What is D2 tool steel? D2 tool steel is a high-carbon, high-chromium, air-hardening steel with excellent wear resistance, high hardness, and good dimensional stability. It is the most widely used steel grade in cold-work tool steel. D2 tool steel knives are also very common in our daily lives. Just as a coin has two sides, the advantages of D2 tool steel knives in specific applications may be disadvantages in others. Based on the characteristics of D2 steel and our experience, we analyze the advantages and disadvantages of using D2 tool steel knives. Readers of this article can determine how to utilize D2 tool steel knives based on their specific application scenarios.
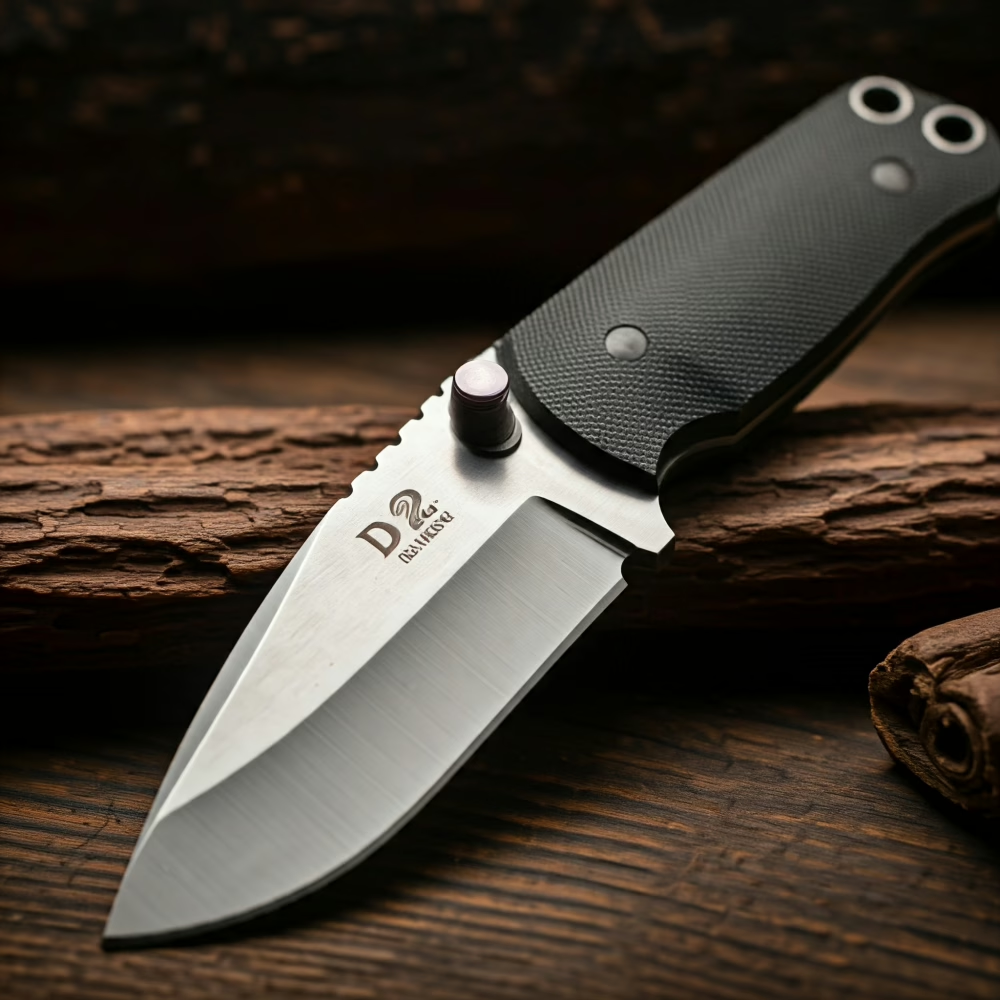
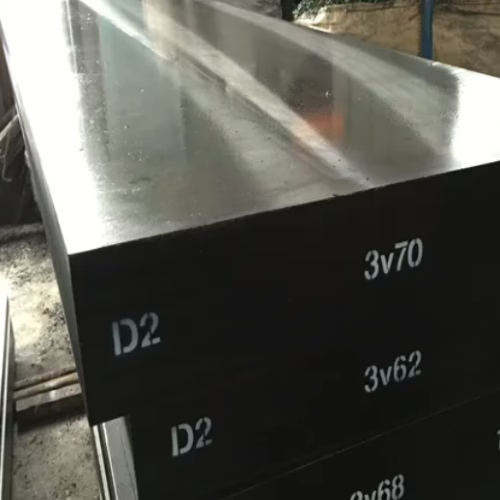
Advantages of D2 Tool Steel for Knives
- High Wear Resistance. D2 steel has extremely high wear resistance, and knives made from it can maintain a sharp cutting edge for an extended period, thereby exhibiting exceptional resistance to dulling caused by wear. The reason is the D2 steel composition, which has a high carbon and chromium content. These elements form a large volume fraction of extremely hard M7C3-type chromium carbides in its microstructure, with a hardness of up to 1800 HV (Vickers hardness).
