Heat treatment is not merely an optional step for A2 steel; it is necessary to develop the specific combination of high hardness, wear resistance, and toughness required to effectively use as a tool and die material. Without proper heat treatment, A2 steel would lack the strength and durability to perform reliably in demanding manufacturing environments, leading to premature failure and increased production costs. Therefore, adhering to a well-defined and controlled heat treatment cycle is paramount to maximizing the service life and performance of components made from A2 tool steel.
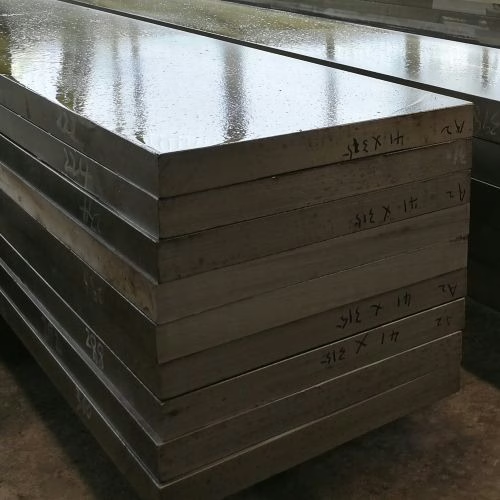
A2 Mechanical Properties and Performance
The mechanical properties of A2 steel depend heavily on its heat-treated condition.
Annealed Condition: Machinability
Before hardening, in the annealed state, A2 offers good machinability. Its rating is around 60% compared to a 1% carbon tool steel (rated at 100%). This facilitates easier initial shaping and fabrication of tools. Annealed tool steels generally have lower hardness and strength than their hardened state.
Hardened and Tempered Condition: The Optimal Balance
The real performance of A2 is achieved after proper hardening and tempering. This process develops a strong combination of:
- Wear Resistance: A2 provides very good resistance to wear, superior to that of shock-resisting steels (like the S series).
- Toughness: It maintains good toughness (resistance to fracture), better than high-chromium, high-wear steels like D2. This combination makes it durable in applications facing both abrasive wear and moderate impact.
- Hardness: A typical working hardness of 58-60 HRC is achievable after hardening (e.g., from 1775°F / 968°C) and air quenching. A2 can fully harden through sections up to about 4.5 inches (114 mm).
- Dimensional Stability: Due to its air-hardening nature, A2 exhibits good dimensional stability during heat treatment. Size change is relatively small and predictable (around +0.001 in./in. or +0.10%), simplifying the process of achieving final tool dimensions.
- Safety in Hardening: A2 is known for its reliability and safety during the hardening process, minimizing risks compared to more demanding quench methods.
Torsional Properties Considerations
- Strength & Ductility: When hardened, A2’s torsional strength generally exceeds that of O1 tool steel, peaking after a low-temperature temper (around 300°F / 150°C). Importantly, unlike O1, its torsional ductility doesn’t drop significantly at these low tempering temperatures.
- Impact Energy: Note that torsional impact energy may be minimal when tempered around 500°F (260°C). This temperature range might be avoided if the application involves significant torsional impact loading. However, unnotched impact energy is generally good when A2 is tempered for high hardness.
A2 Tool Steel Heat Treatment Guide
Achieving the optimal performance and longevity from A2 tool steel depends entirely on precise and correctly executed heat treatment. As a specialist in tool steel with over 20 years of forging experience, Aobo Steel provides this guide to outline the essential steps for processing A2 steel effectively. Adhering to these procedures is critical for obtaining the desired hardness, toughness, and dimensional stability.
Preheating
Preheating is the essential first step before hardening A2 steel.
Purpose:
- Minimize thermal shock when introducing the steel to higher austenitizing temperatures. This is especially important for components with significant variations in thickness.
- Condition the steel’s microstructure for the upcoming phase transformations.
- Relieve residual stresses induced during manufacturing or machining.
Procedure:
- Heat the A2 steel uniformly to approximately 1200°F (650°C).
- Ensure the entire part reaches this temperature before proceeding to the austenitizing step.
Austenitizing (Hardening)
This stage transforms the steel’s structure to austenite, dissolving carbon and key alloying elements into the solution, which is necessary for hardening.
Procedure:
- Heat the steel from the preheating temperature to the hardening temperature range of 1750°F to 1800°F (955°C to 980°C). A common target is 1775°F (970°C).
- Soaking Time: Hold the steel at the selected austenitizing temperature for 1 hour per inch (25 mm) of its thickest cross-section. Adequate soaking is crucial for complete transformation.
- Atmosphere Control: To prevent surface decarburization (loss of carbon, leading to reduced surface hardness), perform austenitizing in a controlled environment. Options include:
- Neutral atmosphere furnace
- Vacuum furnace
- Neutral salt bath
- Wrapping the part securely in stainless steel foil is also a common and effective method for protection.
Quenching
A2 is an air-hardening tool steel. This means it achieves hardness by cooling in air after austenitizing.
Procedure:
- Remove the steel from the furnace and allow it to cool in still air to room temperature.
- The cooling transforms the austenite into martensite, the hard microstructure responsible for A2’s wear resistance.
- Ensure the cooling rate is sufficient to avoid the formation of softer phases, especially in the core of larger sections.
