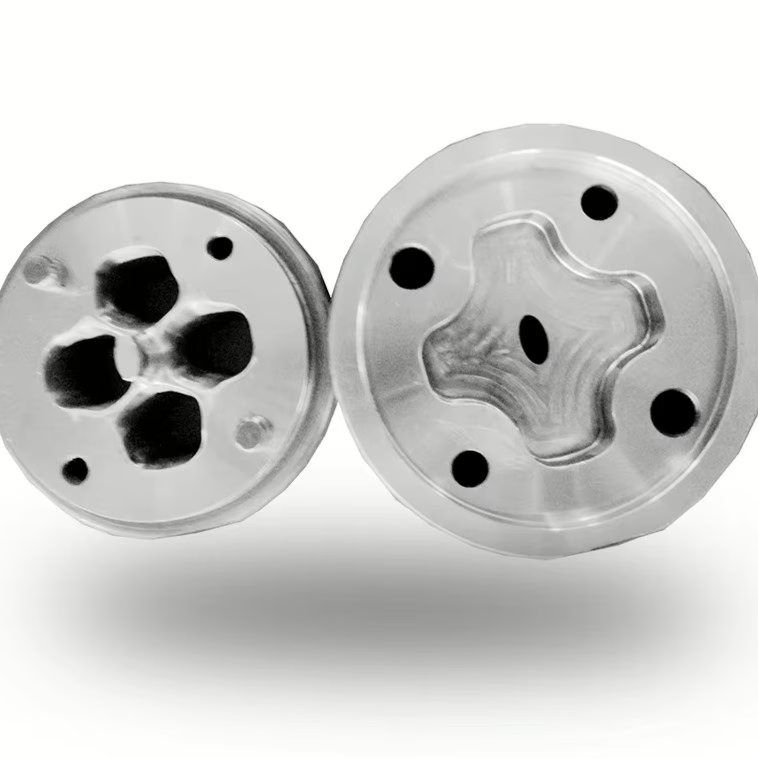
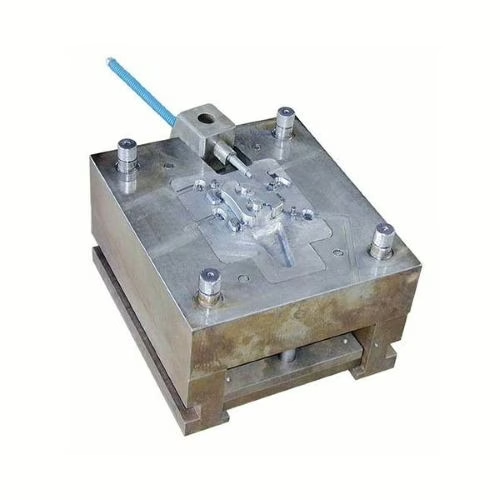
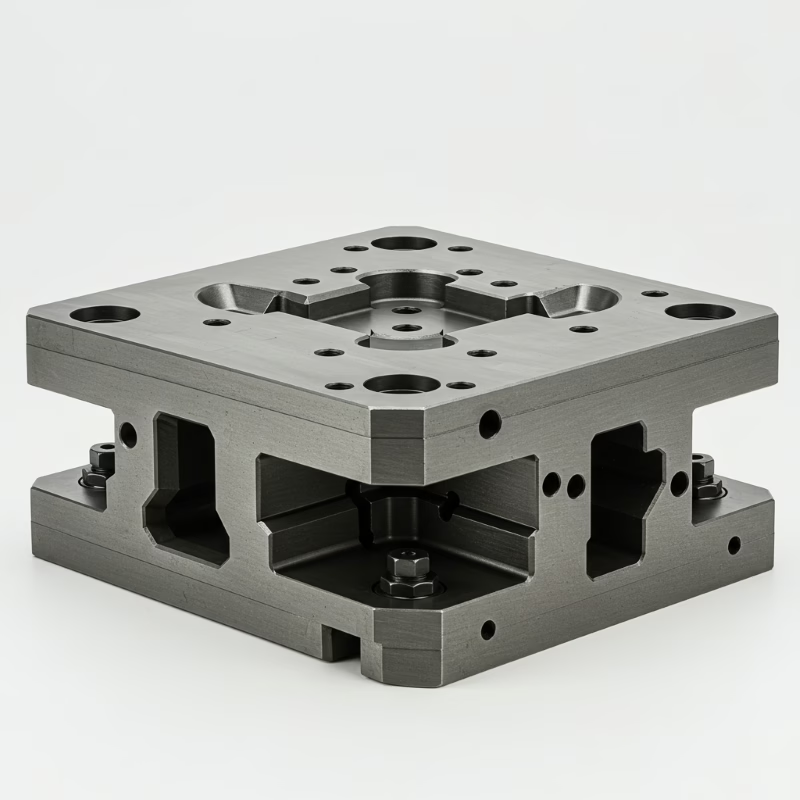
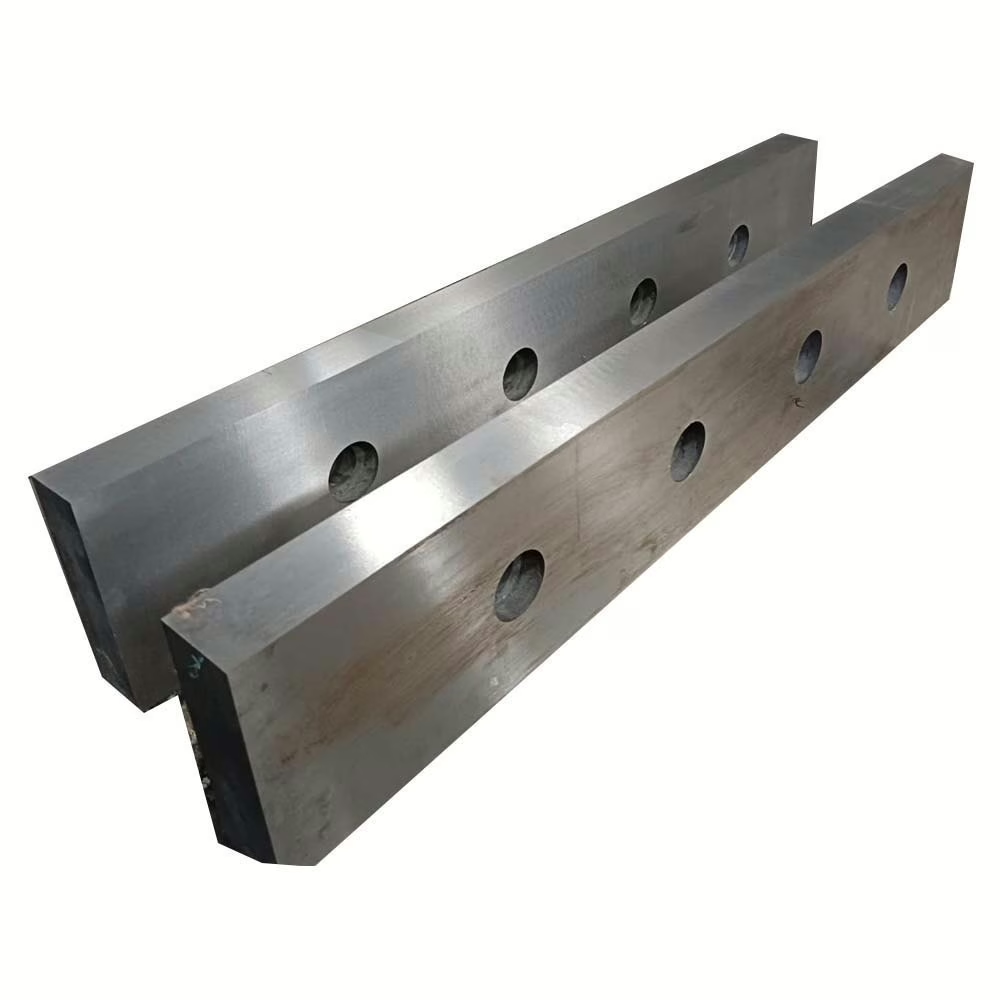
1. Die Casting Dies:
H13 die steel exhibits excellent heat resistance and toughness, making it ideal for die-casting dies. Specifically, workers inject molten metal under high pressure and temperature during the die-casting process, requiring materials capable of withstanding extreme conditions.
2. Forging Dies:
H13 handles high impact and mechanical stress effectively, making it suitable for forging dies that shape metals at high temperatures. Additionally, its durability and resistance to thermal fatigue ensure reliable performance in demanding industrial applications.
3. Extrusion Dies:
H13 is strong and resists wear. This makes it useful for extrusion dies. These dies shape materials are under high pressure.
4. Plastic Molding Dies:
Manufacturers commonly use H13 tool steel to make molds for plastic injection because they need its heat resistance and wear resistance.
5. Hot Shear Blades:
Its ability to stay sharp at high temperatures makes it a great material for hot shear blades used in metal cutting processes.
6. Aluminum alloy building material mold materials:
Chinese industries widely use H13 as a mold material for aluminum alloy building materials, which is why people call it H13 mold steel.
H13 Steel: High-Temperature Excellence
H13 steel delivers superior strength, thermal fatigue resistance, and hardness above 500°C—ideal for die-casting molds, hot-working dies, and high-temperature fixtures. Trusted in aluminum and magnesium alloy die-casting, forging, and extrusion, it’s your go-to choice for peak performance.
H13 tool steel properties
H13 mold steel is a widely used hot work tool steel globally. It is renowned for its strength and toughness, high hardenability, and resistance to thermal cracking. This steel features higher levels of carbon and vanadium, which result in good wear resistance but relatively lower toughness. It offers good heat resistance, maintaining strength and hardness, high wear resistance, and toughness at elevated temperatures. Furthermore, it has excellent overall mechanical properties and high tempering resistance.
