A2 Steel: Engineered for Toughness and Precision
Experience superior wear resistance and stability with A2 steel from Aobo Steel – quality you can rely on.
Reliable A2 Tool Steel for High Performance and Durability
At Aobo Steel, we provide factory-direct A2 tool steel crafted for manufacturers who demand durability, precision, and quality. Engineered with exceptional toughness and wear resistance, A2 tool steel is a trusted choice for cold work tooling and versatile industrial applications.
what is a2 steel? A2 tool steel is a deep-hardening, air-hardening tool steel. Due to its air-hardening properties, the deformation caused by hardening is about one-fourth that of tungsten-based oil-hardening tool steel. Its wear resistance is between chromium-type and high-carbon high-chromium-type tool steels, but its toughness is superior. This makes it especially suitable for applications requiring good wear resistance, toughness, and dimensional stability. It is widely used in blanking dies, forming dies, rolling dies, punch dies, calendering dies, thread rolling dies, and specific cutting blades.
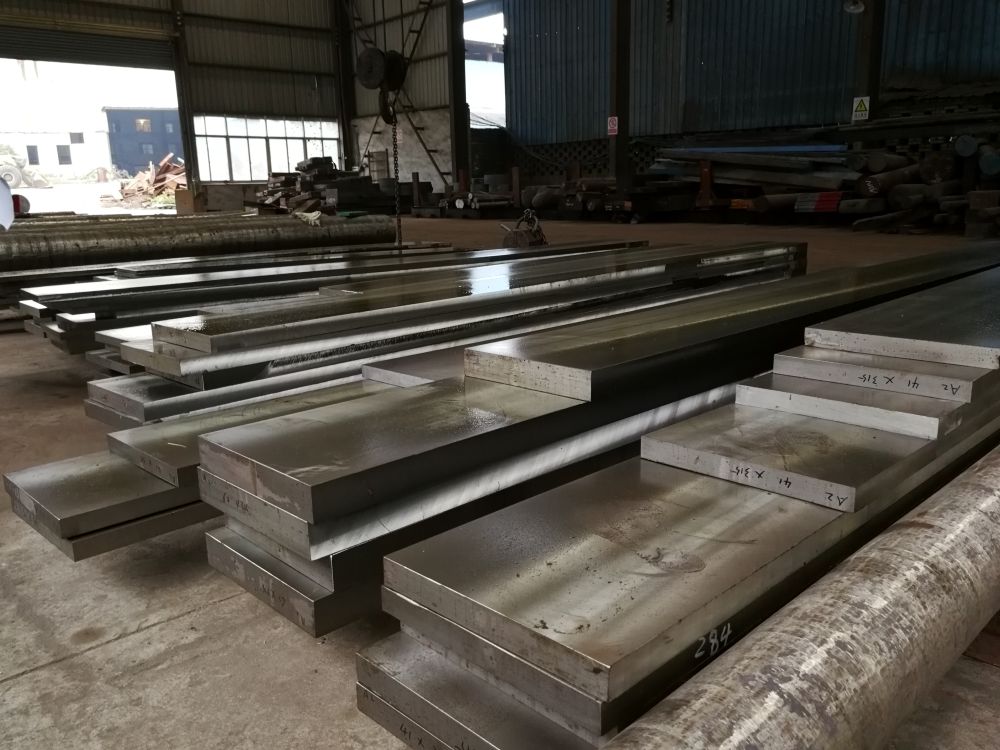
A2 steel Applications
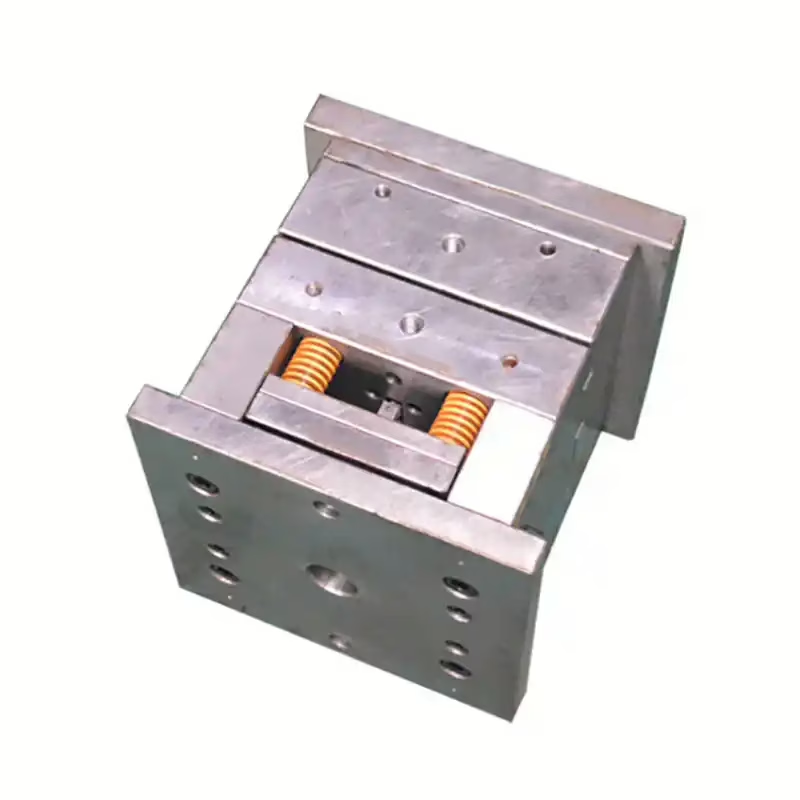
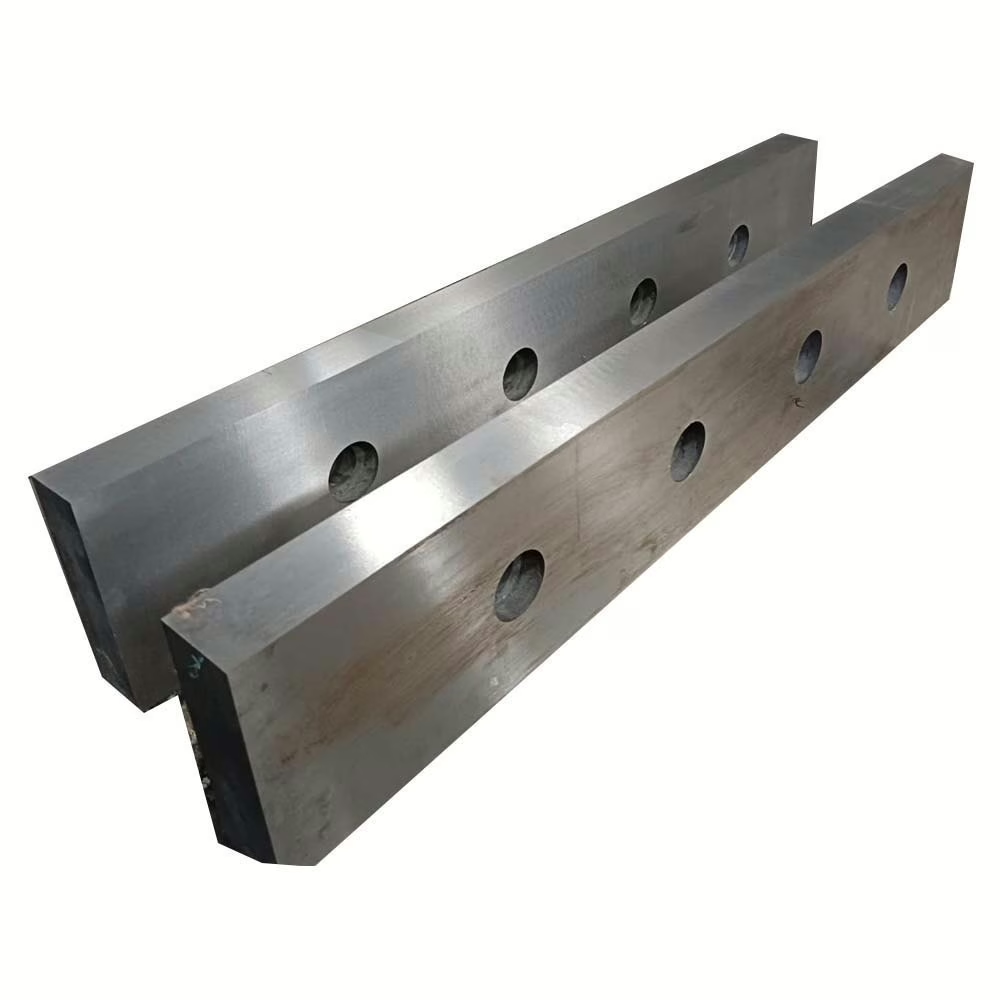
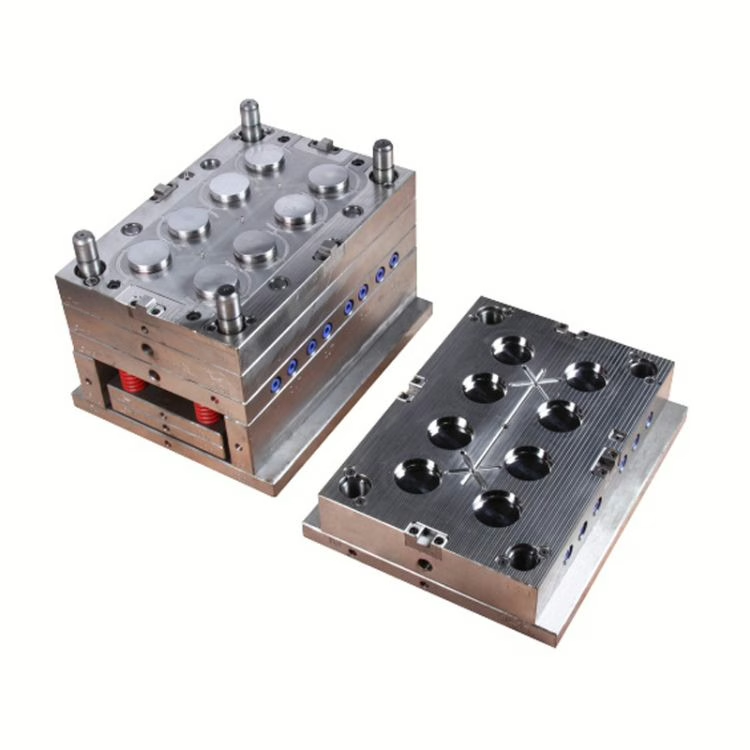
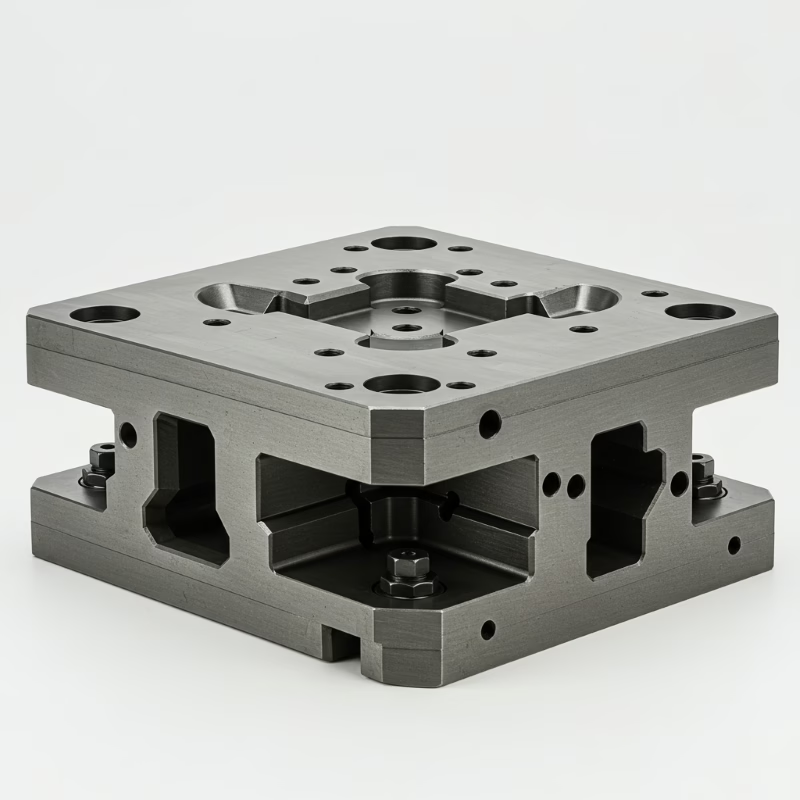
A2 steel excels in producing precise stamping dies, such as drawing dies, stretching dies, and forming dies, and can withstand repeated impact loads and wear.
