420 stainless steel vs 304: In terms of name, 420 stainless steel and 304 stainless steel are both stainless steel, but they have significant differences. We distinguish between the two based on metallurgical classification, mechanical properties, corrosion resistance, heat treatment, machinability, and applications.
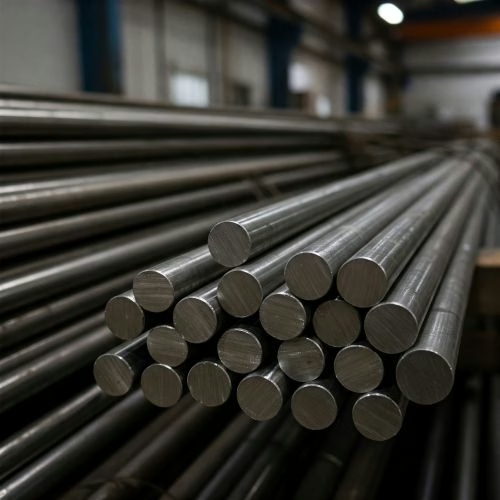
420 stainless steel vs 304: Metallurgical Classification and Composition
420 stainless steel is a martensitic stainless steel, mainly composed of iron, chromium, and carbon, and is ferromagnetic at room temperature. 420 stainless steel typically contains a minimum of 0.15% carbon, with a typical carbon content of 0.3-0.4% during production. The chromium content typically ranges from 12.00% to 14.00%.
304 stainless steel is an austenitic stainless steel that is non-magnetic in the annealed condition. It typically contains 18-19% chromium and 8-11% nickel.
420 stainless steel vs 304: Mechanical Properties
- Hardness. 420 stainless steel has quenching hardenability, enabling high strength and hardness. Its common hardness is 46–52 HRC, and it can reach 54 HRC through heat treatment. In the annealed state, the strength and hardness of 304 stainless steel are lower than those of heat-treated 420 stainless steel.
- Ductility and Toughness. 420 stainless steel has low ductility and room temperature impact strength, especially in the hardened condition. 304 stainless steel exhibits excellent ductility and toughness, with elongations ranging from 40% to 60%.
- Wear Resistance. 420 stainless steel has a higher carbon content, so it’s harder and more wear-resistant. While 304 also has some wear resistance, it’s not as good as 420 stainless steel.
Corrosion Resistance
- Martensitic stainless steel, including 420 stainless steel, has the lowest corrosion resistance among stainless steels because it has low chromium and nickel content as well as high carbon content. This composition structure may lead to carbide precipitation. The corrosion resistance of 420 depends significantly on its heat-treated condition; for maximum resistance, it should be tempered either below 750°F (400°C) or above 1100°F (600°C). It is resistant to air, fresh water, some chemicals, and food acids, but not suitable for severe corrosive environments. 304 stainless steel has good corrosion resistance in industrial atmospheres and weakly acidic media. It does not usually rust in chloride-free environments.
- 420 stainless steel’s high carbon levels can increase the possibility of forming Cr-rich carbides (K1 carbide, (Cr, Fe)23C6), which can deplete chromium in the surrounding matrix below the 12% Cr threshold, making the steel susceptible to intergranular corrosion (sensitization). 304 stainless steel is prone to intergranular corrosion due to carbide precipitation, especially in welded conditions (weld corrosion). While 304 has good general corrosion resistance, for pitting resistance, molybdenum-containing grades like 316 are preferred. The Pitting Resistance Equivalent Number (PREN) for 304 is 191.
Weldability and Fabrication
- 420 stainless steel has a high carbon content, which makes it difficult to weld. If welding is required, preheating is necessary, and heat treatment must be performed again after welding. In contrast, 304 stainless steel has good weldability.
- In terms of machinability, 420 has good machinability, while 304 has low machinability. When properly annealed, 420 has a machinability rating of 70 compared to a 1% carbon steel (rated at 100). 304 steel has high toughness and good ductility, and produces long, thin chips during processing.
Heat Treatment
420 stainless steel heat treatment can significantly improve its mechanical properties. It must undergo double tempering, and sometimes even triple tempering. 304 stainless steel is typically used in annealed form to maximize its ductility and corrosion resistance. Unlike 420 martensitic steel, it cannot be hardened through heat treatment.
Applications comparison
- 420 Stainless Steel: Commonly used for cutlery, dental and surgical instruments, plastic molds, shafts, valves, magnets, and other products requiring a combination of hardness, wear resistance, and corrosion resistance.
- 304 Stainless Steel: Known as the “workhorse” alloy, it is the most widely used stainless steel. Its applications are diverse, including food and beverage industries (dairy, breweries), chemical and process industries, building and architectural applications (cladding, railway parts), home appliances (sinks, stoves, refrigerators, utensils), and some automotive exhaust systems.
Summary
420 stainless steel is a hard, strong, and wear-resistant material, ideal for applications that require high hardness and edge retention. However, it is less ductile, more difficult to weld, and has lower general corrosion resistance compared to 304 stainless steel. Its properties are highly dependent on precise heat treatment. In contrast, 304 stainless steel offers excellent ductility, formability, and good general corrosion resistance, making it versatile for a vast array of applications, particularly those requiring extensive fabrication and resistance to mild corrosive environments. Its weldability is good, especially with the “L” variant, though it sacrifices some hardness for these benefits.
The above is a summary of our 20 years of industry experience with 420 stainless steel, with some information sourced from scientific papers. If you are interested in 420 stainless steel, please do not hesitate to contact us.
- McGuire, M. (2008). Stainless Steels for Design Engineers (p. 214). ASM International. ↩︎
Get a Competitive Quote for Premium 420 Stainless Steel
Leverage our 20+ years of forging expertise. We provide consistent, high-quality 420 stainless steel tailored to your exact specifications. Partner with an industry expert for reliable supply and service.
Ready to start? Fill out the form below to get a no-obligation quote from our specialists.