H13 tool steel composition
Carbon (C) | Chromium (Cr) | Molybdenum (Mo) | Vanadium (V) | Silicon (Si) | Iron (Fe) | Nickel (Ni) | Copper (Cu) | Manganese (Mn) |
0.32 – 0.45 | 4.75 – 5.50 | 1.10 – 1.75 | 0.80 – 1.20 | 0.80 – 1.20 | ≥ 90.9 | ≤ 0.3 | ≤ 0.25 | Smaller amounts |
H13 material physical properties
Property | Value |
---|---|
Density | 7.75 – 7.80 g/cm3 |
Tensile Strength, Ultimate | 1200 – 2050 MPa (174000 – 231000 psi) |
Tensile Strength, Yield | 1000 – 1380 MPa (145000 – 200000 psi) |
Hardness | 45-52 HRC (Rockwell C Hardness) |
Impact Toughness | 20-40 J/cm2 |
Compressive Strength | 2550 MPa |
H13 tool steel heat treatment
- Preheating: 550 to 600°C, holding for a certain period of time.
- Second preheat: 800 ~ 850 ℃, holding time.
- austenitizing: 1020 ~ 1050 ℃, holding time 2 ~ 5 minutes.
- Hardening: Oil cooled to 150-180°C.
- First tempering: 560-600°C, hold for 2-3 hrs.
- Cool to room temperature.
- Second tempering: about 20°C lower than the first, hold for 2 to 3 hours.
- Final air cooling to room temperature.
H13 material hardness in HRC
- After hardening, H13 steel usually has a hardness between 56 and 64 HRC.
- After conventional tempering (tempering twice at 560 to 580°C), the hardness is usually in the range of 47 to 49 HRC.
- The final hardness of H13 steel can be adjusted within a certain range by adjusting the quenching and tempering temperatures and using different heat treatment processes (e.g., multiple tempering, deep-cooling, surface treatment, etc.) to meet different usage requirements.
H13 tool steel machinability
H13 tool steel cutting performance is medium level, cutting difficulty than mild steel and low alloy steel, but better than the high hardness of the cold work die steel and high-speed steel.H13 steel cutting performance is affected by a variety of factors, such as its hardness, heat treatment state, and microstructure. Annealing before the final heat treatment can improve its cutting performance. It is recommended to use carbide tools, lower cutting speeds and higher feeds, and adequate cooling lubrication.
Weldability of H13 steel
Welding H13 tool steel is a challenging task. H13 steel is considered a moderately weldable material, and its high carbon content makes it susceptible to hardening organization during the welding process, which increases the risk of cracking. Alloying elements such as chromium, molybdenum and vanadium, while increasing the hot strength and wear resistance of the steel, may also affect its weldability, for example by increasing the hardenability, which makes the weld and the heat-affected zone more susceptible to the formation of hard and brittle tissues, such as martensite, during the cooling process.
From forging to extrusion, H13 steel delivers unmatched strength and versatility. Discover the difference today!
H13 steel equivalents: DIN 1.2344 and JIS SKD61
Under the German and Japanese standard systems, DIN 1.2344 and SKD61 are steels that can substitute H13. They share similar compositions and properties, and are internationally recognized air-hardening hot work die steels. These steels exhibit excellent high-temperature strength, toughness, and resistance to thermal fatigue, enabling them to withstand rapid temperature changes. They are suitable for prolonged operation under high-temperature conditions while maintaining superior machinability and polishing performance.
Introduction to DIN 1.2344 steel
Chemical composition
Carbon (C) | Silicon (Si) | Manganese (Mn) | Chromium (Cr) | Molybdenum (Mo) | Vanadium (V) | Phosphorus (P) | Sulfur (S) |
0.35 – 0.42 | 0.8 – 1.2 | 0.25 – 0.5 | 4.8 – 5.5 | 1.2 – 1.5 | 0.85 – 1.15 | ≤0.030 | ≤0.030 |
1.2344 material properties
Machinability: Machine 1.2344 tool steel, which has moderate machinability, best in its annealed condition. Use proper cutting fluids and tools to reduce tool wear.
Weldability: Welding 1.2344 steel presents some challenges. To prevent cracking, welders must carefully preheat the material and perform post-weld heat treatment. Maintaining weld integrity requires specialized welding techniques.
Introduction to JIS SKD61 steel
Chemical composition
Carbon (C) | Chromium (Cr) | Molybdenum (Mo) | Vanadium (V) | Manganese (Mn) | Silicon (Si) | Phosphorus (P) | Sulfur (S) |
0.32 – 0.42 | 4.50 – 5.50 | 1.00 – 1.50 | 0.80 – 1.20 | 0.20 – 0.50 | 0.80 – 1.20 | ≤ 0.03 | ≤ 0.03 |
Physical Properties
Property | Value |
---|---|
Density | 7.8 g/cm³ |
Thermal Conductivity | 28 W/m·K at 100°C |
Elastic Modulus | 210 GPa |
Specific Heat Capacity | 460 J/kg·K |
Hardness (After Heat Treatment) | 50 – 55 HRC |