Blanking Dies:
A2 steel’s toughness and wear resistance balance are ideal for blanking dies used in stamping and cutting operations.Forming Tools:
Its toughness ensures long service life, making A2 perfect for forming tools that endure mechanical stress.Punches and Shear Blades:
A2 steel’s wear resistance allows for producing durable punches and shear blades that withstand repeated use.Plastic Molds:
A2 offers excellent dimensional stability and resistance to stress, making it a top choice for precision plastic injection molding.
Aobo Steel: Your A2 Tool Steel Expert
Aobo Steel stands out as your A2 tool steel supplier, providing steel renowned for its durability and wear resistance. A2 steel’s excellent toughness makes it ideal for applications like punches and dies, ensuring high performance under stress. Trust Aobo for quality and reliability in every piece.
A2 tool steel properties
1. A2 tool steel chemical composition
Element | Carbon (C) | Chromium (Cr) | Molybdenum (Mo) | Vanadium (V) | Manganese (Mn) | Silicon (Si) | Phosphorus (P) | Sulfur (S) |
Percentage (%) | 0.95 – 1.05 | 4.75 – 5.50 | 0.90 – 1.40 | 0.15 – 0.50 | 0.40 – 1.00 | 0.30 – 0.90 | ≤ 0.03 | ≤ 0.03 |
2. A2 steel equivalent
- DIN/ISO: 1.2363 (X100CrMoV5),
- JIS (Japan): SKD12
- China(GB/T 1299 standard): Cr5Mo1V
3. A2 steel properties
3.1 Critical Point Temperature
Critical Point | Temperature (Approximate) / °C |
---|---|
Ac₁ | 795 |
Accm | — |
Ms | 168 |
3.2 Linear Expansion Coefficient
Temperature / °C | Linear Expansion Coefficient α / × 10⁻⁶ °C⁻¹ |
---|---|
20 ~ 100 | 8.2 |
20 ~ 300 | 11.3 |
20 ~ 500 | 12.4 |
20 ~ 700 | 12.9 |
3.3 Other Physical Properties
Property | Value |
---|---|
Density (g/cm³) | 7.84 |
Elastic Modulus E (Room Temperature) / MPa | 203,000 |
Specific Heat Capacity c_p / [J/(kg·K)] | 460.55 |
4. A2 Tool Steel Heat Treatment Guide
Proper heat treatment is essential to achieve the target mechanical properties for A2 tool steel. Understanding and controlling these processes ensures the optimal performance and service life of your tools and components. At Aobo Steel, with our extensive experience in tool steels, we provide this guide to the key heat treatment stages for A2.
4.1 Annealing A2 Tool Steel
Annealing prepares A2 steel for machining by reducing hardness and relieving internal stresses.
- Process: Heat the steel uniformly to 1650°F (899°C). Hold at this temperature for 2 hours per inch (or 4.7 min/mm) of the thickest section.
- Cooling: Cool slowly at a rate of 40°F (22°C) per hour down to 900°F (482°C). After reaching 900°F, allow it to air cool to room temperature.
- Result: This process typically yields a maximum hardness of 235 HB, improving machinability. Annealing creates a structure primarily of ferrite and coarse pearlite.
