1. The Short Answer: Yes, With the Right Approach
For anyone working with H13 tool steel, a common question is: Can it be welded? The straightforward answer is yes, H13 steel is readily weldable. However, because it’s a high-performance hot work tool steel, achieving a successful, durable weld requires specific procedures and careful attention to detail. Skipping these steps can lead to problems. At Aobo Steel, with our decades of experience, we aim to provide you with the correct information to handle H13 tool steel effectively.
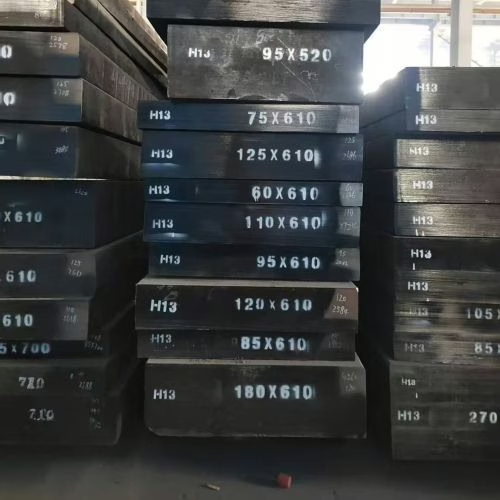
2. Understanding H13 Steel: Why Welding Needs Special Care
H13 (also known as 4Cr5MoSiV1 or Nu-Die V) is a 5% chromium, air-hardening tool steel. Its composition, including significant amounts of Chromium, Molybdenum, and Vanadium, gives it excellent toughness, wear resistance, and high-temperature resistance. This makes it ideal for applications like die casting, extrusion dies, forging dies, and plastic injection molds.
2.1 Key Properties of H13 tool steel:
- Composition: Approx. 0.32-0.45% C, 4.75-5.50% Cr, 1.10-1.75% Mo, 0.80-1.20% V, 0.80-1.20% Si.
- Characteristics: High hot strength, good toughness, excellent temper resistance, good wear resistance.
- Hardness: Can be heat-treated to high hardness levels (e.g., 52-55 HRC or even higher, depending on application and treatment).
2.2 The Air-Hardening Challenge
The key factor influencing H13 welding is its air-hardening nature. This means that even relatively slow cooling in air after heating, such as during welding, can cause the Heat Affected Zone (HAZ) – the area adjacent to the weld – to become very hard and brittle, resulting in the formation of martensite structures. This hardness increases susceptibility to cracking, especially hydrogen-induced cracking, if precautions aren’t taken.
3. Essential Procedures for Welding H13 Tool Steel Successfully
Based on our experience and established industry practices, here’s what you need to focus on when welding H13:
3.1 Recommended Welding Process: TIG/GTAW
The Gas Tungsten Arc Welding (GTAW) process, commonly known as TIG welding, is highly recommended for H13, particularly for tool and die repairs. It offers excellent control of the heat input and produces high-quality welds. An inert shielding gas, typically Argon, is essential to protect it from air contamination.
3.2 The Critical Role of Pre-heating
Pre-heating the H13 workpiece before welding is crucial. This minimizes the temperature difference between the weld area and the surrounding base metal, reducing thermal stress and the risk of cracking as the weld cools.
- Temperature Range: Pre-heat temperatures typically range from 110°C (230°F) up to 375°C (705°F) or even 400°C (750°F).
- Factors to Consider: The exact temperature depends on the size and thickness of the material, the complexity of the weld, and whether it’s in a crack-sensitive location. A larger component generally requires a higher preheat temperature.
3.3 Choosing the Right Filler Metal
Selecting the correct filler material is crucial to achieve the right properties of the final weld deposit.
- Matching Hardness (52-55 HRC): Use an H13 filler wire. This is the standard choice for achieving properties similar to the base metal.
- Alternative Medium Hardness: If H13 wire isn’t available, a general-purpose medium-hard tool steel filler suitable for hot work applications can be used.
- Higher Hardness (Approx. 60 HRC): For applications requiring maximum hardness, a tough filler wire, such as a high-speed steel type (e.g., M-series), may be necessary.
- Low Hydrogen: Always opt for low-hydrogen consumables (such as electrodes or wires) if applicable to the chosen process, to reduce the risk of hydrogen cracking.
3.4 Post-Weld Cooling and Heat Treatment (Annealing)
How you cool the part after welding is just as crucial as pre-heating. Because H13 is air-hardening, rapid cooling is detrimental.
- Slow Cooling: After welding is complete, the part must be cooled slowly down to room temperature. This can involve wrapping it in an insulating blanket or burying it in a suitable insulating medium. Cooling tool fast invites stress cracking.
- Spheroidizing Anneal: Following slow cooling, a full spheroidizing anneal is strongly recommended, especially for significant repair work or before any subsequent hardening and tempering. Annealing relieves internal stresses created during welding and softens the HAZ, improving toughness and machinability. The typical process includes heating to approximately 871°C (1600°F), soaking, and then slowly and carefully cooling. The resulting hardness is usually around 192-235 HBW.
4. Final Thoughts from Aobo Steel
Welding H13 tool steel isn’t only possible, but it’s also a common practice in tool maintenance and modification. The key is understanding the material’s air-hardening nature and meticulously following the correct procedures: proper preheating, selecting the appropriate filler metal, controlling the welding heat input, slow post-weld cooling, and applying necessary post-weld heat treatment, such as annealing.
Follow these guidelines to achieve strong, reliable welds in H13 steel. If you have specific questions about welding H13 for your application, please don’t hesitate to contact the Aobo Steel team – we’re always happy to share our expertise.
🔥 Special Offer on H13 Tool Steel — Direct from Manufacturer!
- ✅ Ready Stock for Standard Sizes — Fast delivery within 7 days.
- ✅ Custom Size Forging Available — Quick quote within 12 hours.
- ✅ Free Metallurgical Report — Know exactly what you’re buying.
- ✅ 20+ Years of Tool Steel Expertise — Trusted by 40+ global suppliers.
👇Get an instant quote now — Your project deserves real quality.👇