Heat treat D2 steel typically involves three basic steps: heating (austenitization), rapid cooling (quenching), and reheating to a lower temperature (tempering). At each stage, precise control of time and temperature is crucial for achieving the desired D2 steel properties and microstructure.
Specific Heat Treatment Steps for D2 Tool Steel
1. Preparation and Preheating
D2 steel must be degreased before heat treatment to prevent discoloration caused by oils on the steel surface.1 Placing D2 steel in a controlled neutral atmosphere, vacuum, or neutral salt furnace environment and wrapping it in stainless steel foil can prevent decarburization during heat treatment. This preparation is especially important for smaller pieces of D2 steel.
After applying surface protection, preheating (unhardened) must be performed on D2 steel before formal heat treatment, especially when a high volume of material (more than 30-50% of the initial block) has been removed. The purpose of preheating is to reduce the risk of deformation and cracking during subsequent heat treatment.
The steps for preheating are as follows: Slowly and evenly heat D2 steel to 1200–1250°F (649–677°C). Soak at this temperature for 1–2 hours per inch (25.4 mm) of thickness. Then, slowly cool to room temperature in the furnace.
It is best to start heating D2 steel from a cold furnace, as this allows for a slower, more uniform heating process. If the furnace has already been heated to the preheating temperature, we recommend placing the D2 material on top of the furnace for preheating to eliminate cold shrinkage and reduce thermal shock, thereby minimizing cracking.
2. Austenitizing (Hardening)
This is the second step in the heat treatment operation. Austenitizing transforms the ferrite-pearlite structure into austenite and dissolves a large portion of the carbides. D2 steel depends on the dissolution of various complex alloy carbides during austenitizing to develop its properties.
The temperature range for this step is 980–1025°C (1796–1877°F), and the soak time is typically 45-60 minutes per inch (1.8-2.4 minutes/mm) of thickness. For items under 1 inch (25.4 mm) thick, a minimum soaking time of 45-60 minutes is recommended. Over-soaking or over-heating can destroy the molecular structure and cause brittleness, while under-soaking leads to insufficient hardness.
3. Quenching
After soaking, the steel is rapidly cooled to a temperature below the transformation temperature, resulting in a hard martensitic structure. Quenching is the third step.
D2 is an air-hardening tool steel, and air quenching is the preferred method for quenching this type of steel. Air quenching can significantly reduce deformation and dimensional changes. However, for very large cross-sections, air cooling alone may not achieve full hardness; in such cases, oil quenching or agitated salt baths may be considered to ensure proper transformation.
