Czym jest kucie na zimno? Kucie na zimno to metoda obróbki metali stosowana do produkcji elementów złącznych, takich jak śruby i wkręty. Ponieważ formy poddawane są dużemu ciśnieniu podczas procesu kucia na zimno, są podatne na problemy, takie jak: nosić, przyleganie, pękanie, a nawet zmęczenie materiału lub odkształcanie się form.

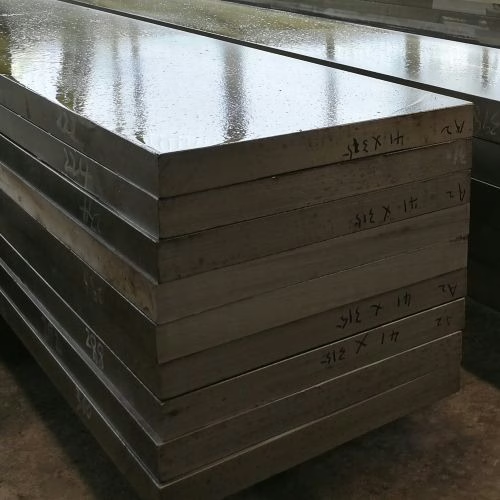
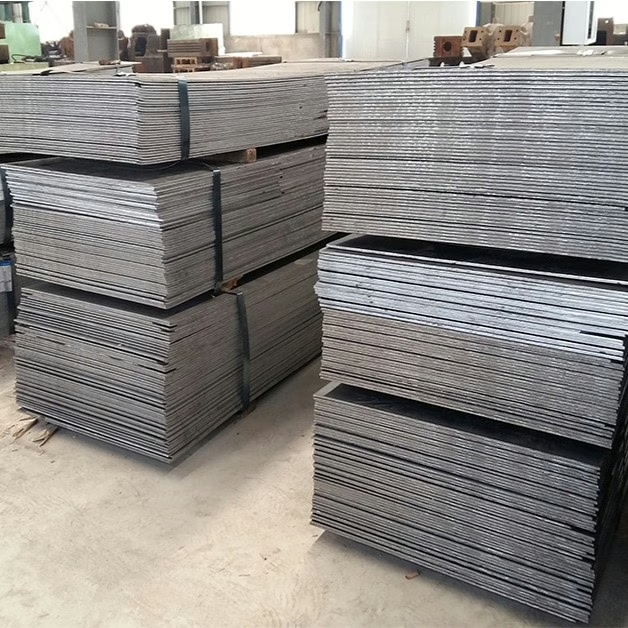
Dlaczego formy do kucia na zimno ulegają uszkodzeniu?
Formy do formowania na zimno w swojej pracy często napotykają na następujące wady:
- Zużycie: powierzchnia formy ulega zużyciu, co wpływa na jej trwałość użytkową.
- Przyczepność: Materiał metalowy przywiera do formy, co powoduje pogorszenie jakości obróbki.
- Pękanie: forma pęka, ponieważ nie wytrzymuje wysokiego ciśnienia.
- Zmęczenie: Uszkodzenia zmęczeniowe powstają wewnątrz formy lub na powierzchni roboczej po długim czasie użytkowania.
- Powiększanie kształtu: Kształt formy jest podparty, co negatywnie wpływa na precyzję.
Ze względu na wysokie ciśnienie w procesie kucia na zimno, powierzchnia robocza formy musi być bardzo twarda, zazwyczaj o twardości 62 HRC (jednostka twardości). Dlatego tak ważny jest dobór odpowiedniej stali.
Powszechnie stosowane stale: stale hartowane w wodzie W1 i W2
Jak wspomniano w artykule, najczęściej stosowanymi materiałami na matryce i stemple do kucia na zimno (stemple to narzędzia używane z matrycami) są stale hartowane w wodzie W1 i W2. Stale te charakteryzują się następującymi właściwościami:
- Płytkie hartowanie: Podczas hartowania (metody obróbki cieplnej, która hartuje stal) stale te utwardzają się tylko na powierzchni; wnętrze jest nadal stosunkowo miękkie.
- Kontrola hartowności jest ważna: Hartowność to głębokość, do której stal może się utwardzić po zahartowaniu. Hartowność powinna być dostosowana do rozmiaru formy.
Jednakże stale W1 i W2 mają wady:
- Ograniczona odporność na zużycie: nawet przy twardości 62-64 HRC nie są wystarczająco dobre. Jeśli forma ma być używana przez długi czas, ta stal może nie być wystarczająco trwała.
Wpływ wanadu: Czasami wanad (pierwiastek metaliczny) jest dodawany do stali, ale wanad może obniżyć hartowność. Aby rozwiązać ten problem, można dostosować inne pierwiastki w stali, aby zapewnić hartowność, drobniejsze ziarno stali i poprawić wytrzymałość (wytrzymałość to zdolność materiału do niełatwego łamania się).
Bardziej trwała opcja: stale wysokostopowe (D2, M2, A2)
Jeśli forma ma wytrzymać dłużej, wybierz stal wysokostopową, taką jak D2, M2 lub A2. Poniżej wymieniono zalety i wady tych stali:
- Zalety: dużo większa odporność na zużycie niż w przypadku W1 i W2, możliwość produkcji masowej.
- Wady: niska wytrzymałość (łatwe pękanie), nie można bezpośrednio wytwarzać całych form.
Rozwiązanie:
- Wykonaj z tych wysokostopowych stali wkładki (małe części formy), a następnie zamontuj je w powłoce wykonanej ze stali H11.
- Stal H11 jest wytrzymała, o twardości 48-50 HRC, co chroni wkładki i sprawia, że cała forma jest odporna na zużycie i mniej podatna na pęknięcia.
Dobór stali na matryce do kucia na zimno
Stempel jest narzędziem współpracującym z formą w procesie kucia na zimno, a wybór stali ma również duże znaczenie:
- Materiały powszechnie stosowane, takie jak formy i stemple, są zazwyczaj wykonane ze stali W1 lub W2.
- Gdy potrzebna jest wytrzymałość, jeśli stempel łatwo pęka lub odporność na zużycie nie jest tak ważna, można użyć stali odpornej na uderzenia S1. Ta stal jest wytrzymała i wytrzymuje uderzenia.
- Gdy potrzebna jest odporność na zużycie: Jeżeli stempel musi być bardziej odporny na zużycie, należy użyć stali D2 lub M2.
Podsumowując, kluczem do wyboru stali jest
Główną ideą tego artykułu jest to, że różne stale nadają się do różnych zastosowań. Wybór stali zależy od konkretnych potrzeb:
- Jeśli forma lub stempel wymaga twardego i taniego materiału, należy rozważyć W1 lub W2.
- Jeśli materiał ma być używany przez dłuższy czas i ma być odporny na zużycie, wybierz D2, M2 lub A2, ale z wytrzymałą obudową.
- Jeżeli dziurkacz jest podatny na pękanie, wybierz S1.