ما هو الفرق الرئيسي بين ح13 و فولاذ الأدوات A2? خلاصة القول: H13 هو الخيار الأمثل لتطبيقات العمل الساخن حيث تعمل الأدوات في درجات حرارة عالية. أما A2، فهو مصمم لتطبيقات العمل البارد، ويتفوق في المهام التي تتطلب ثباتًا في الأبعاد ومقاومة جيدة للتآكل في درجات الحرارة المحيطة..
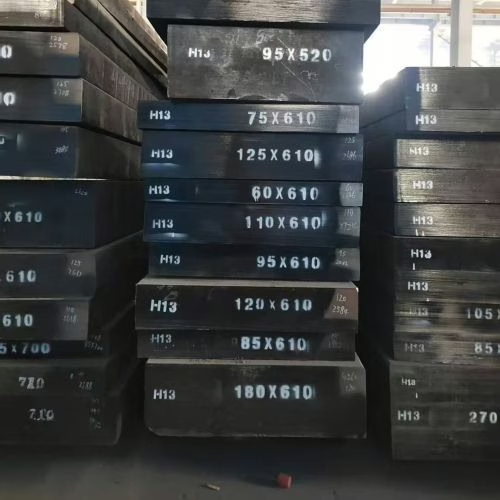
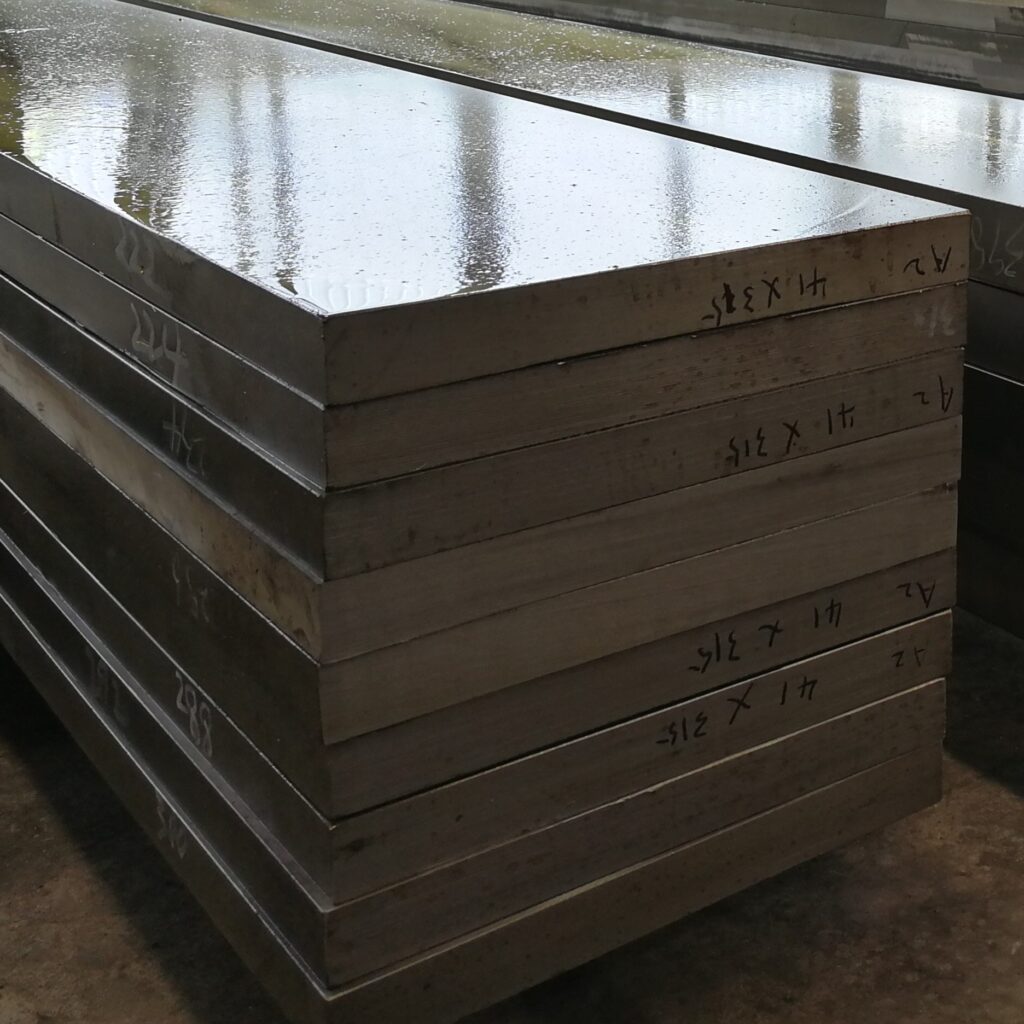
فهم الأساسيات: التصنيف والغرض
تُصنف فولاذات الأدوات بناءً على استخدامها المُراد وخصائصها. يحظى كلٌّ من H13 وA2 بتقدير كبير، لكنهما ينتميان إلى مجموعتين مختلفتين:
H13: أخصائي العمل الساخن
تم تصنيف H13 على أنه فولاذ أداة العمل الساخن، جزء من سلسلة "H" ضمن نظام المعهد الأمريكي للحديد والصلب (AISI). وهو فولاذ مصنوع من الكروم، مُصنَّع على الساخن. تتمحور فلسفة تصميمه حول الحفاظ على القوة ومقاومة التآكل والإجهاد الحراري عند ارتفاع درجة الحرارة - سواءً بالطرق أو الصب بالقالب أو البثق.
