فولاذ الأدوات H13 مقابل فولاذ الأدوات A2: ما الفرق بين فولاذ A2 وH13؟ يُستخدم كلا النوعين H13 وA2 على نطاق واسع، لكنهما ينتميان إلى تصنيفات مختلفة ويختلفان في التركيب والخصائص، خاصةً من حيث مقاومة درجات الحرارة. يرتدي المقاومة والصلابة.
فولاذ الأدوات H13 هي شعبية جدا فولاذ أداة العمل الساخنصُممت هذه المادة للاستخدامات التي تتعرض فيها الأدوات لدرجات حرارة وأحمال عالية بشكل متكرر، مثل قوالب الصب، والدرفلة الساخنة، والبثق الساخن، والتشكيل الساخن. كما يمكن استخدامها أحيانًا في تطبيقات العمل البارد. ومن أبرز ميزاتها المتانة في درجات الحرارة العالية، ومقاومة التلدين، والمتانة.
فولاذ الأدوات A2 هو فولاذ متوسط السبائك، مُصلد بالهواء، مُستخدم على البارد. يُستخدم بشكل أساسي في تطبيقات العمل البارد في درجة حرارة الغرفة، ولكنه يُستخدم أيضًا في أدوات القص الساخن خفيفة الوزن وقوالب البثق الساخن للزنك. من أبرز ميزاته مقاومة التآكل، وثبات الأبعاد، والمتانة العالية.
وفي النص التالي، سنقوم بمقارنة النوعين من الفولاذ في جوانب مختلفة.
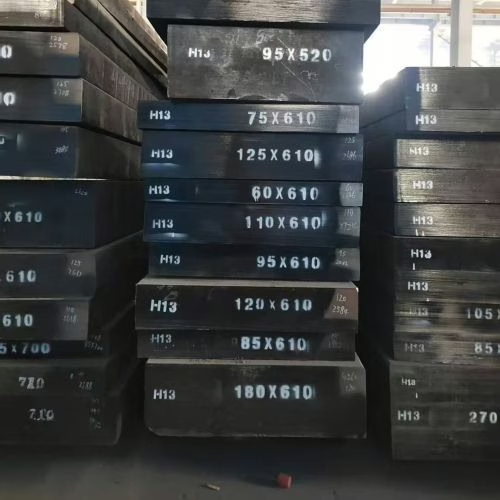
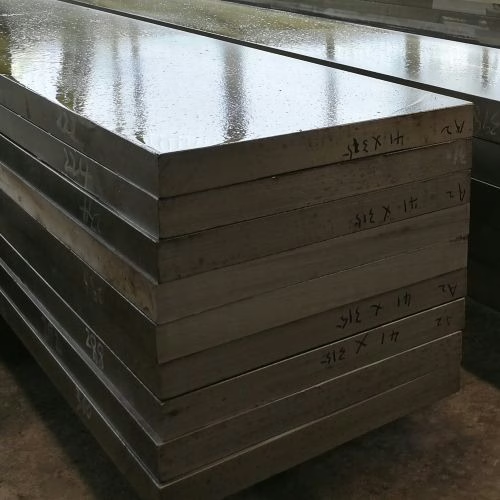
تعبير
رمز | فولاذ الأدوات H131 (%) | فولاذ الأدوات A2 (%) |
ج | 0.32 – 0.45 | 0.95 – 1.05 |
كر | 4.75 – 5.50 | 4.75 – 5.50 |
شهر | 1.10 – 1.75 | 0.90 – 1.40 |
الخامس | 0.80 – 1.20 | 0.15 – 0.50 |
سي | 0.80 – 1.20 | 0.50 (الحد الأقصى) |
من | 0.20 – 0.50 | 1.00 (الحد الأقصى) |
ص | 0.03 (الحد الأقصى) | 0.03 (الحد الأقصى) |
س | 0.03 (الحد الأقصى) | 0.03 (الحد الأقصى) |
مقارنة الخصائص
- مقاومة التآكل. يحتوي H13 على الفاناديوم، ما يجعله يتمتع بمقاومة جيدة للتآكل. يتميز A2 بمقاومة عالية للتآكل، بفضل المارتنسيت عالي الكربون ومشتتات الكربيد الدقيقة.