4.2 Hardening A2 Tool Steel
Hardening increases the strength and wear resistance of A2 steel by transforming its structure into hard martensite. This involves preheating, austenitizing, and quenching.
4.2.1 Preheating
Preheating minimizes thermal shock and reduces the risk of cracking, especially for parts with varying thicknesses.
- Process: Heat the steel to 1200°F (650°C). A typical preheat time is 10-15 minutes.
4.2.2 Austenitizing
This step transforms the steel’s structure into austenite, necessary for hardening.
- Process: Heat the preheated steel to the austenitizing temperature, typically 1775°F (970°C).
- Soaking: Hold at this temperature for a sufficient time to ensure complete transformation and carbide dissolution. A standard guideline is 1 hour per inch (25 mm) of thickness. The exact temperature influences final grain size and properties.
4.2.3 Quenching
Rapid cooling transforms the austenite into martensite.
- Process: A2 is an air-hardening steel. Quench the part in air until it reaches approximately 150°F (65°C). Tempering should follow immediately.
- Note: Some minor straightening can be done between 1050°F (565°C) and 400°F (205°C) before significant hardening occurs. Be aware that some retained austenite (untransformed structure) might remain after quenching.
4.3 Tempering A2 Tool Steel
Tempering is performed immediately after quenching to reduce brittleness, relieve stresses, and increase toughness. Double tempering is strongly recommended for A2 steel.
4.3.1 First Temper
- Process: Heat the hardened steel to the desired tempering temperature, often starting around 400°F (205°C).
- Soaking: Hold at temperature for 2 hours per inch (25 mm) of the thinnest section. This stabilizes the newly formed martensite.
4.3.2 Second Temper
- Process: The second temper further refines the structure and stress-relieves the material. A common practice is to temper at a temperature 25°F (14°C) lower than the first temper.
- Soaking: Use the same holding time: 2 hours per inch (25mm) of the thinnest section.
- Result: Double tempering improves toughness and wear resistance, aids stress relief, and helps transform retained austenite. Final hardness depends significantly on the chosen tempering temperature (higher temperatures generally decrease hardness but increase toughness). As-quenched hardness is typically around Rc 64.
4.4 Stress Relief
Stress relieving reduces internal stresses introduced by machining or previous heat treatments without significantly changing hardness.
- Unhardened A2: Heat slowly to 1200–1250°F (649–677°C). Soak for 2 hours per inch (4.7 min/mm) of thickness. Cool slowly (furnace cool preferred) to room temperature.
- Hardened A2: Stress relief is highly recommended after heavy grinding, welding, or EDM. Heat to a temperature 25°F to 50°F (14°C to 28°C) below the final tempering temperature used. Hold for the standard time (2 hours per inch/25mm) and air cool.
4.5 Dimensional Stability
A2 tool steel offers good dimensional stability during heat treatment compared to many other tool steels. When correctly air-quenched from the proper hardening temperature, anticipate an expansion of about 0.001 in./in. (0.001 mm/mm). Keep in mind that part geometry and potential distortions like bending or twisting can affect the final dimensions.
4.6 Forging Process Specifications
Item | Heating Temperature (°C) | Initial Forging Temperature (°C) | Final Forging Temperature (°C) | Cooling Method |
---|---|---|---|---|
Steel Ingot | 1100 ~ 1150 | 1050 ~ 1100 | 850 ~ 900 | High-temperature annealing, pit cooling, or sand cooling |
Steel Billet | 1050 ~ 1100 | 1000 ~ 1050 | 850 ~ 900 | Pit cooling or sand cooling |
A2 VS O1 Steel: A brief look at their differences and uses
1. Heat Treatment
A2 steel:
Austenitizing temperature: 945-995°C (1730-1750°F)
Typical tempering process: 205-540°C (400-1000°F) double tempering
Hardness range: 46-63 HRC
O1 Steel:
Austenitizing temperature: 790°C (1450°F) Oil quenching
Typical tempering process: Single tempered at 205°C (400°F)
Hardness range: 58-62 HRC
2. Mechanical Properties Comparison
O1’s peak torsional strength is lower than that of A2’s. A2’s impact toughness is stronger than that of O1’s, and A2’s wear resistance is stronger than that of O1’s.
