Elevate Your Tool and Die Making with M35 steel
Experience the Difference with Superior Hot Hardness and Wear Resistance
Aobo Steel: Professional M35 steel supplier
Aobo Steel supplies high-quality M35 steel for demanding tool and die manufacturers. As a high-speed tool steel, M35 offers excellent wear resistance, a balanced combination of toughness and hardness, and good machinability. Additionally, its cobalt content ensures outstanding hardness at high temperatures.
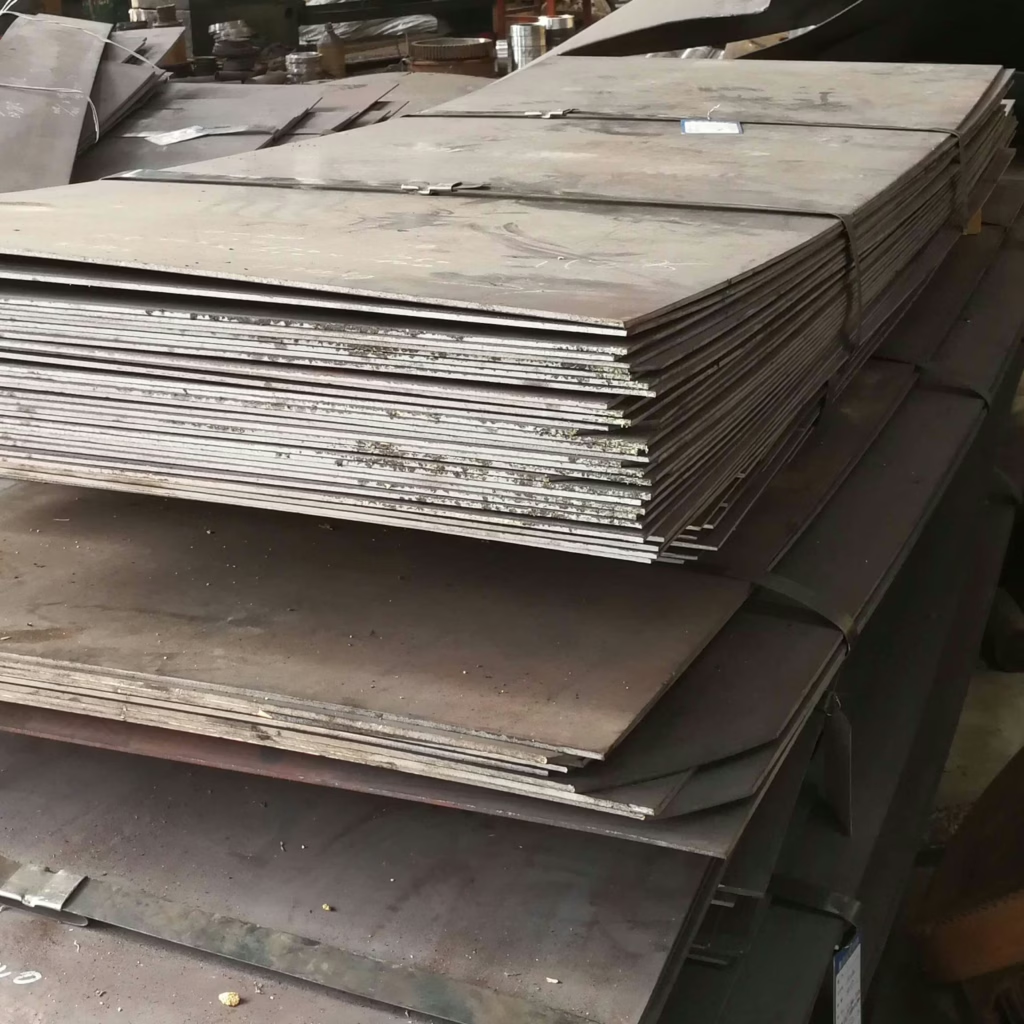
Applications
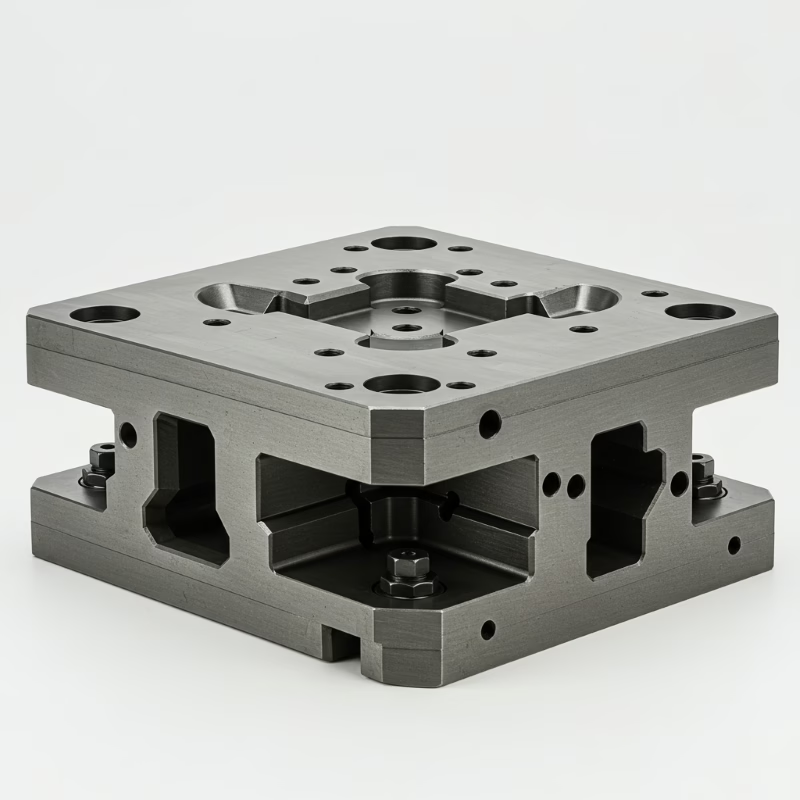
M35 steel can be used to manufacture various high-hardness and ultra-high-hardness saw blades, drills, taps, broaches, hobs, and various milling cutters.
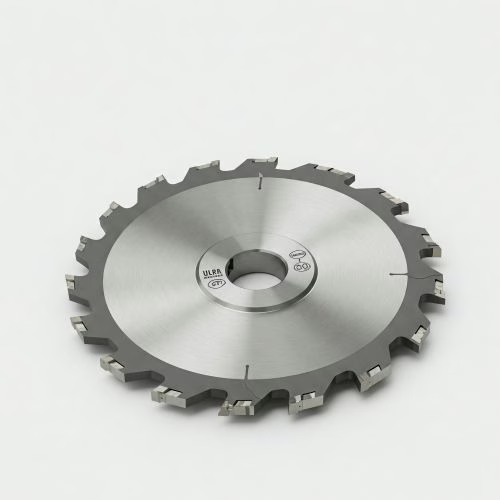
M35 is used for cold forging dies, deep drawing dies, cutting tools, etc.
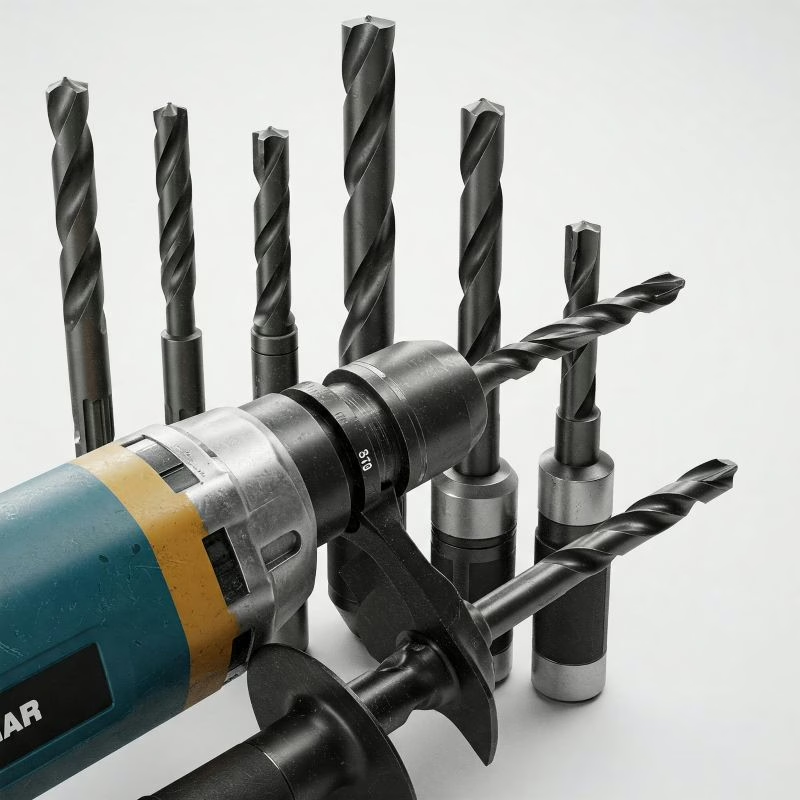
Recommended for use in cold stamping product industries such as watch case factories and screw factories.