- الصلابةيتميز H13 بمتانة ممتازة ومقاومة عالية للصدمات. يتميز A2 بمتانة عالية.
- صلابة ساخنة (صلابة حمراء) / مقاومة للتصلبH13 هو فولاذ مُشَغَّل بالحرارة، مُصمَّم خصيصًا للبيئات ذات درجات الحرارة العالية، يجمع بين الصلابة الحمراء ومقاومة ممتازة للتآكل والصدمات. يقاوم هذا الفولاذ التليين أثناء التعرض المستمر لدرجات حرارة تصل إلى 540 درجة مئوية (1000 درجة فهرنهايت). كما يتميز بمقاومة ممتازة للتسخين، ويمكنه الحفاظ على صلابته ومتانته العالية في درجات الحرارة العالية. يتميز الفولاذ A2 بمقاومة جيدة للتسخين، إلا أن صلابته الحرارية عادةً ما تكون غير كافية لتلبية متطلبات التشغيل الآلي عالي السرعة أو تطبيقات التشغيل الحراري. وهو غير مناسب لظروف العمل التي يتعرض فيها لدرجات حرارة تزيد عن 205-260 درجة مئوية (400-500 درجة فهرنهايت) لفترات طويلة.
المعالجة الحرارية
H13 و A2 كلاهما من الفولاذ المتصلب بالهواء مع عمق قابلية التصلب. H13 هو فولاذ تقوية ثانوي يتطلب المعالجة الحرارية عند درجة حرارة أعلى (أعلى من 510 درجة مئوية أو 950 درجة فهرنهايت) لتحقيق الأداء الأمثل وتخفيف الضغط واستقرار الأداء. صلابة فولاذ الأداة A2 تبلغ درجة حرارته 61 HRC عن طريق التبريد عند 300 درجة فهرنهايت (150 درجة مئوية) لمدة ساعة واحدة. لمزيد من التفاصيل الرجاء القراءة المعالجة الحرارية لفولاذ الأدوات H13 و A2 الفولاذ الحراريطعام.
ثبات الأبعاد
كما ذكرنا أعلاه، يعتبر كل من H13 وA2 من الفولاذ المتصلب بالهواء، وميزتهما هي أنهما يحافظان على ثبات أبعادي ممتاز.
معالجات السطح
لتحسين خصائص السطح، يتم استخدام معالجات مثل النترتة يمكن تطبيقها على كلٍّ من H13 وA2. تُكوّن النترتة طبقة سطحية صلبة، مما يُحسّن بشكل كبير من مقاومة التآكل، وفي بعض الحالات، من مقاومة التعب. يستفيد H13، على وجه الخصوص، بشكل كبير من النترتة في تطبيقات مثل قوالب الصب، حيث يواجه درجات حرارة عالية وتآكلًا كاشطًا.
التطبيقات
- تطبيقات فولاذ الأدوات H13يُستخدم على نطاق واسع في تطبيقات العمل الساخن العامة، وقوالب الصب (للألومنيوم والزنك والمغنيسيوم)، وقوالب حقن البلاستيك، وأدوات التشكيل. وهو مناسب لقوالب البثق الساخن للألومنيوم والمغنيسيوم والفولاذ والنحاس والنحاس الأصفر. كما يُستخدم في المثاقب والثاقبات واللحامات للعمل الساخن. يمكن استخدامه كفولاذ قوالب للتجاويف المخرطة، ويُوصى به لقوالب البلاستيك المصقولة جيدًا بعد تكرير ESR، ويُستخدم أحيانًا للأجزاء الهيكلية شديدة الإجهاد في صناعة الطيران نظرًا لمقاومته للتليين في درجات الحرارة المرتفعة ومتانته المعتدلة.
- فولاذ الأدوات A2: فولاذ أدوات متعدد الأغراض، مُصلد بالهواء، ذو تطبيقات واسعة في مجال التشكيل. يُستخدم عادةً في تقطيع وثقب القوالب في الإنتاج الضخم. كما يُستخدم في قوالب التشكيل على البارد، وقوالب السك، وقوالب السحب والتصفيح، وقوالب درفلة الخيوط، وشفرات القص والشق، ولفائف التشكيل. يُعد خيارًا جيدًا لأدوات وقوالب العمل على البارد متوسطة الخدمة. يمكن استخدامه في القوالب الصغيرة والحشوات، ويُفضل استخدامه في القوالب الكبيرة نظرًا لانخفاض تشوهه أثناء التشكيل. المعالجة الحرارية. يستخدم أحيانًا كبديل لفولاذ العمل الساخن لأدوات القص الساخن والقوالب المستخدمة في عملية البثق الساخن للزنك.
