HSS primarily stands for High-Speed Steel or High-Speed Tool Steel. It is a crucial category of alloy steels predominantly used for creating engineering cutting tools.
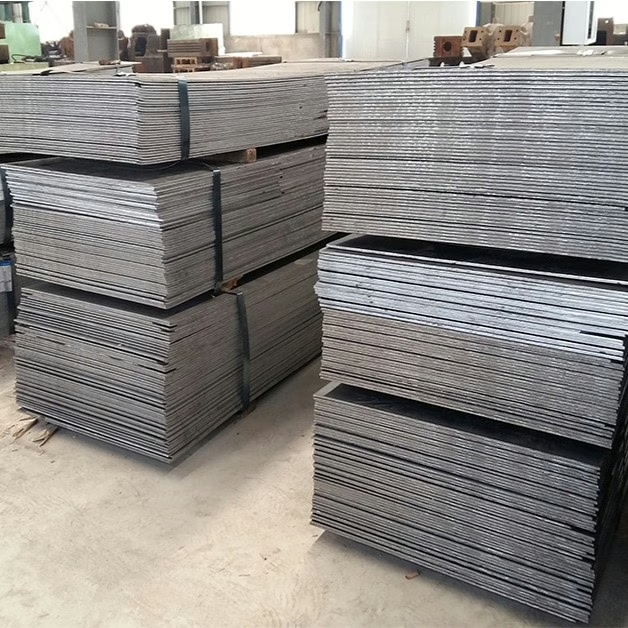
Definition and Primary Function
High-Speed Steels (HSS) are a class of alloy steels specifically designed for applications requiring materials that can maintain their hardness and cutting edge even at elevated temperatures generated during high-speed machining operations. They are extensively utilized to manufacture various engineering cutting tools.
Chemical Composition
The following table shows the composition of the high-speed steel we produce.
Steel Type | C | Si | Mn | Cr | V | W | Mo | Co |
M2 | 0.78-1.05% | 0.20-0.45% | 0.15-0.40% | 3.75-4.50% | 1.60-2.20% | 5.50-6.75% | 4.50-5.50% | – |
M35 | 0.80–0.90% | 0.20–0.45% | 0.20–0.45% | 3.75–4.50% | 1.75–2.20% | 5.50–6.75% | 4.50–5.50% | 4.50–5.50% |
M42 | 1.05 – 1.1% | 0.15 – 0.65% | 0.15 – 0.40% | 3.5 – 4.25% | 0.95 – 1.35% | 1.15 – 1.85% | 9.0 – 10.0% | 7.75 – 8.75% |
Key Characteristics and Properties
- High Hardness: HSS exhibits high hardness, which is important for resisting penetration and deformation during cutting.
- Red Hardness (Heat Resistance): Refers to its ability to resist softening or annealing at temperatures of 400°F (205°C) and above. However, these abilities decline rapidly at temperatures above 540°C to 600°C.
- Wear Resistance: HSS has good resistance to abrasive wear.
- Toughness and Shock Resistance: HSS demonstrates excellent fracture toughness and resistance to shock loading, allowing tools to withstand impact forces without brittle fracture.
- Machinability: HSS can be hot-rolled and forged into rough shapes, then machined before heat treatment and finish grinding.
- Cost-Effectiveness: HSS tools are relatively inexpensive compared to other tool materials, making them a common choice, especially for monolithic tools.
Classification and Grades
- T-type Steels: These grades primarily use tungsten as the major alloying element. They tend to be less tough than M-types but are easier to heat-treat.
- M-type Steels: These grades primarily use molybdenum. They are more commonly used for rotary tools, such as drills, end mills, and taps. M2 is a commonly used grade for drills and taps, while M42 exhibits the greatest hot strength.
- International and National Standards: HSS grades are specified in various standards, such as BS 4659:1989 in the UK, which includes details on hot-work, cold-work, and plastic molding tool steels. The ISO Standard 4957 and the German system (prefix ‘S’ for Schnellstahl) also classify HSS by chemical composition and application. ISO designations, like HS2-9-1-8, denote the percentages of tungsten, molybdenum, vanadium, and cobalt.
Applications
HSS is a versatile material used in a wide array of tools:
- Cutting Tools: Common applications include drills, reamers, taps, milling cutters, broaches, and gear hobs. It is also used for turning operations, especially in multi-spindle machines.
- Specialized Machining: HSS tools are employed for machining challenging materials like titanium and aluminum alloys.
- Industrial Tools: This includes saw blades (especially bi-metal steel strips for band saws), precision punching tools, and various punches and dies.
- Dies: Used for presses and hammers, hot trimming, hot swaging, and hot extrusion tools and mandrels.
Source High-Performance M2, M35 & M42 Steel With Confidence
Choosing the correct high-speed tool steel is critical for performance and cost-effectiveness. Don’t leave it to chance. Partner with an expert to get the exact material grade and quality your project demands.
Expert Material Consultation
Leverage my 15+ years of experience to select the optimal steel for your application, saving you time and preventing costly errors.
Guaranteed Quality & Certification
All materials are 100% UT tested and sourced from our network of 40+ trusted suppliers, backed by Aobo Steel’s 20 years in forging.
Evan, your Tool Steel Specialist
“My goal is your success. Let’s find the perfect steel together.”
Aobo Steel | www.aobosteel.com