If air cooling is selected, remove the D2 workpiece from the furnace and allow it to cool naturally to approximately 150°F (66°C). It is essential to keep the part sealed in its foil envelope until all visible red heat is gone to prevent contact with the atmosphere.
If straightening is required, it must be performed at a temperature above 400°F (205°C).
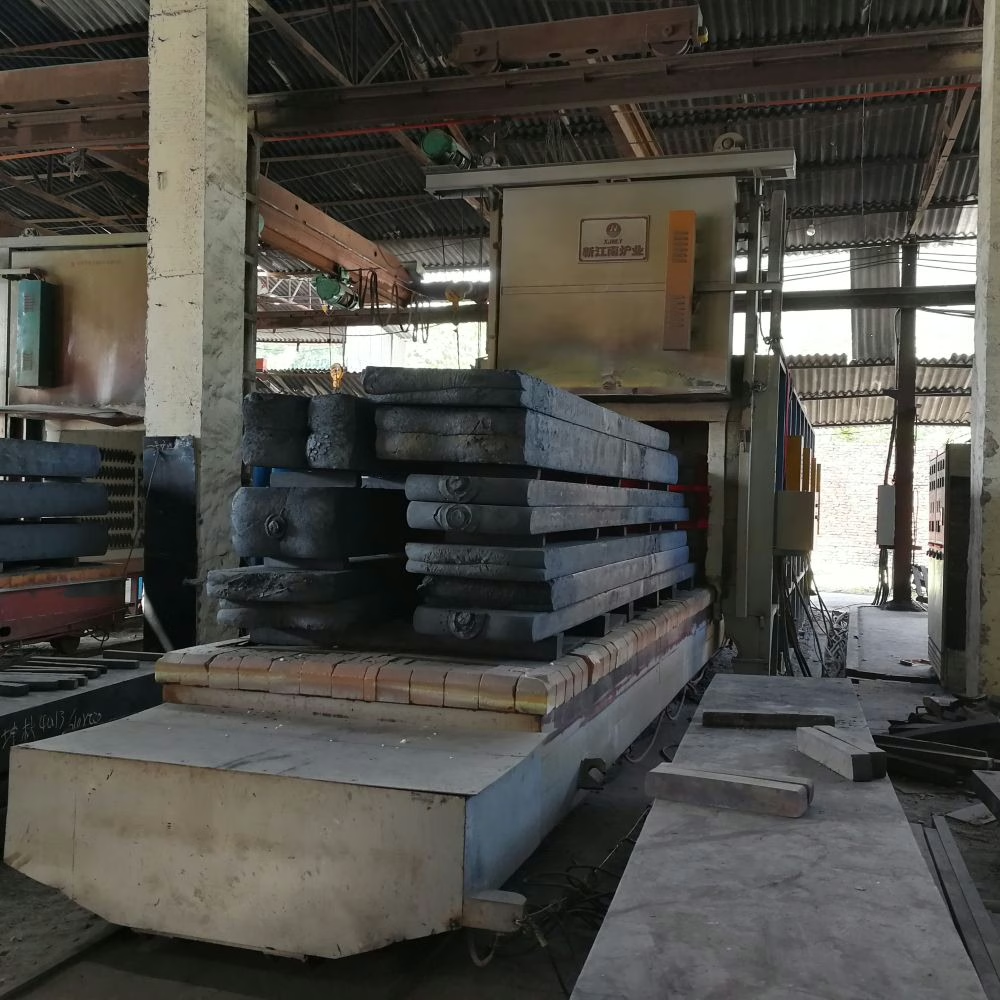
4. Tempering
Tempering (or drawing) is a thermal treatment of hardened steels to improve toughness and ductility, relieve internal stresses, and achieve desired mechanical properties. It transforms as-quenched martensite into tempered martensite. As-quenched martensite is very hard but also brittle, and without tempering, it is highly susceptible to cracking. Tempering also refines the grain structure.
Tempering must be carried out immediately after quenching, as soon as the parts reach a temperature of 125-150°F (52-65°C).
We recommend double tempering for D2, or even triple tempering, to improve wear resistance and stress relief. The temperature for the first tempering is 960°F (515°C), with a soaking time of 2 hours per inch (25mm) of cross-section. The second tempering must wait until the temperature has dropped to room temperature after the first tempering. Secondary tempering at 900°F (480°C), with soaking for 2 hours per inch of the cross-section.
Although a single tempering at 400°F (205°C) can achieve 62 HRC, we recommend double tempering at 900°F to improve wear resistance and eliminate stress.
For hardened D2 steel material, after significant grinding, welding, or electrical discharge machining (EDM), we also recommend tempering for stress relief. This is performed at a temperature of 25-50°F (14-28°C) lower than the previous tempering temperature. 2
Summary
In summary, the above is a common heat treatment scheme for D2 steel. There are several details to consider in this process, such as uneven heating, which can cause deformation or cracking. Overheating or over-soaking during austenitizing can lead to excessive grain growth, making the steel brittle. For the results of D2 steel heat treatment, D2 steel hardness measurement alone is insufficient to confirm whether the heat treatment is appropriate. Other performance indicators, such as strength, toughness, wear resistance, and microstructural characteristics, better reflect the quality.
- ASM International. (1991). ASM Handbook, Volume 4: Heat Treating. ASM International. ↩︎
- Leed, R. M. (2007). Tool and Die Making Troubleshooter. Society of Manufacturing Engineers (SME). ↩︎
Get a Competitive Quote for Premium D2 Tool Steel
With over 20 years of forging expertise, Aobo Steel is your trusted partner for high-performance D2 steel. We provide not just materials, but solutions. Leverage our deep industry knowledge and reliable supply chain for your project’s success.
✉ Contact us by filling out the form below.