In the tool steel industry, ESR means Electroslag Remelting.
Some steel grades go through remelting processes like vacuum arc remelting (VAR) and electro-slag remelting (ESR) to improve quality. As molds get bigger and require more specialized features, the use of remelted steel has been growing.
Compared to VAR, ESR offers several advantages. It has a lower cost because it doesn’t require vacuum equipment. Additionally, the electro slag refining process improves the surface quality of the steel ingot. This allows even large cross-section ingots to achieve a uniform structure.
Although various technical methods and applications exist for electro-slag metallurgy, ESR remains its basic and core technology. This article will introduce the ESR process and its significance. AoboSteel can provide clients with tool steel manufactured using the ESR process.
Basic Principles of the ESR Process
The ESR process uses current to generate resistance heat through the electro-slag layer. This heat melts the electrode (base material) to achieve the following objectives:
- A special electroslag layer can achieve refining.
- Reduction of non-metallic inclusions and improved purity.
- A uniform and fine structure forms in the cross-section and length directions.
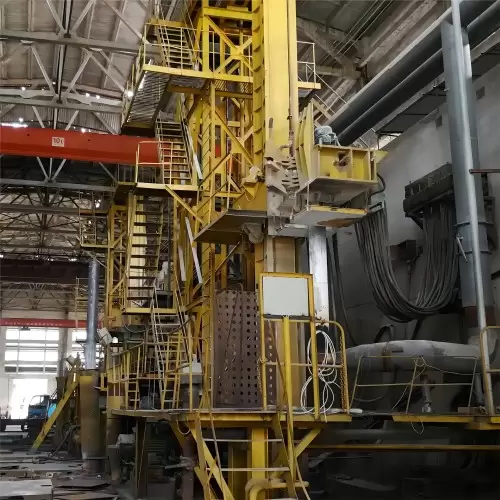
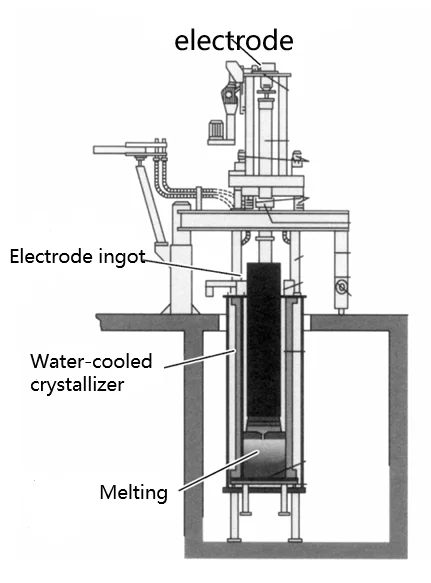
The process of electroslag remelting (ESR) and its core working principle can be simplified and summarized as follows:
- Establishing the circuit: Insert the consumable electrode into a copper water-cooled crystallizer that contains solid or liquid slag. Then, connect it to a transformer through a short network to form the power supply circuit. This circuit includes the consumable electrode, the molten slag, and the molten metal pool at the bottom.
- Resistance heating: Current passes through the transformer output and flows through the slag in the circuit. Because of the high resistance of the slag, most of the voltage from the transformer is dropped across the slag, resulting in a large amount of heat generation. The slag generates heat and transfers heat energy to the electrode (for melting), to the liquid metal leaving the electrode (for superheating), and to the ingot surface, helping to maintain the required temperature gradients in the solidifying ingot.
- Consumable Electrode: The molten slag is in a high-temperature molten state due to resistive heating, and its temperature is much higher than the melting point of the metal. This high temperature causes the end of the consumable electrode inserted into the slag to melt gradually.
- Metal droplet detachment: Molten metal gathers into droplets, detaching from the electrode tip under the force of gravity and passing through the slag into the molten metal pool below.
- Solidification through Cooling: Water-cooled crystallizers forcibly cool the molten metal pool, causing the liquid metal to solidify and form an ingot gradually.
Characteristics of ESR
Electroslag remelting of die steel belongs to the secondary refining method for die steel. The consumable electrode is the raw material sourced from die steel smelting methods like electric arc furnaces, induction furnaces, vacuum induction furnaces, and vacuum consumable furnaces. The purpose of electroslag remelting of die steel is to purify the steel and alloy further and improve the crystalline structure of the ingot based on primary smelting to obtain high-quality metal products.”
