Selecting the correct steel grade is critical for the performance and longevity of your tooling. At Aobo Steel, with our extensive experience in tool steel forging, we often guide customers through the differences between popular grades. Two common choices, particularly for mold and die applications, are P20 and H13. While both are workhorses, they have distinct properties suited for different jobs. Let’s look at the key technical differences.
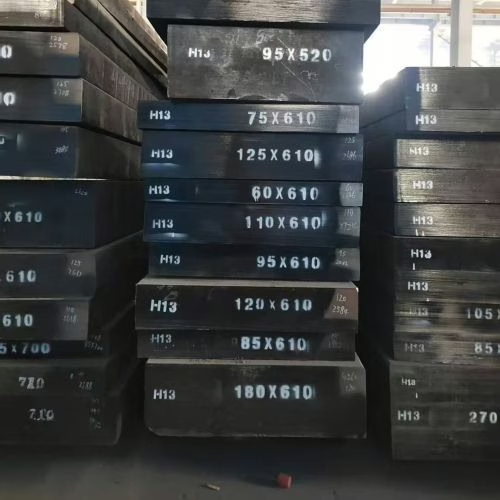
Classification and Basic Use
- P20: This is typically classified as a medium-carbon alloy tool steel, primarily known as a mold steel. Consider it a versatile grade for plastic molding and certain die-casting applications, particularly for zinc.
- H13: This grade falls under the category of 5% chromium hot-work tool steels. It’s also recognized for its ultrahigh strength capabilities.
Chemical Composition: The Foundation of Performance
The core differences between P20 and H13 stem from their alloy compositions:
- P20: Generally contains 0.18-0.40% carbon (often around 0.35%), along with silicon, manganese, chromium (0.5-2.00%), and molybdenum (0.30-0.55%).
- H13: While carbon levels can overlap (0.30-0.45%), H13 has a significantly different alloying package defined by standards like ASTM A681 or JIS SKD61. It features much higher chromium (4.75-5.50%), higher molybdenum (1.10-1.75%), and a crucial addition of vanadium (0.80-1.20%). This vanadium content contributes significantly to its performance characteristics.
Applications: Where They Excel
- P20: Widely used for plastic injection molds, zinc die-casting dies, and holder blocks. It’s a solid choice for intermediate-length production runs.
- H13: As a hot-work steel, H13 shines in high-temperature environments involving thermal cycling. This includes die casting molds (especially for aluminum or other high-melting-point alloys), hot extrusion dies, hot forging dies, and also demanding plastic injection molds that require higher hardness or better thermal management than P20.
Processing and Hardness
How these steels are supplied and heat-treated is a major practical difference:
- P20: A key advantage is that P20 is typically supplied pre-hardened, with a hardness of approximately 28-32 HRC (approximately 300 HB). This allows mold makers to machine cavities directly and use the tool without further high-temperature heat treatment, minimizing distortion risks. For higher surface hardness and wear resistance in plastic molds, P20 can be carburized after machining. It’s typically oil-quenched.
- H13: While sometimes used prehardened, H13 is often heat-treated by the user to achieve higher hardness levels (e.g., 45-54 HRC or even higher for specific applications) and strengths exceeding 2070 MPa (300 ksi). H13 is an air-hardening steel, which means it can harden through large sections with minimal distortion during the cooling process. It’s also a secondary-hardening steel, maintaining high hardness and strength at elevated operating temperatures, known as “red hardness.” Double tempering is often recommended.
Key Performance Characteristics
Let’s compare them head-to-head on critical properties:
- Wear Resistance: H13 generally offers superior wear and abrasion resistance due to its higher vanadium content, which forms hard carbides. P20 has fair wear resistance, making it suitable for many molds, but H13 is better suited for abrasive conditions or longer runs. Carburizing significantly improves the surface wear of P20.
- Toughness: Both steels are considered tough. H13 generally exhibits excellent impact strength and toughness, which are vital for resisting cracking in demanding applications. P20 also offers good toughness.
- Temper Resistance (Red Hardness): This is a major differentiator. H13 has excellent resistance to softening at high temperatures, making it ideal for use in hot work applications. P20’s resistance to tempering is lower.
- Dimensional Stability: H13’s air-hardening nature results in very minimal distortion during heat treatment. P20 (oil-hardening) offers better stability than water-hardening steels but generally less than H13.
- Machinability: P20 is known for its excellent machinability in the prehardened condition. H13 also has good machinability when properly annealed.
- Polishability: Both P20 and H13 can achieve a polished surface of good quality, which is essential for high-quality plastic molds. H13 often polishes well at higher hardness levels (above 50 HRC).
- Heat Checking Resistance: Crucial for die casting, H13 offers good resistance to thermal fatigue cracking, commonly known as heat checking. P20 is suitable for lower-temperature die casting, such as zinc, but H13 is preferred for more demanding hot work.
- Internal Quality: For large or critical tools, internal steel cleanliness is vital. H13 is often produced using Electroslag Remelting (ESR) or similar processes, yielding higher cleanliness and uniformity compared to conventionally melted steels. This enhances performance, especially resistance to thermal fatigue.
Making the Choice
- Choose P20 if: You need a cost-effective, readily machinable steel for plastic molds or low-temperature die casting, supplied prehardened for convenience, suitable for intermediate runs. Carburizing is an option for enhancing surface wear resistance.
- Choose H13 if: Your application involves high operating temperatures, requires superior wear resistance, high red hardness, maximum dimensional stability during heat treatment, resistance to heat checking, or high hardness levels (above 50 HRC) for demanding molds or hot work tooling. Its higher alloy content (Cr, Mo, V) provides superior performance in these conditions, often justifying the use of cleaner ESR/VAR grades for critical applications.
Understanding these differences helps ensure you select the optimal tool steel for your specific needs. If you have further questions or require specific grades, such as P20 or H13, please do not hesitate to contact us at sales@aobosteel.com. We have the experience to help you make the right choice.