يُعد اختيار درجة الفولاذ المناسبة أمرًا بالغ الأهمية لأداء أدواتك وطول عمرها. أوبو ستيلبفضل خبرتنا الواسعة في تشكيل فولاذ الأدوات، نُرشد عملاءنا باستمرار إلى الاختلافات بين الدرجات الشائعة. الخياران الشائعان، خاصةً لتطبيقات القوالب والقوالب، هما P20 وH13. ورغم أن كلاهما يتميز بكفاءة عالية، إلا أنهما يتميزان بخصائص مميزة تناسب مختلف المهام. دعونا نلقي نظرة على أهم الاختلافات التقنية.
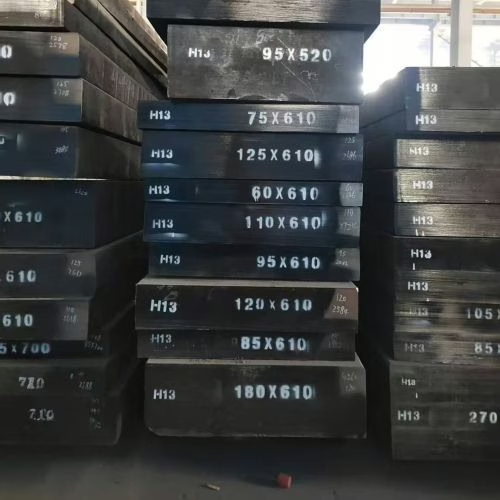
التصنيف والاستخدام الأساسي
- ص20: يُصنف هذا الفولاذ عادةً كفولاذ أدوات متوسط الكربون، ويُعرف أساسًا باسم فولاذ القوالب. يُعدّ هذا الفولاذ متعدد الاستخدامات في صب البلاستيك وبعض تطبيقات الصب بالقالب، وخاصةً الزنك.
- ح13: يقع هذا الصنف ضمن فئة الكروم 5% فولاذ أدوات العمل الساخنكما أنها معروفة بقدراتها العالية جدًا.
التركيب الكيميائي: أساس الأداء
الاختلافات الأساسية بين P20 و H13 تنبع من تركيبات السبائك الخاصة بهم:
- ص20: يحتوي عمومًا على 0.18-0.40% من الكربون (غالبًا حوالي 0.35%)، إلى جانب السيليكون والمنجنيز والكروم (0.5-2.00%)، والموليبدينوم (0.30-0.55%).
- ح13: بينما قد تتداخل مستويات الكربون (0.30-0.45%)، يتميز H13 بحزمة سبائك مختلفة تمامًا، وفقًا لمعايير مثل ASTM A681 أو JIS SKD61. يتميز بنسبة كروم أعلى بكثير (4.75-5.50%)، وموليبدينوم أعلى (1.10-1.75%)، بالإضافة إلى كمية مهمة من الفاناديوم (0.80-1.20%). يُسهم هذا المحتوى من الفاناديوم بشكل كبير في خصائص أدائه.
التطبيقات: أين تتفوق
- ص20: يُستخدم على نطاق واسع في قوالب حقن البلاستيك، وقوالب صب الزنك، وكتل الحامل. وهو خيار ممتاز لعمليات الإنتاج متوسطة الطول.
- ح13: نظرًا لكونه فولاذًا مُستخدمًا في العمل الساخن، يتميز H13 ببراعة عالية في البيئات ذات درجات الحرارة العالية التي تتضمن دورات حرارية. ويشمل ذلك قوالب الصب بالقالب (خاصةً للألمنيوم أو غيره من السبائك عالية درجة الانصهار)، وقوالب البثق الساخن، وقوالب التشكيل بالحرارة، بالإضافة إلى قوالب حقن البلاستيك عالية الأداء التي تتطلب صلابة أعلى أو تحكمًا حراريًا أفضل من P20.
المعالجة والصلابة
كيف يتم توريد هذه الفولاذات و المعالجة حرارياً هناك فرق عملي كبير:
- ص20: من أهم مزاياه أن مادة P20 تُورَّد عادةً مُصلَّبة مسبقًا، بصلابة تتراوح بين 28 و32 HRC (أي ما يعادل 300 HB تقريبًا). يتيح هذا لصانعي القوالب تشكيل التجاويف مباشرةً واستخدام الأداة دون الحاجة إلى معالجة حرارية عالية، مما يُقلل من مخاطر التشوه. للحصول على صلابة سطحية أعلى و يرتدي في قوالب البلاستيك، يمكن معالجة P20 بالكربنة بعد التشغيل. عادةً ما يتم تبريده بالزيت.
- ح13: على الرغم من استخدام H13 مُصلَّدًا مسبقًا في بعض الأحيان، إلا أنه غالبًا ما يُعالَج حراريًا من قِبل المستخدم لتحقيق مستويات صلابة أعلى (مثل 45-54 HRC أو أعلى لتطبيقات محددة) وقوة تحمل تتجاوز 2070 ميجا باسكال (300 كيلو باسكال). H13 هو فولاذ مُصلَّد بالهواء، مما يعني أنه يمكن أن يصلب عبر مقاطع كبيرة بأقل تشوه أثناء عملية التبريد. وهو أيضًا فولاذ مُصلَّد ثانويًا، يحافظ على صلابته ومتانته العالية في درجات حرارة التشغيل المرتفعة، والمعروفة باسم "صلابة حمراء"يُنصح عادةً بالتلطيف المزدوج."
