H11 tool steel and H13 tool steel are both hot work tool steels. They belong to the H series of the American Society for Testing and Materials (ASTM) system.
H11 and H13 are representative of hot work tool steels. They offer a good balance of cost and performance, making them a reference point for various applications in hot-forming molds. These materials were initially developed for die casting and exhibit high hardenability, minimal deformation during heat treatment, minimal oxidation tendency, good tempering performance, resistance to liquid aluminum corrosion, and high resistance to thermal fatigue.
The primary difference between H11 and H13 steel is that H13 contains approximately 0.5% more vanadium. This additional vanadium content further increases hot hardness and resistance to tempering, but it may also slightly reduce toughness, especially during quenching and tempering.
H13 is slightly better resistant to softening after heat treatment, but its toughness is slightly lower. Compared to H11, H13 may tend to have an uneven distribution of vanadium carbides. This is especially important under homogenization manufacturing conditions to maximize toughness.
This article compares H11 and H13 based on certain data. Some of the data is sourced from literature and has been cited accordingly.
Chemical composition of h11 and H13
AISI Type | UNS No. | C (%) | Mn (%) | Si (%) | Cr (%) | Ni (%) | Mo (%) | W (%) | V (%) |
H11 | T20811 | 0.33-0.43 | 0.20-0.50 | 0.80-1.20 | 4.75-5.50 | 0.30 max | 1.10-1.60 | … | 0.30-0.60 |
H13 | T20813 | 0.32-0.45 | 0.20-0.50 | 0.80-1.20 | 4.75-5.50 | 0.30 max | 1.10-1.75 | … | 0.80-1.20 |
Major Factors comparison of H11 and H13 tool steel
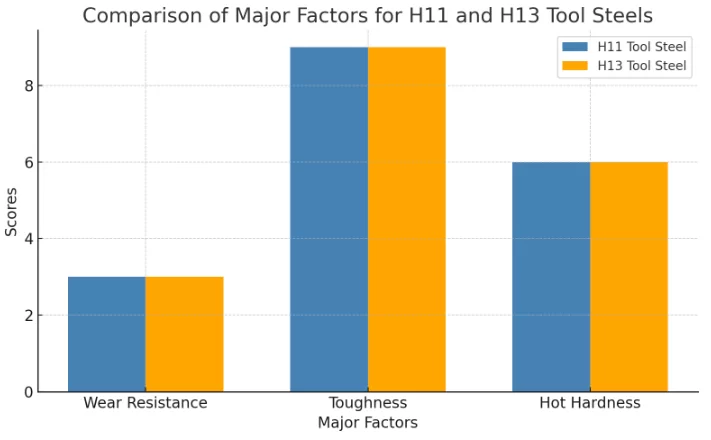
- Wear Resistance: H11 and H13 have the same value of 3, indicating equal wear resistance.
- Toughness: Both have a value of 9, suggesting high toughness for both types.
- Hot Hardness: Both have the same value of 6, indicating similar hot hardness properties.
Based on this table, H11 and H13 appear to have very similar properties in wear resistance, toughness, and hot hardness.
Comparison of manufacturing factors for H11 and H13 tool steels
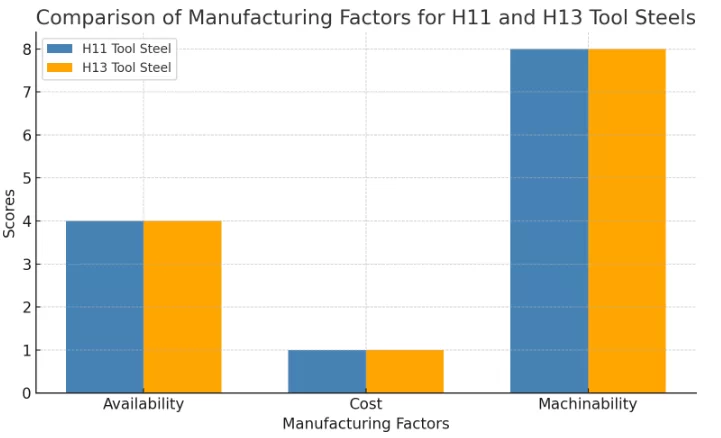
- Availability: Both H11 and H13 tool steel have an availability rating of 4, suggesting they are equally available.
- Cost: Both types of steel have a cost rating of 1, indicating they are similarly priced.
- Machinability: Both H11 and H13 have a machinability rating of 8, suggesting they are both relatively easy to machine.
The table shows that H11 and H13 tool steel are similar regarding these three manufacturing factors.
