With over two decades of supplying top-quality tool and alloy steels, we frequently receive questions about selecting the best grade for a specific application. Today, let’s compare two standard models: SKD11 versus SKD61. While both are reliable Japanese Industrial Standards (JIS) tool steels, they are designed for fundamentally different worlds within the factory. Understanding their unique characteristics is key to optimizing your tooling performance and lifespan.
The core difference boils down to temperature: SKD11 is built for cold work, while SKD61 excels in hot work environments. This distinction comes directly from their chemical makeup and how they respond to heat treatment.
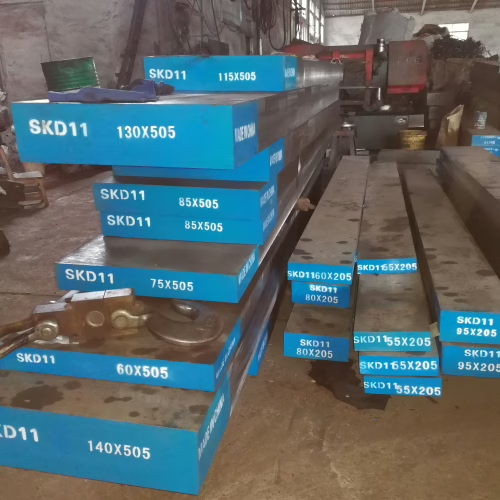
SKD11: The Cold Work Specialist
Think of SKD11 as your go-to for high-wear, room-temperature applications. It’s a high-carbon, high-chromium cold-worked tool steel.
- Composition Highlights: Its significant carbon (around 1.5%) and chromium (around 12%) content are crucial. During heat treatment, these elements form hard carbides throughout the steel’s structure.
- Key Properties: This translates directly into SKD11’s main strengths:
- Excellent Wear Resistance: The hard carbides make it incredibly resistant to abrasion and wear, making it perfect for tools that repeatedly come into contact with other materials.
- High Hardness: It can achieve high hardness levels, often exceeding 60 HRC after proper heat treatment.
- Good Compressive Strength: It holds up well under pressure.
- Dimensional Stability: It maintains its shape well after quenching, which is vital for precision tooling.
- Applications: You’ll find SKD11 used extensively for:
- Stamping dies (especially for precision work)
- Forming dies
- Cold forging and extrusion dies
- Punches
- Shear blades
- Gauges
- Complex plastic molds require high wear resistance.
Essentially, if your tool requires cutting, shaping, or forming metal or other materials at ambient temperatures and needs to withstand prolonged wear, SKD11 is a prime candidate.
SKD61: The Hot Work Performer
Now, let’s shift gears to SKD61. This grade is engineered to withstand the demanding conditions of hot work applications.
- Composition Highlights: Compared to SKD11, SKD61 has a significantly lower carbon content (approximately 0.40%), but includes additions such as silicon (approximately 1.0%) and molybdenum (approximately 1.25%), along with a moderate chromium level (approximately 5%). This blend is optimized for high-temperature performance.
- Key Properties: SKD61 brings a different set of strengths to the table:
- Excellent Hot Strength & Hardness: It retains its hardness and strength even when exposed to elevated temperatures.
- Good Toughness: Crucial for resisting cracking under the stresses of hot forming.
- Thermal Shock and Fatigue Resistance: It withstands the repeated heating and cooling cycles typical of hot work without failing quickly.
- Good Thermal Conductivity: Helps dissipate heat effectively.
- Applications: SKD61 is the workhorse for:
- Die casting molds (especially for aluminum and zinc alloys)
- Hot forging dies
- Hot extrusion dies (mandrels, liners)
- Hot shear blades
- Press forging tools.
If your tooling operates at high temperatures, dealing with molten metal or red-hot billets, SKD61’s ability to resist heat, thermal stress, and maintain its integrity is what you need.
The Bottom Line
Choosing between SKD11 and SKD61 is straightforward once you define the operating environment:
- Need maximum wear resistance and hardness for cold forming, stamping, or cutting? Choose SKD11.
- Need toughness, thermal fatigue resistance, and strength at high temperatures for die casting, forging, or extrusion? Choose SKD61.
Using the wrong steel type can lead to premature tool failure, costly downtime, and compromised part quality. By understanding the fundamental differences rooted in their composition and intended applications, you can make an informed decision.
Of course, specific application details and heat treatment protocols matter greatly. At Aobo Steel, with our extensive experience, we’re always ready to discuss your particular requirements and help you select the ideal material for your needs. Feel free to reach out!