- High Hardness. After heat treatment, the hardness of D2 steel can be achieved at 60 to 62 HRC (Rockwell C). Some sources claim that after quenching, it can even reach a hardness of 64 HRC. And surface hardness after ion nitriding can reach 750-1200 HV (approx. 61-64 HRC).1 The higher the hardness, the better the wear resistance. Learn more about this topic by reading D2 steel hardness.
- Resistance to Softening (Hot Hardness). Although D2 steel is used for cold working, friction inevitably generates heat when used for cutting purposes. Therefore, D2 has good softening resistance at high temperatures and maintains edge stability, which is an advantage of D2 tool steel knives.
Limitations of D2 Tool Steel for Knives
Now that we have discussed the advantages let’s talk about the limitations of D2 tool steel knives.
- Low Toughness/Brittleness. D2 steel has low toughness, which is its biggest drawback when used as a knife blade. D2 knife blades may be prone to chipping or breaking, especially when subjected to lateral stress, impact loading, or when encountering hard, discontinuous materials. It tends to fail by fracturing with a flat surface and shows almost no necking (plastic deformation) before fracture.2 If applications require resistance to impact, we recommend using other steel grades instead of attempting to enhance D2 steel’s toughness through heat treat D2 steel or other methods, as these efforts exceed the inherent capabilities of D2 steel.
- Difficulty in Machining and Grinding. D2 steel is difficult to machine. The reason for this is its high hard carbide content, which is also one of the advantages of D2 steel mentioned earlier, like two sides of the same coin. Its machinability rating is 45% compared to 1% carbon steel, rated at 100%. The difficulty of machining D2 steel may lead to higher usage costs.
- Low corrosion resistance. D2 steel has a certain degree of corrosion resistance, but it is not high. It is not a true stainless steel. Under extreme conditions, D2 steel will still rust. The corrosion resistance of D2 steel is mainly due to its high chromium content. Much of the chromium in D2 is tied up in carbides, limiting its availability to form a robust passive layer against corrosion.
- Weldability. D2 steel has poor weldability, also due to its high carbide content. This may cause inconvenience when used as a knife.
If you want to learn more about the disadvantages, please read: What are the disadvantages of D2 tool steel?
Comparison with Other Knife Steels
- Vs. Martensitic Stainless Steels (e.g., 420, 440C). These are commonly used for cutlery because they balance corrosion resistance with good edge retention and hardness. While D2 might offer superior wear resistance in some specific contexts, it compromises significantly on corrosion resistance and general toughness compared to dedicated cutlery stainless steel. For more information, please read D2 Vs. 440C.
- Vs. High-Speed Steels (e.g., M2). M2 is a general-purpose high-speed steel often preferred for cutting tools due to its balanced combination of wear resistance, hot hardness, and toughness. M2 steel has higher toughness than D2 steel. In applications that require impact resistance, M2 is a better choice than D2. For more information, please read What is the difference between D2 and M2 tool steel.
- Vs. Powder Metallurgy (P/M) Tool Steels (e.g., CPM 10V, P/M M4, P/M T15). These materials offer significant improvements over conventionally processed D2 in terms of both toughness and wear resistance. P/M steels achieve a finer and more homogeneous distribution of carbides, which minimizes the negative impact of coarse carbides on toughness while maximizing wear resistance. For high-performance knives, P/M tool steels often overcome D2’s primary limitations.3
Summary
D2 tool steel is an ideal choice for knives, as its ability to maintain sharpness and wear resistance is its most significant advantage. However, its disadvantages should also be noted. For a general-purpose knife, particularly one that might be subjected to prying, chopping, or other shock loads, its inherent low toughness and susceptibility to chipping make it a less ideal choice compared to tougher tool steels (like some S-series or M-series) or specialized cutlery-grade stainless steels. The difficulty in grinding and the need for meticulous heat treatment to mitigate retained austenite also make D2 a more challenging material to work with for knife makers. In industrial knife applications, D2 is more suitable for industrial cutting tools such as shearing blades, slitting knives, and paper knives. This is because in these applications, even if the blade chips, it will not cause significant damage or accidents.
- Altan, T., & Tekkaya, A. E. (Eds.). (2012). Sheet Metal Forming: Processes and Applications (p. 324). ASM International. ↩︎
- Di Schino, A., & Sugimoto, K. (Eds.). (2017). Mechanical Properties and Microstructure of Forged Steel. MDPI. ↩︎
- Mesquita, R. A. (2014). Tool Steels: Properties and Performance. CRC Press. ↩︎
Get a Competitive Quote for Premium D2 Tool Steel
With over 20 years of forging expertise, Aobo Steel is your trusted partner for high-performance D2 steel. We provide not just materials, but solutions. Leverage our deep industry knowledge and reliable supply chain for your project’s success.
✉ Contact us by filling out the form below.