Why Choose M35 Tool Steel?
Ideal for High-Speed Cutting:
Its red hardness ensures knives stay sharp during fast, demanding operations, minimizing downtime.
Ideal for Heavy-Duty Use:
High wear resistance and toughness make it perfect for drills, milling cutters, and rugged knives.
M35 steel overview
M35 steel composition
The M35 steel we provide fully meets the standard requirements. Due to its cobalt content, M35 steel has some special properties compared to other ordinary tool steels. Its composition table is as follows:
Element | Carbon | Chromium | Molybdenum | Tungsten | Vanadium | Cobalt | Manganese | Silicon |
Composition (%) | 0.80–0.90 | 3.75–4.50 | 4.50–5.50 | 5.50–6.75 | 1.75–2.20 | 4.50–5.50 | 0.20–0.45 | 0.20–0.45 |
Physical Properties
Density: Approximately 8.3-8.5 g/cm³
Melting Point: Approximately 1420-1450°C
Thermal Conductivity: Approximately 20-25 W/(m·K)
Thermal Expansion Coefficient: Approximately 11-13×10⁻⁶/°C
Elastic Modulus: Approximately 210-220 GPa
Mechanical Properties
m35 material hardness after heat treatment: HRC 65-67 (quenching + multiple tempering).
High-Temperature Hardness: At 600°C: Still maintains HRC 54-58 (cobalt improves red hardness).
Tensile Strength: Approximately 2000-2500 MPa
Toughness: Impact toughness is low (approximately 4-8 J/cm²),
Wear Resistance: Excellent, especially for high-speed cutting and processing of high-hardness materials (such as stainless steel and titanium alloys).
Compressive Strength: Approximately 3000-3500 MPa
Take the Next Step Today
Seamless performance, unmatched durability, and industry-leading results—M35 steel is your trusted partner in tooling excellence.
M35 steel equivalents DIN 1.3243 and JIS SKH55
M35 steel equivalent DIN 1.3243 and JIS SKH55 have similar compositions and properties in the German and Japanese steel systems.
Introduction to DIN 1.3243
1.3243 Chemical composition
Carbon (C) | Silicon (Si) | Manganese (Mn) | Phosphorus (P) | Sulfur (S) | Chromium (Cr) | Molybdenum (Mo) | Tungsten (W) | Vanadium (V) | Cobalt (Co) |
0.87 – 0.95 | ≤ 0.45 | ≤ 0.40 | ≤ 0.03 | ≤ 0.03 | 3.8 – 4.5 | 4.7 – 5.2 | 5.9 – 6.7 | 1.7 – 2.1 | 4.5 – 5.0 |
1.3243 steel Properties
Property | Value |
---|---|
Density | 8.12 g/cm³ |
Hardness (HRC) | 60 – 64 |
Modulus of Elasticity | 210 GPa |
Thermal Conductivity | 20.0 W/m·K |
Specific Heat Capacity | 420 J/kg·K |
Coefficient of Thermal Expansion | 11.0 × 10⁻⁶ /K (20 – 100°C) |
Introduction to DIN 1.3243
SKH55 Chemical composition
C | Si | Mn | Cr | Mo | W | V | Co |
0.85 ~ 0.95 | ≤ 0.40 | ≤ 0.40 | 3.8 ~ 4.5 | 4.6 ~ 5.5 | 5.7 ~ 6.7 | 1.7 ~ 2.2 | 4.5 ~ 5.5 |
SKH55 steel Properties
Property | Value |
---|---|
Density | 8.12 g/cm³ |
Hardness (HRC) | 60 – 66 |
Modulus of Elasticity | 210 GPa |
Thermal Conductivity | 20.0 W/m·K |
Specific Heat Capacity | 420 J/kg·K |
Coefficient of Thermal Expansion | 10.5 × 10⁻⁶ /K (20 – 100°C) |