خصائص الأداء الرئيسية
دعونا نقارنهم وجهاً لوجه على الخصائص الحرجة:
- مقاومة التآكل: يوفر H13 بشكل عام مقاومة فائقة للتآكل والتآكل بسبب محتواه العالي من الفاناديوم، والذي يشكل الكربيدات الصلبة. يتميز P20 بمقاومة جيدة للتآكل، مما يجعله مناسبًا للعديد من القوالب، بينما يُعد H13 أكثر ملاءمةً للظروف الكاشطة أو التشغيلات الطويلة. يُحسّن التكرير (الكربون) من تآكل سطح P20 بشكل ملحوظ.
- صلابة: يُعتبر كلا الفولاذين متينين. يتميز الفولاذ H13 عمومًا بقوة تحمل ممتازة للصدمات و صلابة، وهي ضرورية لمقاومة التشقق في التطبيقات الصعبة. كما يوفر P20 صلابة جيدة.
- مقاومة التصلب (الصلابة الحمراء): هذا يُميزه بشكل كبير. يتميز H13 بمقاومة ممتازة للتليين في درجات الحرارة العالية، مما يجعله مثاليًا للاستخدام في تطبيقات العمل الساخن. أما P20، فمقاومة التليين فيه أقل.
- الاستقرار الأبعادي: تُنتج طبيعة التصلب الهوائي لفولاذ H13 تشوهات ضئيلة للغاية أثناء المعالجة الحرارية. يُوفر فولاذ P20 (التصلب بالزيت) ثباتًا أفضل من فولاذ التصلب المائي، ولكنه أقل ثباتًا بشكل عام من فولاذ H13.
- قابلية التصنيع: تشتهر P20 بجودتها الممتازة قابلية التصنيع في حالة التصلب المسبق. كما يتمتع H13 بسهولة التشغيل عند معالجته بشكل صحيح.
- قابلية التلميع: يمكن لكلٍّ من P20 وH13 تحقيق سطح مصقول بجودة عالية، وهو أمرٌ أساسيٌّ لقوالب البلاستيك عالية الجودة. عادةً ما يُلمّع H13 جيدًا عند مستويات صلابة أعلى (أكثر من 50 HRC).
- مقاومة فحص الحرارة: يُعدّ H13 ضروريًا للصب بالقالب، إذ يُوفّر مقاومة جيدة للتشقق الناتج عن التعب الحراري، المعروف باسم "الفحص الحراري". يُعدّ P20 مناسبًا للصب بالقالب في درجات حرارة منخفضة، مثل الزنك، ولكن يُفضّل H13 للأعمال الساخنة الأكثر تطلبًا.
- الجودة الداخلية: بالنسبة للأدوات الكبيرة أو الحساسة، تُعدّ النظافة الداخلية للفولاذ أمرًا بالغ الأهمية. غالبًا ما يُنتَج H13 باستخدام إعادة الصهر بالكهرباء الخبثية (ESR) أو عمليات مماثلة، مما يُعطي نظافةً وتجانسًا أعلى مقارنةً بالفولاذ المُذاب بالطريقة التقليدية. يُحسّن هذا الأداء، وخاصةً مقاومة التعب الحراري.
اتخاذ الاختيار
- اختر P20 إذا: أنت بحاجة إلى فولاذ اقتصادي وسهل التشكيل، يُستخدم في قوالب البلاستيك أو الصب بالقالب في درجات حرارة منخفضة، ويُورَّد مُصلَّى مسبقًا لسهولة الاستخدام، ومناسب للاستخدامات المتوسطة. يُعدّ التكرير خيارًا لتعزيز مقاومة السطح للتآكل.
- اختر H13 إذا: يتطلب تطبيقك درجات حرارة تشغيل عالية، ومقاومة فائقة للتآكل، وصلابة حمراء عالية، وثباتًا أبعاديًا فائقًا أثناء المعالجة الحرارية، ومقاومةً للاختبار الحراري، أو مستويات صلابة عالية (أعلى من 50 HRC) للقوالب المتطلبة أو أدوات العمل الساخن. يوفر محتواه العالي من السبائك (الكروم، الموليبدينوم، والخماسي) أداءً فائقًا في هذه الظروف، مما يبرر غالبًا استخدام مواد أنظف. معدل ترسيب كرات الدم الحمراء/درجات VAR للتطبيقات الحرجة.
يساعدك فهم هذه الاختلافات على اختيار فولاذ الأدوات الأمثل لاحتياجاتك الخاصة. إذا كانت لديك أي أسئلة أو كنت ترغب في الحصول على درجات محددة، مثل P20 أو H13، فلا تتردد في التواصل معنا عبر البريد الإلكتروني sales@aobosteel.com. لدينا الخبرة الكافية لمساعدتك في اتخاذ القرار الصحيح.