ملخص المقارنة
مميزة | فولاذ الأدوات H13 | فولاذ الأدوات A2 |
التطبيق الأساسي | تطبيقات العمل الساخن (على سبيل المثال، الصب بالقالب، والتزوير، والبثق). | تطبيقات العمل البارد (على سبيل المثال، القطع، التشكيل، الرسم). |
مقاومة التآكل | مقاومة عالية للتآكل. أفضل من سلسلة S، لكنها أقل عمومًا من سلسلة D. مناسبة لعمليات الإنتاج الطويلة على أخشاب رقيقة/متوسطة السُمك. | مقاومة عالية للتآكل. أفضل من سلسلة S، لكنها أقل عمومًا من سلسلة D. مناسبة لعمليات الإنتاج الطويلة على أخشاب رقيقة/متوسطة السُمك. |
الصلابة | قوة تأثير ممتازة ومتانة جيدة؛ مقاومة عالية للصدمات تجعلها مفضلة لمعظم عمليات العمل الساخن. | الحد الأدنى من الضغوط المتبقية والحد الأدنى/عدم وجود تشويه عند التصلب بالهواء. |
صلابة ساخنة | عالية جدًا؛ تحافظ على صلابة عالية (على سبيل المثال، ~52 HRC عند 540 درجة مئوية) وقوة في درجات حرارة مرتفعة؛ مقاومة ممتازة للتلطيف (التصلب الثانوي). | مقاومة جيدة للتغيرات في درجات الحرارة وتظهر تصلبًا ثانويًا، ولكنها غير كافية للتشغيل الآلي عالي السرعة أو ظروف العمل الساخن (تقتصر على أقل من 205-260 درجة مئوية). |
قابلية التصلب | التصلب العميق، التصلب الهوائي. | التصلب العميق، التصلب الهوائي. |
ثبات الأبعاد | الحد الأدنى من الضغوط المتبقية والحد الأدنى/عدم وجود تشويه عند التصلب بالهواء. | أقل حركة وتشويه في التصلب، وأمان عالي ضد التشقق. |
قابلية التصنيع | جيد في حالة التصلب. تصنيف التلدين: 70% مقارنةً بالفولاذ الكربوني 1% (W1).2 | سهولة التصنيع. تصنيف التلدين: 60-65% مقارنةً بالفولاذ الكربوني 1% (W1). |
الصلابة النموذجية | صلابة العمل العادية للصب بالقالب: ٤٤-٨ HRC؛ لمقاومة الصدمات: ٤٠-٤ HRC. قابلة للمعالجة الحرارية حتى أكثر من ٢٠٧٠ ميجا باسكال (٣٠٠ كيلو باسكال). صلابة مُخمّدة (غير قابلة للكسر) ~٥٣ HRC. | صلابة العمل العادية: ٥٨-٦٠ HRC. صلابة الصب المُخمَّدة: ~٦٤ HRC. |
في الأساس، تم تصميم H13 للعمل في بيئات ذات درجات حرارة عالية شديدة، مع إعطاء الأولوية للصلابة الساخنة ومقاومة الصدمات القوية، في حين أن A2 متعدد الاستخدامات الفولاذ المُشغول على الباردتتميز بمقاومة عالية للتآكل وثبات أبعادها للعمليات في درجة حرارة الغرفة. إذا واجهت صعوبة في الاختيار بين هاتين المادتين، يُرجى التواصل معنا للحصول على استشارة متخصصة.
احصل على عرض أسعار تنافسي لأدوات الفولاذ H13 وA2
بخبرة تزيد عن 20 عامًا في مجال التشكيل، تُعدّ Aobo Steel شريكك الموثوق في فولاذ الأدوات عالي الأداء H13 وA2. لا نوفر المواد فحسب، بل نوفر أيضًا الحلول. استفد من معرفتنا العميقة بالصناعة وسلسلة التوريد الموثوقة لنجاح مشروعك.
✉ تواصل معنا عن طريق ملء النموذج أدناه.