The main features (advantages) of electroslag remelting of mold steel:
- The melting, pouring, and solidification happen in a nearly pure environment, slashing contamination of the molten steel and cutting down pollution. Low-pressure conditions reduce the content of harmful gases such as oxygen and hydrogen, preventing metal oxidation or the absorption of harmful gases, thereby improving the quality of the castings. This has similarities with vacuum smelting, but the cost may be lower.
- Favorable Metallurgical Reaction Conditions:
- High Temperature: The slag pool temperature is typically above 1750℃ (3182℉) and can locally reach around 1900℃ (3452℉). The steel melt superheat can reach 450℃ (824℉). This high temperature accelerates the progress of metallurgical physical and chemical reactions.
- Sufficient Contact and Mixing: Full contact between the steel and slag, along with the stirring effect of electromagnetic forces, continuously renews the contact surfaces between the steel and slag, intensifying the metallurgical reactions and promoting the removal of harmful impurities and non-metallic inclusions. This translates to better desulfurization, deoxidation, and inclusion removal.
- Uniform and dense structure: Top-down sequential solidification ensures the remelted metal ingot’s uniform and dense crystalline structure. The top always has a liquid metal pool and a hot slag pool, which provides both heat preservation and sufficient liquid metal to fill the shrinkage cavities generated by solidification shrinkage. Gases and inclusions also easily float up, ultimately making the steel ingot structure dense and uniform and improving the material’s mechanical properties, such as strength, toughness, and fatigue performance.
- Smooth Surface and Pure Material: The transition from liquid to solid phase completes through forced cooling in a water-cooled crystallizer (copper crucible). A thin and uniform slag shell forms between the water-cooled crystallizer and the steel ingot, preventing contamination from oxidation and refractory materials. This ensures the remelted mold steel ingot’s smooth surface and material purity. This is crucial for molds with high surface quality requirements.
- Obtainable Large-Sized Castings: Electro-slag remelting consumable smelting can obtain large-sized and heavy metal castings, with the largest castings reaching 60-70 tons and diameters exceeding 2 meters, to meet the needs of large-scale industries such as large molds and aerospace components.
The significance of ESR
Electroslag remelting (ESR) is key in enhancing the quality of specialty steels and alloys. For mold steels, the improvements in microstructure and properties resulting from ESR are particularly significant, mainly reflected in the following aspects:
1. Improvement of macrostructure:
- Optimization of crystal structure: During ESR, the rapid solidification of the molten steel changes the crystal growth direction, significantly improving the macrostructure compared to conventionally cast ingots.
- Reduction of porosity and segregation: ESR significantly improves the macrostructure of the steel. Despite the same forging ratio, ESR improves central porosity and segregation by over 0.5 levels (according to ASTM standards) compared to ordinary cast mold steels. The central structure of ESR steel is dense, usually less than grade I. The effect is especially obvious for steels prone to porosity and shrinkage cavities in ingots, such as A2 tool steel. In producing plastic mold steel, improving structural uniformity and density significantly improves the steel’s polishing performance and corrosion resistance.
2. Reduction of non-metallic inclusion content in steel:
ESR significantly reduces the content of non-metallic inclusions in the steel, especially sulfide inclusions, which show significant changes and reductions in morphology and quantity. Silicate inclusions are also largely removed, thereby significantly improving the purity of the steel.
3. Improvement of carbide inhomogeneity:
ESR significantly improves the carbide inhomogeneity and the crystal structure of the steel ingot, especially for high-carbon, high-chromium cold work die steel. Under the same forging ratio, it improves by 0.5 levels, particularly enhancing the central structure. The refinement of carbides increases the alloy content in the matrix after quenching, thereby enhancing the secondary hardening effect and tempering resistance. In addition, ESR also improves the hot workability and toughness of the steel.
4. Improvement of mechanical properties:
ESR improves micro-segregation and inclusions in the steel ingot, creating a uniform and dense steel structure. This enhances the mechanical properties, particularly reducing performance differences between the steel’s longitudinal, transverse, central, and edge regions. For example, after ESR treatment of H13 tool steel, the ratio of longitudinal to transverse tensile strength and plasticity exceeds 0.90, while the impact toughness ratio exceeds 0.78.