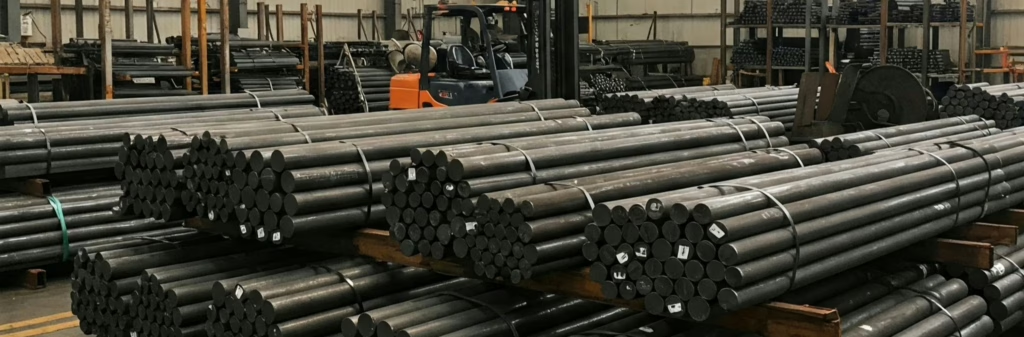
Hot Work Tool Steels Catalog
Hot Work Tool Steels Catalog
Click on any product to view details.
What is Hot Work Tool Steel?
Hot-work tool steel is typically used at temperatures above 200°C (390°F). At high temperatures, it maintains its hardness and dimensional stability. In contrast, ordinary steel loses hardness in high-temperature environments.
Composition and Alloying Elements
Hot work tool steels typically have medium carbon content, usually ranging from 0.35% to 0.45%. This relatively lower carbon content, compared to cold-worked steels, promotes higher toughness. Their resistance to softening at elevated temperatures is achieved by alloying elements such as chromium, tungsten, molybdenum, and vanadium, which collectively range from 6% to 25% of the composition.
- Chromium (Cr): A primary alloying element, typically 3% to 5%, contributes to hot hardness, wear resistance, and improves hardenability and oxidation resistance.
- Tungsten (W): Provides resistance to softening at high temperatures (red hardness) and wear resistance by forming stable carbides. It also contributes to hot hardness and can be present in substantial amounts (e.g., 9% to 19%) in tungsten-base hot work steels. However, high tungsten content can reduce toughness and resistance to thermal shock, making them unsuitable for water cooling during operation.
- Molybdenum (Mo): Similar to tungsten, it is crucial for hot hardness, increased resistance to tempering, and forms wear-resistant carbides. Molybdenum has about double the potency of tungsten in its effect on hot hardness.