أ2: أداء العمل البارد
يقع A2 ضمن سلسلة "A"، مما يجعله صلابة هوائية، سبيكة متوسطة فولاذ الأدوات للعمل الباردكما يوحي الاسم، صُمم هذا المنتج للعمل في درجة حرارة الغرفة أو قريبة منها. بالنسبة لـ A2، تتمثل الأولويات في الحفاظ على شكله بدقة أثناء المعالجة الحرارية وتوفير مزيج جيد من يرتدي المقاومة والمتانة للمهام مثل الختم والتشكيل والقطع.
ماذا يوجد بالداخل؟ نظرة على التركيب الكيميائي
تنبع الخصائص المميزة لـ H13 وA2 من تركيبهما الكيميائي. ويتم اختيار عناصر السبائك بعناية لتحقيق خصائص أداء محددة.
أهم ما يميز H13
- الكربون (C): حول 0.35-0.45%يساهم هذا المستوى المعتدل من الكربون في متانته، وهو أمر حيوي لتطبيقات العمل الساخن التي غالبًا ما تنطوي على الصدمات.
- الكروم (Cr): عن 5%يعد الكروم عنصرًا أساسيًا للصلابة ومقاومة التآكل والقوة في درجات الحرارة العالية.
- الموليبدينوم (Mo): تقريبا 1.35-1.4%. يعزز الموليبدينوم القوة الساخنة والصلابة والقدرة على التصلب.
- الفاناديوم (V): حول 1%. يعتبر الفاناديوم ضروريًا لتشكيل الكربيدات الصلبة، مما يعزز مقاومة التآكل، وخاصة في درجات الحرارة المرتفعة، ويساعد في تحسين بنية الحبوب.
- السيليكون (Si): تقريبًا 1%. يعمل السيليكون على تحسين قوة تحمل درجات الحرارة العالية ومقاومة الأكسدة.
يمنح هذا التكوين، وخاصة التوازن بين الكروم والموليبدينوم والخامس، مادة H13 قدرتها على تحمل قسوة العمل الساخن.
أبرز ما في تكوين A2
- الكربون (C): حول 1.0%. يُعد هذا المحتوى العالي من الكربون مساهمًا أساسيًا في زيادة صلابة A2 ومقاومتها للتآكل في سيناريوهات العمل البارد.
- الكروم (Cr): أيضا حول 5%كما هو الحال في H13، يساعد الكروم على زيادة القدرة على التصلب ومقاومة التآكل.
- الموليبدينوم (Mo): عادة 1.0-1.1%يساهم الموليبدينوم في الصلابة والمتانة.
- الفاناديوم (V): كمية أصغر، عادة 0.2-0.25%على الرغم من أنها أقل من H13، إلا أنها لا تزال تلعب دورًا في مقاومة التآكل.
يتمتع A2 عمومًا بتوازن مختلف، وهو مناسب لتطبيقات العمل البارد.
إن نسبة الكربون العالية في A2 تشكل عامل تمييز مهم، مما يجعله أكثر صلابة وتحملاً للتآكل في التطبيقات الباردة.
المعالجة الحرارية: إطلاق العنان للأداء
تُحوّل المعالجة الحرارية هذه الفولاذ من حالتها اللينة القابلة للتشكيل إلى أدوات صلبة ومتينة. يتميز كلٌّ من H13 وA2 بخصائص معالجة حرارية سهلة الاستخدام.
التصلب وقابلية التصلب
كل من H13 و A2 هما الفولاذ المقسى بالهواءهذه ميزة كبيرة. هذا يعني أنه يمكن تقويتها بالتبريد في الهواء الساكن بعد تسخينها إلى درجة حرارتها القصوى. الأوستنيت درجة حرارة (التصلب). يُقلل التصلب الهوائي من الضغوط الداخلية التي قد تؤدي إلى التشوه أو التشقق، وهو أمر مفيد بشكل خاص لأشكال الأدوات المعقدة. يتمتع كلا الفولاذين أيضًا بخصائص جيدة قابلية التصلبوهذا يعني أنها يمكن أن تتصلب إلى عمق كبير، مما يجعلها مناسبة للأدوات الأكبر حجمًا.
