فولاذ الأدوات O1 مقابل D2: فولاذ الأدوات O1 و فولاذ الأدوات D2 كلاهما من فولاذ الأدوات المُستخدم على نطاق واسع في العمل البارد، لكنهما يتميزان بخصائص مميزة تجعلهما مناسبين لتطبيقات مختلفة. تُبرز المقارنة التفصيلية نقاط قوتهما ونقاط ضعفهما.
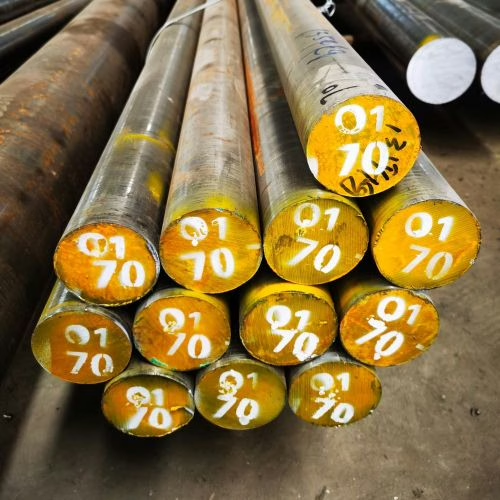

فولاذ الأدوات O1 مقابل D2: التركيب الكيميائي
العنصر | فولاذ الأدوات O1 (%) | تركيبة الفولاذ D2 (%) |
الكربون (C) | 0.85 – 1.00 | 1.40 – 1.60 |
الكروم (Cr) | 0.40 – 0.60 | 11.00 – 13.00 |
المنجنيز (Mn) | 1.00 – 1.40 | 0.10 – 0.60 |
الفاناديوم (V) | 0.15 – 0.30 | 0.50 – 1.10 |
الموليبدينوم (Mo) | – | 0.70 – 1.20 |
التنجستن (W) | 0.40 – 0.60 | – |
السيليكون (Si) | 0.10 – 0.50 | 0.10 – 0.60 |
الفوسفور (P) | ≤ 0.03 | ≤ 0.03 |
الكبريت (S) | ≤ 0.03 | ≤ 0.03 |
فولاذ الأدوات O1 مقابل D2: الخصائص الميكانيكية
- صلابة. يتمتع فولاذ O1 وفولاذ D2 بصلابة عمل متشابهة. صلابة الفولاذ O1 58–60 HRC. صلابة الفولاذ D2 تتراوح كثافتها بين 58 و61 HRC، ويمكن أن تصل إلى 60 و62 HRC بالمعالجة الحرارية، وحتى 63 و64 HRC عند إنتاجها باستخدام معالجة مسحوق المعادن (P/M). صلابة روكويل للفولاذ O1 أقل قليلاً من D2.
- قوةتبلغ مقاومة خضوع فولاذ O1 829 ميجا باسكال (758 ميجا باسكال UTS). وكانت مقاومة خضوعه للضغط أعلى من فولاذ D2. تبلغ مقاومة خضوع فولاذ D2 411 ميجا باسكال (350 ميجا باسكال UTS)، وقوة شده 758 ميجا باسكال.
- الصلابةبالمقارنة مع O1، يتمتع فولاذ D2 بمتانة أقل. وتُقلل الكمية الكبيرة من الكربيدات في فولاذ D2 من متانته.
- اللدونة/اللدونةيتميز فولاذ O1 بليونة أعلى من فولاذ D2. يُظهر O1 انكماشًا ملحوظًا قبل الكسر، مع انخفاض محسوب في المساحة يُقدر بحوالي 19.7%. أما D2، فلم يُظهر أي انكماش تقريبًا قبل الكسر، مع انخفاض في المساحة يُقدر بحوالي 1.3%.
- مقاومة التآكل/مقاومة التآكل. D2 لديه أفضل يرتدي مقاومة التآكل مقارنةً بفولاذ O1. يتميز فولاذ O1 بمقاومة تآكل متوسطة، بينما يتميز فولاذ D2 بمقاومة تآكل عالية جدًا. ويرجع ذلك إلى أن محتوى الكربون والكروم العالي في فولاذ D2 يُنتج كمية كبيرة من كربيدات M7C3 الغنية بالكروم.
- الاستقرار/التشويه البعديمقارنةً بأنواع فولاذ الأدوات الأخرى، يتمتع فولاذ D2 بأفضل ثبات أبعادي أثناء المعالجة الحرارية، مع أن فولاذ O1 يُظهر أيضًا تغيرات أبعادية طفيفة أثناء التبريد بالزيت. يُصلب فولاذ D2 بشكل أساسي بالهواء، مع تمدد أو انكماش يبلغ حوالي 0.0005 بوصة لكل بوصة.
- قابلية التصنيع/الطحنيتميز فولاذ O1 بسهولة تشغيل ممتازة، حيث يبلغ تصنيفه 90 مقارنةً بـ 100 لفولاذ الكربون 1%. أما فولاذ D2، فهو ضعيف بشكل خاص من حيث سهولة التشغيل، حيث يبلغ تصنيفه 45 مقارنةً بـ 100 لفولاذ الكربون 1%. ومن الواضح أن فولاذ O1 يتميز بسهولة تشغيل أفضل بكثير.
المعالجة الحرارية مقارنة
ميزة | المعالجة الحرارية للصلب O1 | معالجة حرارية للفولاذ D2 |
درجة حرارة التصلب/الأوستنيت | 802–816 درجة مئوية (1475–1500 درجة فهرنهايت) | 1010–1024 درجة مئوية (1850–1875 درجة فهرنهايت) |
وسط الإطفاء | تصلّب بالزيت. تصل إلى الصلابة الكاملة عند إخمادها بالزيت. | التصلب الهوائي أساسًا. قد يلزم تبريد الأجزاء الثقيلة بالزيت. |
التقسية | يتم تدفئتها عادة عند درجة حرارة 149–232 درجة مئوية (300–450 درجة فهرنهايت). | يتم معالجتها في درجات حرارة منخفضة، حوالي 200 درجة مئوية (392 درجة فهرنهايت)، لتحقيق صلابة عالية. |
إزالة الكربون والتكسير | يعاني من إزالة الكربون أثناء المعالجة الحرارية ويتعرض للتشقق بسبب الصدمة الحرارية أثناء إخماد الزيت. | يتميز D2 بمقاومة عالية للتشقق أثناء تشكيل وتصنيع المعادن. |
التطبيقات
O1 هو فولاذ أدوات متعدد الاستخدامات متعدد الأغراض يتم اختياره غالبًا للأدوات الصغيرة التي تتطلب قابلية تشغيل جيدة ومتانة وصلابة متوازنة. تطبيق فولاذ الأدوات D2 يتم تفضيله للقوالب طويلة المدى ويتطلب أقصى قدر من مقاومة التآكل والاستقرار الأبعادي.
احصل على عرض أسعار تنافسي لأدوات الفولاذ O1 وD2
بخبرة تزيد عن 20 عامًا في مجال التشكيل، تُعدّ Aobo Steel شريكك الموثوق في فولاذ الأدوات عالي الأداء O1 وD2. لا نوفر المواد فحسب، بل نوفر أيضًا الحلول. استفد من معرفتنا العميقة بالصناعة وسلسلة التوريد الموثوقة لنجاح مشروعك.
✉ تواصل معنا عن طريق ملء النموذج أدناه.