- Vanadium (V): Forms very hard carbides (MC type) that significantly increase wear resistance and hot hardness.
- Cobalt (Co): When added, it primarily increases hot hardness, enhancing cutting efficiency at high tool temperatures. Cobalt-containing steels generally exhibit higher hot hardness.
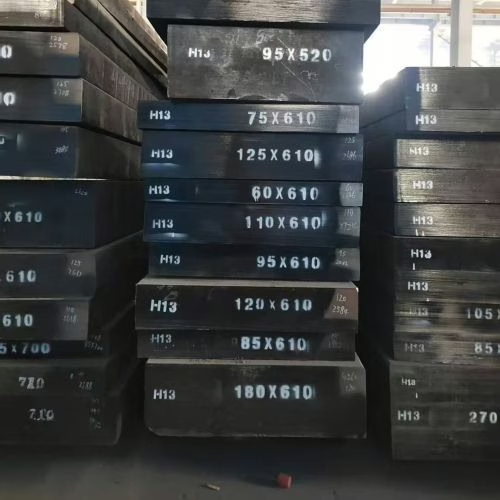
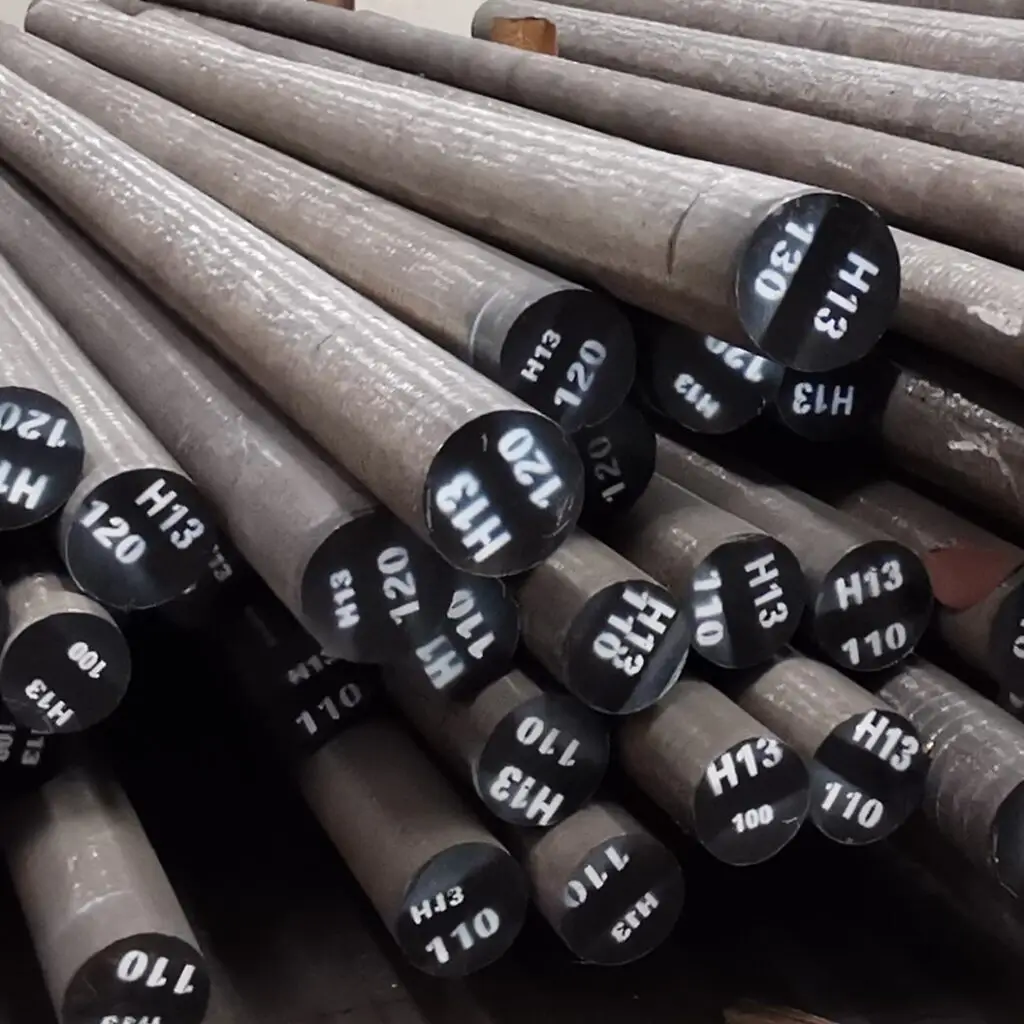
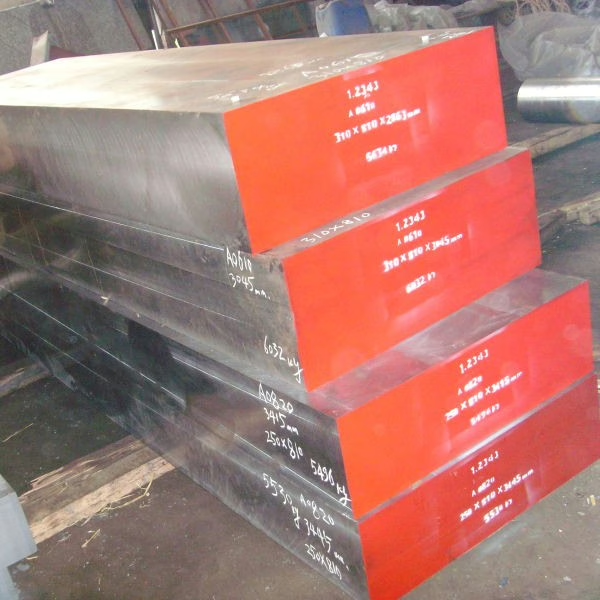
Properties
- Hot Hardness (Red Hardness). This is the most important property, referring to the ability to maintain hardness at elevated temperatures, often up to 650°C (1200°F) or higher for brief periods.
- Wear Resistance. Hot work tools are subjected to abrasive action from hot metals and require resistance to wear, including erosive wear (washing) at high temperatures.
- Toughness. This is the ability to resist chipping, breaking, and crack propagation under mechanical and thermal shock. Toughness is often balanced against hardness and wear resistance, as increasing one may decrease the other.
- Resistance to Thermal Fatigue (Heat Checking). This refers to the ability to withstand repeated cycles of rapid heating and cooling without developing networks of fine cracks on the tool surface. Heat checking is a common failure mode in die-casting dies.
- High-Temperature Strength. The capacity to withstand sustained loads at elevated temperatures without undergoing plastic deformation.
- Hardenability. Hot work steels are designed for deep hardening, often by air cooling, which helps minimize distortion during heat treatment.