- Expected Outcome: As-quenched hardness typically reaches ~64 HRC. However, the steel in this state is very brittle and contains internal stresses.
- Dimensional Change: Expect expansion of approximately 0.001 in./in. (0.001 mm/mm) during quenching. Be aware that complex geometries may lead to some distortion.
Tempering
Tempering is a mandatory step immediately following quenching. It reduces brittleness and internal stresses, significantly increasing the steel’s toughness.
Procedure:
- Double Tempering: A double tempering treatment is strongly recommended for A2 steel. This ensures maximum stress relief, microstructural stability, and the transformation of any retained austenite (untransformed austenite left after quenching), which is critical for dimensional stability in service.
- Temperature: Select the tempering temperature based on the desired final balance of hardness and toughness, typically between 375°F and 1000°F (190°C to 540°C). Lower temperatures yield higher hardness but lower toughness; higher temperatures increase toughness but reduce hardness. Common practice involves a first temper around 400°F (205°C) and a second around 375°F (190°C), but adjust based on requirements.
- Duration: Hold the steel at the chosen tempering temperature for a minimum of 2 hours per inch (25 mm) of the thinnest section for each tempering cycle. Allow the part to cool completely to room temperature between tempers.
Stress Relieving
Stress relieving can be applied at different stages to minimize distortion and cracking risk.
Stress Relieving Unhardened Material
- If needed before hardening (e.g., after heavy machining), heat slowly to 1200°F–1250°F (649°C–677°C).
- Soak for 2 hours per inch of thickness.
- Cool slowly, preferably in the furnace, to room temperature.
Stress Relieving Hardened Material
- This is strongly recommended after operations on hardened parts, such as heavy grinding, welding, or Electrical Discharge Machining (EDM).
- Temper the part at a temperature approximately 25°F to 50°F (14°C to 28°C) below the final tempering temperature used previously.
Important Considerations
- Hardening Safety: A2 steel offers good safety in hardening and generally exhibits less distortion than oil-hardening steels.
- Atmosphere: Maintaining the correct furnace atmosphere during austenitizing is crucial to preventing detrimental oxidation and decarburization.
- Retained Austenite: Improper quenching or insufficient tempering (especially omitting the second temper) can leave retained austenite, leading to potential dimensional instability later. Double tempering effectively addresses this.
Effect of heat treatment on A2 steel
Why Heat Treatment Matters for A2 Steel
Heat treatment is a fundamental process for A2 tool steel. It involves carefully controlled cycles of heating and cooling. Why do we do this? To change the steel’s internal microstructure. This controlled change is how we achieve the specific mechanical properties – like hardness and toughness – required for demanding applications. Understanding this process is key to getting the best performance from A2 steel.
Achieving Hardness
The primary way to increase the hardness of A2 steel is through quenching.
- The Process: This means heating the steel to a specific austenitizing temperature and then cooling it rapidly. For A2, being an air-hardening steel, this cooling is typically done in air.
- The Result: Rapid cooling transforms the steel’s structure into martensite, which is very hard. The carbon content in the A2 steel directly influences the maximum hardness achievable.
- The Challenge: While hard, steel directly after quenching (as-quenched) is often too brittle for most tool applications. It needs further processing.
Developing Toughness
Hardness is important, but tools also need toughness – the ability to resist chipping or breaking. This is achieved through tempering.
- The Process: After quenching, the steel is reheated to a precise temperature below its critical point, held for a specific time, and then cooled.
- The Result: Tempering modifies the brittle martensite structure, reducing brittleness and significantly increasing toughness.
- The Balance: There’s a direct trade-off controlled by the tempering temperature.
- Lower tempering temperatures result in higher hardness but lower toughness.
- Higher tempering temperatures increase toughness but decrease hardness.
- Choosing the right temperature is critical to meeting the specific demands of the tool’s application. With our experience, we at Aobo Steel understand how crucial this balance is.
Ensuring Dimensional Stability
Heat treatment involves significant temperature changes, which can cause the steel to change shape or size. Controlling dimensional stability is vital.
- The Challenges:
- Uneven Heating/Cooling: Can cause warping, distortion, or even cracking, especially in parts with complex shapes or thick sections.
- Quenching Stresses: The rapid cooling and internal structure changes during quenching create internal stresses that can lead to dimensional changes.
- The Solutions:
- Uniform Heating: Proper preheating steps can help ensure the part heats evenly.Controlled Cooling: A2’s air-hardening nature helps reduce thermal shock compared to oil—or water-quenching
- internal stresses introduced during quenching, improving stability.
- Advanced Techniques: Methods like vacuum heat treatment can offer superior dimensional control by eliminating surface reactions like oxidation and decarburization.
Summary: Tailoring A2 Steel Properties
In short, the heat treatment for A2 tool steel typically involves:
- Austenitizing: Heating to the correct temperature to transform the structure.
- Quenching: Air cooling to achieve high hardness by forming martensite.
- Tempering: Reheating to balance hardness and toughness and relieve stress.
Expert A2 Tool Steel Solutions
With 20+ years of forging experience, Aobo Steel delivers A2 Tool Steel with excellent wear resistance and toughness for demanding applications.
Need stamping dies, forming tools, or custom parts? We provide tailored steel solutions.
Ready to upgrade?
Fill out the form below. Our A2 specialists will provide a quick quote and expert advice.