Comparison of other parameters
Factor | H11 tool steels | H13 tool steels |
Usual Working Hardness, HRC | 38-55 | 40-53 |
Depth of Hardening | D | D |
Finest Grain Size at Full Hardness, Shepherd Standard | 8 | 8 |
Surface Hardness as-Quenched, HRC | 53-55 | 51-54 |
Core Hardness (25 mm, or 1 in., diam round), HRC | 53-55 | 51-54 |
Quenching Medium | A | A |
Hardening Temperature, °C (°F) | 995-1025 (1825-1875) | 995-1040 (1825-1900) |
Dimensional Change on Hardening | L | L |
Safety on Hardening | H | H |
Susceptibility to Decarburization | H | H |
Approximate Hardness as-Rolled or Forged, HB | 500 | 500 |
Annealed Hardness, HB | 192-229 | 192-229 |
Annealing Temperature, °C (°F) | 845-900 (1550-1650) | 845-900 (1550-1650) |
Tempering Range, °C (°F) | 540-650 (1000-1200) | 540-650 (1000-1200) |
Forging Temperature, °C (°F) | 1065-1150 (1950-2100) | 1065-1150 (1950-2100) |
H11 and H13 tool steels share many similarities regarding their mechanical properties, heat treatment characteristics, and forging capabilities. The primary difference lies in their hardness range, with H13 offering slightly higher hardness for more demanding applications. The choice between these two steels depends on the specific requirements of the intended application, such as the level of wear resistance, toughness, and dimensional stability needed.
Tensile Properties of H11 and H13 Tool Steels at Elevated Temperatures
Steel Type | Testing Temperature (°C) | Testing Temperature (°F) | Tensile Strength (MPa) | Tensile Strength (ksi) | Yield Strength (0.2% offset) (MPa) | Yield Strength (0.2% offset) (ksi) | Elongation (50 mm) (%) | Reduction of Area (%) | Room-Temperature Hardness (HRC) Before testing | Room-Temperature Hardness (HRC) After testing |
H11 | Room | Room | 1806 | 262 | 1482 | 215 | 10 | 35.8 | 50 | 50 |
150 | 300 | 1689 | 245 | 1358 | 197 | 10.1 | 36.1 | 50 | 50 | |
260 | 500 | 1600 | 232 | 1345 | 195 | 9.8 | 34.5 | 50 | 50 | |
345 | 650 | 1579 | 229 | 1317 | 191 | 10 | 35.2 | 50 | 50 | |
425 | 800 | 1510 | 219 | 1289 | 187 | 11.4 | 38.7 | 50 | 50 | |
480 | 900 | 1427 | 207 | 1145 | 166 | 12.2 | 38.9 | 50 | 50 | |
540 | 1000 | 1241 | 180 | 965 | 140 | 11 | 35.4 | 50 | 50 | |
595 | 1100 | 979 | 142 | 724 | 105 | 12.8 | 46.2 | 50 | 47 | |
650 | 1200 | 586 | 85 | 434 | 63 | 18.9 | 66.6 | 50 | 41 | |
H13 | 480 | 900 | 1531 | 222 | – | – | 9 | 37 | 52 | – |
540 | 1000 | 1413 | 205 | – | – | 11 | 43 | 52 | – | |
595 | 1100 | 1193 | 173 | – | – | 15 | 49 | 52 | – | |
650 | 1200 | 814 | 118 | – | – | 22 | 59 | 52 | – |
Note:
- The “-” in the Yield Strength columns for H13 steel indicates that the data was unavailable.
- The Room-Temperature Hardness (HRC) column shows values before and after testing, separated by a comma.
- Data from Teledyne VASCO. Allegheny Ludlum Industries, and Universal-Cyclops Steel Corp.
CVN impact toughness of H11 and H13 tool steels as a function of testing temperature.
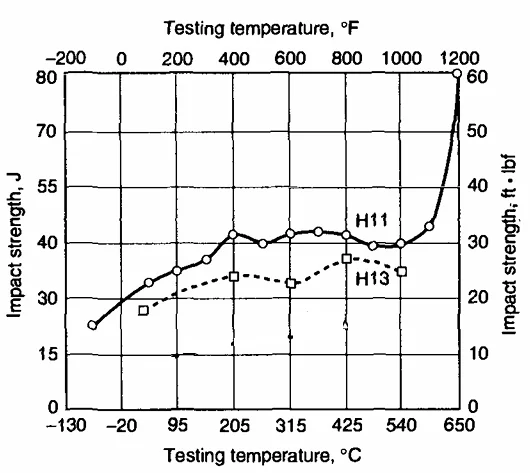
This graph suggests that H11 and H13 become more resistant to impact at higher temperatures. However, H13 is more sensitive to temperature changes, showing a more significant increase in impact strength with rising temperatures.