When it comes to die casting, selecting the right tool steel is crucial for success. Many of our customers rely on H13 tool steel, and for good reason. Let’s break down why H13 tool steel is a workhorse in this demanding field.
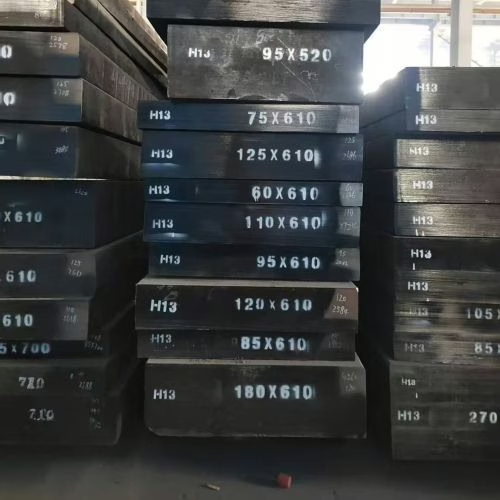
H13 is a 5% chromium hot-work die steel, widely used for casting metals like zinc, aluminum, and magnesium. It’s versatile enough for various components – dies, inserts, cores, plungers, slides, shot sleeves, and nozzles all benefit from its properties. Occasionally, it is also used for short runs with brass.
So, what makes H13 tool steel stand out? It boils down to a combination of properties ideally suited for the high temperatures and cyclical stress involved in die casting. Key strengths include:
- Excellent Heat and Wear Resistance: It withstands intense heat well, even when exposed to molten metal.
- Thermal Fatigue Resistance: This is critical. Die casting involves constant heating and cooling, which can lead to “heat checking” – a network of fine cracks that form on the surface of the casting. H13 tool steel is inherently resistant to this, helping extend tool life. These cracks often originate from residual tensile stresses on the steel surface, and H13 tool steel helps mitigate this failure.
- Good Toughness and Impact Strength: Die casting involves significant shock loads. H13 tool steel provides the necessary toughness to withstand these forces. Its vanadium content contributes to the formation of hard vanadium carbides, thereby enhancing wear resistance.
- Resistance to Tempering: H13 tool steel maintains its hardness and strength even at the elevated temperatures typical in hot work applications.
Heat Treatment Considerations
Proper heat treatment is non-negotiable for achieving optimal performance from H13 steel.
- Air Hardening: H13 steel is an air-hardening steel. This is a significant advantage, as it minimizes distortion during the hardening process and allows for deep hardening, even in large sections (up to approximately 150 mm or 6 inches).
- Hardening and Quenching: Typically, H13 is hardened (austenitized) at a temperature of 1010-1030°C (roughly 1850-1885°F) and then air quenched to achieve a hardness of approximately 52-54 HRC.
- Triple Tempering: This is vital. Tempering must be done immediately after quenching. For die casting, we strongly recommend a triple tempering process. This ensures any retained austenite transforms properly, preventing brittleness under fatigue stress. Tempering is typically performed above 510°C (950°F) to achieve optimal properties. Avoid tempering around 500°C (930°F), as this can sometimes lead to reduced impact toughness, known as temper embrittlement.
- Target Hardness: Achieving the final hardness accurately is crucial. Too hard, and the tool can be brittle; too soft, and it wears quickly. The target hardness depends on the specific component:
- General Die Casting Tooling: 44–48 HRC
- Shock Resistance Needs: 40–44 HRC
- Dies: 42–52 HRC
- Inserts/Cores: 46–52 HRC
- Plungers: 46–50 HRC
- Ejector Pins: 42–46 HRC
Material Quality and Processing
- Premium Quality (ESR/VAR): For demanding applications requiring maximum toughness and reliability, consider H13 steel produced using Electro-Slag Remelting (ESR) or Vacuum Arc Remelting (VAR). These processes result in cleaner steel with better homogeneity.
- Surface Treatments: Nitriding can significantly increase surface hardness (over 1000 HV or >70 HRC) for enhanced wear resistance, although the nitrided layer can sometimes be prone to cracking. Chromizing is another option, though H13’s carbon content can affect the layer thickness.
- Welding: For repairs, TIG welding is a suitable option. Proper preheating (ranging from 110°C to 375°C, depending on size and complexity) is essential to prevent cracking. An H13 filler wire is standard.
- Machinability: In its annealed state, H13 steel machines reasonably well.
In Summary
H13 tool steel is a foundational material for die casting due to its excellent balance of high-temperature strength, wear resistance, thermal fatigue resistance, and toughness. Its air-hardening nature provides good dimensional stability. However, realizing its full potential depends entirely on correct heat treatment, especially proper triple tempering to achieve the target hardness for your specific application. Selecting high-quality materials, such as ESR or VAR grades when necessary, further ensures optimal performance and longevity.
If you have specific questions about applying H13 steel in your operations or need assistance selecting the correct grade, please don’t hesitate to reach out. We have extensive experience with tool steels and are here to help you find the best solutions.