التلطيف والاستقرار الأبعادي
بعد التصلب، يتم معالجة الفولاذ المستخدم في الأدوات لتخفيف الضغوط وتحقيق التوازن المطلوب بين الصلابة والمتانة.
- ح13 المعروضات التصلب الثانويهذا يعني أنه عند صقله عند درجات حرارة أعلى (عادةً حوالي 510 درجة مئوية أو 950 درجة فهرنهايت)، فإنه يكتسب صلابةً نتيجة ترسب كربيدات السبائك الدقيقة. هذه الخاصية حيوية لأداء العمل الساخن، حيث تساعد H13 على الاحتفاظ بصلابته حتى عند تعرضه لدرجات حرارة تشغيل عالية. وغالبًا ما يُصقل مرتين لضمان ثباته ومتانته.
- أ2 يُظهر أيضًا ذروة تصلب ثانوية، وإن كانت أقل وضوحًا من H13. ميزته الرئيسية أثناء المعالجة الحرارية هي استقرار أبعادي ممتازتتميز A2 بتغير الحجم الضئيل والتشوهات المنخفضة بعد التصلب والتخمير، وهو أمر بالغ الأهمية للأدوات الدقيقة.
معالجات السطح
لتحسين خصائص السطح، يتم استخدام معالجات مثل النترتة يمكن تطبيقها على كلٍّ من H13 وA2. تُكوّن النترتة طبقة سطحية صلبة للغاية، مما يُحسّن بشكل كبير من مقاومة التآكل، وفي بعض الحالات، من مقاومة التعب. يستفيد H13، على وجه الخصوص، بشكل كبير من النترتة في تطبيقات مثل قوالب الصب، حيث يواجه درجات حرارة عالية وتآكلًا كاشطًا.
الخصائص الميكانيكية الرئيسية: التفاصيل الدقيقة
دعونا نقارن بعض أهم الخصائص الميكانيكية لمستخدم الأداة:
صلابة
- أ2 يتم استخدامه عمومًا في مستويات صلابة العمل الأعلى، عادةً 56-61 قانون حقوق الإنسان (صلادة روكويل سي). هذه الصلابة العالية ناتجة مباشرةً عن محتواها العالي من الكربون، وهي مثالية لمقاومة التآكل في العمل البارد.
- ح13 يتم استخدامه عادة في مستويات صلابة العمل التي تتراوح من 42-54 قانون حقوق الإنسانحسب الاستخدام المحدد. على سبيل المثال، قد تتراوح صلابة أدوات الصب بالقالب بين 44 و48 HRC، بينما قد تكون التطبيقات التي تتطلب مقاومة أكبر للصدمات أكثر ليونة. صلابتها بعد التخمير أقل من صلابة A2.
الصلابة الساخنة (مقاومة التليين عند درجة الحرارة)
هذا هو ما يتفوق فيه H13 حقًا، والسبب الرئيسي لكونه فولاذًا للشغل الساخن. فهو يحتفظ بجزء كبير من صلابته حتى في درجات الحرارة المرتفعة (حتى حوالي 550 درجة مئوية أو 1020 درجة فهرنهايت، ويمكنه تحمل التعرضات القصيرة التي تصل إلى درجات حرارة أعلى). هذه "الصلابة الحمراء" تمنع الأداة من التليين والتشوه عند ملامستها لمواد قطع العمل الساخنة.
نظرًا لكون الفولاذ A2 قابلًا للتشكيل على البارد، فإنه لا يتمتع بصلابة جيدة عند التسخين. تنخفض قوته بسرعة عند درجات حرارة أعلى بكثير من 200-260 درجة مئوية (400-500 درجة فهرنهايت)، مما يجعله غير مناسب للتشكيل على الساخن.
الصلابة
الصلابة هي قدرة الفولاذ على امتصاص الطاقة ومقاومة الكسر، وخاصة تحت التأثير.
- ح13 العروض صلابة ممتازة وقوة تأثير، خاصةً لفولاذ العمل الساخن. يُعد هذا أمرًا بالغ الأهمية لتطبيقات مثل قوالب التشكيل التي تتعرض لأحمال صدمات متكررة. يساهم انخفاض نسبة الكربون فيه (مقارنةً بـ A2) بشكل كبير في هذا.
- أ2 يوفر صلابة جيدة للفولاذ المصنوع على البارد، مما يوفر توازنًا أفضل بين المتانة ومقاومة التآكل مقارنة ببعض الدرجات الأخرى المصنعة على البارد مثل سلسلة D. إنه أكثر صلابة من الفولاذ المقسى بالزيت ولكن بشكل عام ليس بنفس قوة الفولاذ المقاوم للصدمات (سلسلة S).
