We are here to provide direct, comprehensive insights into M2 tool steel properties, a grade we know intimately. M2 is a molybdenum-type high-speed tool steel widely recognized and utilized across the industry for its exceptional balance of abrasion resistance, toughness, and crucial red hardness. We provide a free download of the M2 tool steel properties PDF at the bottom of the page.
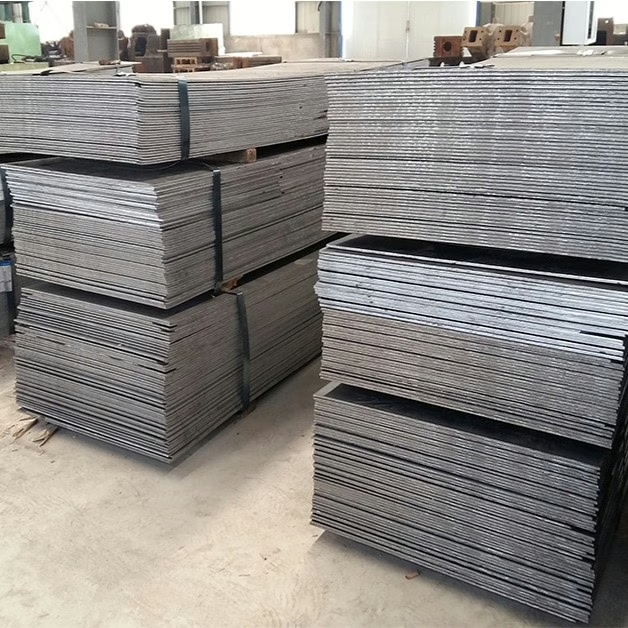
1. Performance Properties: The M2 Tool Steel Advantage
Understanding the performance attributes of M2 is key to appreciating its versatility and why it remains a preferred choice for many demanding applications. These M2 tool steel properties are what truly set it apart.
1.1 Superior Wear Resistance
M2 offers very high wear resistance, a characteristic significantly enhanced by the presence of undissolved carbides within its structure. It’s noted for very high abrasive wear resistance compared to many cold-worked steels.
1.2 Balanced Toughness
This grade provides good toughness, positioned as a medium among Molybdenum HSS types and high when compared to conventional cold-worked steels. The processing method plays a role here; M2 produced by powder metallurgy often exhibits higher impact toughness due to a more uniform carbide distribution. However, precise heat treatment is critical; hardening above approximately 1210℃ (2210°F) to 1220℃ (2230°F) can lead to a notable reduction in toughness.
1.3 Exceptional Hot Hardness (Red Hardness)
M2 is engineered to retain its hardness even at elevated temperatures. It possesses good red hardness and is rated as having very high hot hardness, also known as tempering resistance. This property is indispensable for tools operating under heat, as it directly dictates the steel’s ability to maintain its cutting edge and performance. Adding Cobalt to the M2 base alloy can further amplify this crucial high-temperature hardness.
2. Fabrication and Heat Treatment: Maximizing M2 Tool Steel Performance
Precise fabrication and heat treatment protocols are essential to leverage the inherent M2 tool steel properties fully.
2.1 Machinability Considerations
In its properly annealed state, M2 possesses a machinability rating of 65, using a 1% carbon steel as the baseline at 100. This rates it as medium machinability among tool steels.
2.2 Achieving Dimensional Stability
When M2 is air-quenched from the correct hardening temperature, you can anticipate an expansion of approximately 0.001 inches per inch (0.001 mm/mm). It is important to account for the part’s geometry and potential distortion, such as bending or twisting, which will influence the final dimensions post-heat treatment. Further dimensional changes also occur during tempering, primarily due to the transformation of retained austenite.
2.3 Heat Treatment for M2 Tool Steel
M2 is often considered to have the most forgiving hardening range among high-speed steels. However, its heat treatment process is inherently more complex than that of other tool steel types. A typical cycle involves preheating, austenitizing (hardening), quenching, and multiple tempering cycles.
- Preheating: Commonly to 650℃ (1200°F).
- Austenitizing (Hardening): Temperatures are quite high, around 1220℃ (2225°F), with a brief hold time.
- Quenching: Followed by rapid cooling.
- Multiple Tempering Cycles: Crucial for achieving the desired balance of hardness and toughness. M2 specifically requires a complex tempering cycle.
Here’s a look at common tempering temperatures and their typical resulting M2 tool steel hardness:
Tempering Temperature | Typical Hardness (HRC) |
565°C (1050°F) | ≈65 |
595°C (1100°F) | ≈61 |
620°C (1150°F) | ≈56 |
650°C (1200°F) | ≈52 |
Multiple tempering steps are frequently necessary to manage retained austenite effectively. To prevent decarburization during both annealing and hardening, we strongly recommend utilizing a controlled neutral atmosphere, vacuum, or a neutral-salt furnace environment. Additionally, cryogenic treatments can be integrated after a stress relief step, followed by tempering, to further enhance properties and prevent brittleness.
3. M2 Tool Steel Hardness Values at a Glance
For quick reference, here are the typical hardness values you can expect for M2 tool steel:
- Annealed Hardness: Generally less than 241 HB.
- Working Hardness (after full hardening and tempering): Typically in the range of 60−65 HRC.
4. Applications of M2 Tool Steel
The robust combination of M2 tool steel properties makes it incredibly versatile across a broad spectrum of industrial applications. It is truly a workhorse high-speed steel. M2 is widely specified for:
- Standard Cutting Tools: Including twist drills and turning tools, where precision and durability are paramount.
- Milling Cutters and Screw Taps: Especially when enhanced with cobalt additions, providing superior performance in tough machining operations.
- Hot Cutting Operations: Benefiting from its exceptional wear and heat resistance, it maintains integrity even at elevated temperatures.
- Certain Cold Work Tooling: Offering reliability in applications requiring high toughness and resistance to deformation.
- Specific Hot Work Conditions: Where its ability to withstand heat and maintain hardness is crucial.
- Blanking Steel: For thicknesses exceeding approximately 0.25 inches (6.4 mm), M2 is often preferred over carbide due to carbide’s limited shock resistance, providing a more robust solution.
- Machining High Tensile Strength Materials: Such as heat-treated steels, where their strength and wear resistance allow for efficient and precise material removal.
- Resistance to Abrasion: Performs exceptionally well against abrasive materials like hard cast iron, cast steel, brass, aluminum, and various plastics, ensuring prolonged tool life.
In summary, M2 tool steel offers a robust balance of properties, making it an ideal choice for various cutting and forming applications that demand high performance under challenging conditions. Understanding its specific heat treatment requirements and material characteristics is key to maximizing tool life and performance in your operations. At Aobo Steel, we are committed to providing you with the highest quality M2 tool steel and the knowledge to utilize it effectively.
Unlock Superior Performance with Aobo Steel M2 Tool Steel
With over 20 years of expertise in forging tool steel and a commitment to quality, Aobo Steel is your trusted partner for premium M2 Tool Steel. Don’t compromise on durability and precision.
Ready to enhance your operations? Please fill out the form below to contact our tool steel experts today!