Classification
Here, we classify according to the American AISI standard(AISI H-Series). Hot work tool steels are primarily classified under the AISI H-series. They are subdivided into three main groups based on their principal alloying elements:
- Chromium Hot-Work Steels (H10-H19): These are the most widely used, especially H11, H12, and H13. They offer a good balance of properties, including excellent toughness and shock resistance, good resistance to heat softening, and high hardenability. They are characterized by low distortion during hardening and can often be water-cooled in service without cracking.
- Tungsten Hot-Work Steels (H21-H26): Known for their very high resistance to high-temperature softening and washing due to high tungsten content. However, they generally have lower toughness and are more susceptible to brittle fracture and thermal shock, making rapid water cooling in service risky.
- Molybdenum Hot-Work Steels (H42, H43): These steels are similar in characteristics and uses to tungsten hot-work steels, offering comparable resistance to softening at elevated temperatures. They are generally more resistant to heat checking than tungsten types but require careful heat treatment to avoid decarburization.
Heat Treatment
To achieve optimal performance, hot work tool steel must undergo heat treatment, including quenching and tempering. Most hot work tool steels are air-hardening steels, which helps reduce the risk of material deformation.
Applications
Hot work tool steels are extensively used in manufacturing operations involving the shaping, forming, or cutting of materials at high temperatures. Common applications include:
- Hot Forging Dies: For steel forgings, aluminum, and magnesium.
- Extrusion Dies: For aluminum, magnesium, brass, and steel.
- Die Casting Dies: For aluminum, zinc, and magnesium, and for brass.
- Hot Shear Blades: For cutting heated materials.
- Hot Rolling Mill Rolls: For medium to long runs and special materials at high temperatures.
- Plastic Injection Molds: Where operating temperatures can reach up to 250°C (480°F).
- Other tools: Mandrels, punches, and piercer points for hot work applications.
Distinction from other Tool Steels
- Vs. Cold Work Tool Steels: Hot work steels are designed for temperatures above 200°C (390°F), whereas cold work tool steels are for applications typically below 200°C (390°F), often at room temperature. Hot work steels generally have lower carbon content, and their final hardness is usually determined by desired toughness rather than maximum wear resistance (40-50 HRC vs. ~60 HRC for cold work steels). Using cold-worked steels for hot applications would lead to annealing or cracking due to thermal shock.
- Vs. High-Speed Tool Steels (HSS): While high-speed steels also exhibit excellent hot hardness (retaining a keen cutting edge up to 650°C/1200°F or higher), they are primarily developed for metal-cutting operations at high speeds. Hot work steels are tailored explicitly for forming and shaping applications, offering a balance of hot hardness, toughness, and thermal fatigue resistance. High-speed steels often have higher wear resistance and hot hardness but may possess lower toughness compared to many hot-work steels.
FAQ
Hot work tool steels are a class of alloy steels designed to resist softening at elevated temperatures, typically used for metal-forming processes where tools themselves reach temperatures between 315 and 650 °C (600 and 1200 °F).
There is no single “best” steel; selection depends on balancing hot hardness (resistance to softening), toughness (resistance to breakage), and wear resistance for the specific application.
Tool steels are categorized into various groups based on their composition, application, or heat treatment, including High-Speed (M and T series), Hot-Work (H series), Cold-Work (A, D, O series), Shock-Resisting (S series), Low-Alloy Special-Purpose (L series), Low-Carbon Mold (P series), and Water-Hardening (W series) tool steels.
Grinding itself generates significant heat at the workpiece surface, which can affect surface properties and cause residual stresses. While grinding involves heat, it is distinct from bulk hot working processes like forging or rolling, where the entire workpiece is heated to a plastic state for deformation.
Hot work tool steels are used for applications where the tool’s operating temperature exceeds 200°C (390°F), requiring resistance to softening, thermal fatigue, and high-temperature wear53…. Cold work tool steels are for operations below 200°C (390°F), primarily needing high hardness, wear resistance, and toughness at room temperature14….
Common grades include chromium-base steels (H10, H11, H12, H13, H14, H19), tungsten-base steels (H21, H22, H23, H24, H25, H26), and molybdenum hot-work steel (H42).
Disadvantages can include surface oxidation and scale formation, difficulties in dimensional control due to non-uniform contraction during cooling, potential for grain growth or degradation of properties at excessively high temperatures, and shorter tool life due to heating and abrasive scales108….
Cold work tool steels are used for tooling operations where the working temperature is generally below 200°C (390°F), typically at room temperature. They are selected for their high hardness, good toughness, and high resistance to wear under shock, pressure, or abrasion.
It’s called tool steel because these alloys are specifically designed and processed (often with special heat treatments like hardening and tempering) to manufacture tools, dies, and molds that cut, shape, or form other materials, including metals, plastics, wood, and concrete, under severe service conditions.