مقاومة التآكل
مقاومة التآكل هي القدرة على مقاومة التآكل وفقدان المواد بسبب الاحتكاك.
- أ2 العروض مقاومة جيدة إلى عالية للتآكل لتطبيقات العمل البارد. يُوفر محتواه العالي من الكربون والكربيدات الناتجة عنه هذه الخاصية. يقع عادةً بين فولاذ الأدوات من السلسلة S (مقاومة تآكل أقل) وسلسلة D (مقاومة تآكل أعلى).
- ح13 كما يوفر أيضا مقاومة جيدة للتآكل، خاصةً في درجات الحرارة المرتفعة. يساهم كربيد الفاناديوم في تركيبه في ذلك. عند النترتة، تزداد مقاومة H13 للتآكل بشكل ملحوظ. ومع ذلك، بالنسبة للتآكل البارد الكاشط البحت دون درجات حرارة عالية، عادةً ما يكون لـ A2 حافة.
قابلية التصنيع
في حالتها الملدنة (المخففة)، H13 يقدم بشكل عام أفضل قابلية التصنيع من A2. يمكن أن يكون هذا اعتبارًا عمليًا عند تصنيع الأدوات المعقدة.
التطبيقات النموذجية
يساعد فهم خصائصها على تفسير استخداماتها الشائعة:
تطبيقات H13
نظرًا لقوتها في درجات الحرارة العالية، فإن H13 هو الخيار الأمثل لـ:
- قوالب الصب للألمنيوم والزنك والمغنيسيوم
- قوالب وتشكيلات التشكيل الساخن
- أدوات البثق (القوالب، المغزل، البطانات) للألمنيوم والنحاس
- قوالب حقن البلاستيك، وخاصة للمواد البلاستيكية الهندسية الكاشطة أو عالية الحرارة
- شفرات القص الساخنة
- المغزل والنوى
تطبيقات A2
بفضل ثباتها الأبعادي الممتاز وتوازنها الجيد بين مقاومة التآكل والمتانة، تُستخدم A2 على نطاق واسع في:
- تقطيع وتشكيل القوالب
- قوالب سك النقود
- تشذيب القوالب
- سكاكين القص وسكاكين التقطيع
- اللكمات والمغزل لعمليات الإنتاج الطويلة
- المقاييس وأدوات القياس
- القوالب التي تتطلب دقة عالية
اتخاذ الاختيار الصحيح لمصنعك
لذا، عند الاختيار بين H13 وA2، فإن السؤال الأول الذي يجب طرحه هو: هل ستشهد الأداة حرارة كبيرة أثناء التشغيل؟
- إذا كانت الإجابة بنعم (عادةً أعلى من 200-250 درجة مئوية أو 400-480 درجة فهرنهايت)، فإن H13 هو الخيار الأفضل دائمًا تقريبًا. إن قدرتها على الاحتفاظ بالصلابة والقوة في درجات الحرارة المرتفعة ومتانتها الجيدة ومقاومتها للتعب الحراري (اختبار الحرارة) تجعلها مثالية للأعمال الساخنة.
- إذا كان التطبيق عبارة عن عمل بارد، فإن A2 هو منافس قوي. بفضل ثبات أبعادها الممتاز أثناء المعالجة الحرارية، تحافظ أدواتك على شكلها الدقيق. كما توفر مزيجًا ممتازًا من مقاومة التآكل والمتانة لمختلف عمليات الختم والتشكيل والقطع.
يُعدّ كلٌّ من H13 وA2 من فولاذ الأدوات الممتاز عند استخدامهما في السياق المناسب. سيساعدك فهم الاختلافات الجوهرية بينهما من حيث تحمل الحرارة، والصلابة، والمتانة، ومقاومة التآكل على اختيار المادة الأكثر فعاليةً وفعاليةً من حيث التكلفة لتلبية احتياجات مصنعك.
إذا كانت لديكم تطبيقات محددة أو تحتاجون إلى مزيد من التوجيه، فلا تترددوا في التواصل معنا. لدينا خبرة واسعة في مجال فولاذ الأدوات، ويمكننا مساعدتكم في اختيار الحل الأمثل.
اتخذ الخطوة التالية نحو حلول الفولاذ المتفوقة!
خبراؤنا المتمرسون في Aobo Steel على أتم الاستعداد لمساعدتك في اختيار فولاذ الأدوات المثالي لاحتياجاتك الخاصة. استفد من أسعارنا التنافسية، وخدماتنا المتميزة، ومعرفتنا الواسعة بالصناعة.
👇 املأ النموذج أدناه للتواصل مع فريق المبيعات لدينا اليوم! 👇
(ستجد نموذج الاتصال أسفل هذا القسم مباشرةً)