3. Comparison of typical applications
A2 steel applications:
High-precision punching dies (e.g., automotive nut punching dies)
Shear tools requiring toughness
Complex-shaped dies (using air-quenching properties)
O1 steel applications:
Small punches/thimbles (e.g. nut split pins)
Gauges/jigs (simple shaped parts)
Low-load cutting tools
4. Cost vs. machinability
In terms of machinability, O1 steels are superior to A2 steels, which are more costly than O1 steels because of the need for secondary tempering and because of the Mo element in their composition.
5. Suggestions for selection:
A2: high hardenability, complex shaped tools, high toughness requirements of the occasion
O1: Simple shaped parts, cost-sensitive applications, small cross-section size tools
Your Trusted Partner for A2 Tool Steel
When precision, durability, and performance matter, choose A2 tool steel from Aobo Steel. Join countless satisfied manufacturers who’ve streamlined their production with our unmatched quality and service.
A2 Tool Steel Equivalents: DIN 1.2363 and JIS SKD12
In the German and Japanese standard systems, A2 steel is equivalent to DIN 1.2363 and JIS SKD12 grades, respectively. They can be substituted for each other. They are all cold work die steels and air-hardening chromium steels. The steel has evenly distributed carbides, possessing a certain impact toughness and good wear resistance. It also has good air-quenching performance, small dimensional deformation during air quenching, uniform and fine carbides, good toughness, and high wear resistance.
Introduction to DIN 1.2363 steel
1.2363 Chemical composition
Carbon (C) | Chromium (Cr) | Manganese (Mn) | Silicon (Si) | Vanadium (V) |
0.95 – 1.05 | 4.75 – 5.50 | 0.60 – 1.00 | 0.10 – 0.40 | 0.15 – 0.50 |
1.2363 steel Physical properties
Density: Approximately 7750 kg/m³ at room temperature
Coefficient of Thermal Expansion: 6.5 × 10⁻⁶ per °F from 68°F, or 11.6 × 10⁻⁶ per °C from 20°C
Thermal Conductivity: at 20°C: 15.9 W/(m·K), at 350°C: 26.8 W/(m·K), at 700°C: 29.2 W/(m·K).
Specific Electrical Resistivity: 0.33 μΩ·m at 24°C
Introduction to JIS SKD12
SKD12 Chemical composition
Carbon (C) | Chromium (Cr) | Molybdenum (Mo) | Vanadium (V) | Manganese (Mn) | Silicon (Si) | Phosphorus (P) | Sulfur (S) |
0.95 – 1.05 | 4.75 – 5.50 | 0.90 – 1.20 | 0.15 – 0.50 | 0.50 – 0.70 | 0.10 – 0.40 | ≤ 0.030 | ≤ 0.030 |
SKD12 steel Physical properties
Property | Value |
---|---|
Density | 7.8 g/cm³ |
Thermal Conductivity | 25.0 W/m·K |
Hardness (After Heat Treatment) | 58 – 62 HRC |
Elastic Modulus | 210 GPa |
Tensile Strength | 1570 MPa |
Melting Point | 1450°C (2642°F) |
FAQs
- What is A2 steel?
A2 steel is an air-cooled, medium-alloyed cold work tool steel known for its high wear resistance, good toughness, and small heat treatment deformation. It is commonly used in the manufacture of a variety of cold work molds. - Is A2 a good knife steel?
A2 steel is a good knife steel because of its combination of high wear resistance, good toughness, and easy heat treatment. It is so commonly used in the production of cutting tools. - Is A2 steel better than A4?
A4 steel generally has slightly better wear resistance than A2 steel and can be hardened at lower austenitizing temperatures, but both have good toughness and low heat treat distortion. - Is A2 better than D2 steel?
D2 steel has better wear resistance than A2 steel but is less tough than A2 steel. - Does A2 rust?
A2 steel will rust, but its resistance to rust is somewhat better than ordinary carbon steel because it contains a moderate amount of chromium.