Definition of tool steel
In terms of use, tool steel is the steel used to make various tools such as cutting tools, molds, and gauges. Among the various types of steel materials, tool steel was the first to be developed and utilized. In the early 1900s, most of the major tool steels were produced.
Production-wise, compared to ordinary carbon steel, tool steel meets two conditions: alloy steel mixed in and a heat-treating process before use.
Designation of tool steels
Tool steels are designated according to different systems worldwide, making precise definitions and comparisons difficult. The ASTM standard, widely used in the U.S., assigns a letter and a number to denote specific grades, reflecting properties or applications.
Type | Symbol | Example Grades |
Water-hardening | W | W1 |
Shock resistant | S | S7 |
Oil-hardening cold work | O | O1, O2 |
Air-hardening cold work | A | A2 |
High-carbon/chromium dies | D | D2, D3 |
Plastic molds | P | P20 |
Hot work (chromium/tungsten) | H | H11, H13 |
Tungsten high-speed | T | T1,T2 |
Molybdenum high-speed | M | M2 |
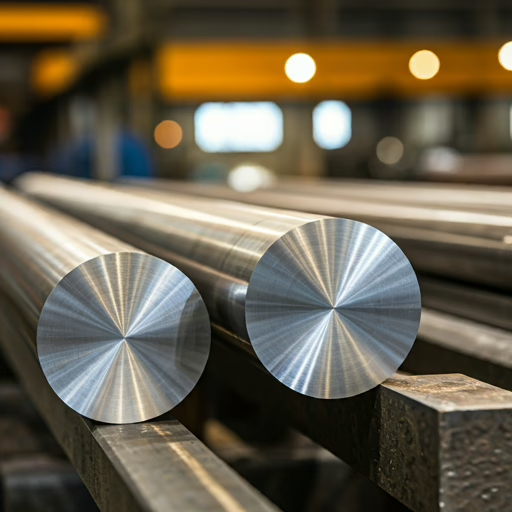
Classification of tool steels
There are 4 common classifications, cold work tool steel, hot work tool steel, plastic mold steel and high speed steel. We introduce one by one.
- Cold work tool steel is used in shaping metal at room temperature, making molds like stamping, drawing, heading, extrusion, embossing, and roller dies. It’s categorized into three types. They are low alloy cold work tool steel (e.g., AISI 01 steel), medium alloy cold work tool steel (e.g., A2 steel) and High alloy cold work tool steel (e.g., D2 steel. This steel is also often categorized as a high-carbon, high-chromium tool steel. Its carbon content is 1.4%~1.6%)
- 2. Hot work tool steel is used for metal molds at high temperatures, such as hot forging, extrusion, die casting, and shearing. These steels typically have alloying elements like tungsten, molybdenum, chromium, and vanadium, which can boost the molds’ high-temperature performance. In China, the typical hot work H13 is widely used in Aluminum alloy factories for building materials. We divide hot work tool steel into three types based on alloy content and use. They are low alloy hot work die steel (e.g., 5CrNiMo, 5CrMnMo), medium alloy hot work die steel (e.g., H13, H11, H12, H10), and High alloy hot work die steel (e.g., H21)
- High-speed steel is used in the manufacture of cutting tools. When using this metal in cutting, it can keep its hardness and sharpness during high speed and high temperatures, so we call it high-speed steel. The reason is that adding tungsten, chromium, molybdenum, cobalt, vanadium, and other alloy steels gives it excellent wear resistance and red-hardness at high temperatures.
- Plastic mold steel is the material used to create molds for making plastic products. Since different plastic products need different types of molds, plastic mold steel comes in many specialized varieties. Here are the common types:
- Carbon structural steel: Basic and used for simple molds.
- Carburized steel: Treated to make the surface harder.
- Pre-hardened steel (e.g., P20, P20+Ni): Hardened ahead of time for easier machining.
- Age-hardening steel: Gets stronger over time.
- Corrosion-resistant steel: Resists corrosion, ideal for special plastics.
- Free-cutting steel (e.g., P20+S): Easy to process.
- Martensitic steel: Offers both good toughness and strength.
- Mirror-polished steel: Provides a super-smooth surface for high-quality molds.
Easy Guide to Selecting Mold Steel
Here’s a simplified and reorganized guide to choosing mold steel. It focuses on its performance in use and its ease of processing during manufacturing.
Use Performance (How the Mold Works)
This section covers how well the mold holds up under working conditions.
- Strength
- Hardness: Molds need to be hard to resist deformation. Cold work die steel typically has a hardness of about 60HRC, while hot work die steel ranges from 40-55HRC. Even with the same hardness, different steel compositions can perform differently.
- Red Hardness: For hot work molds, hardness must hold up at high temperatures. Ordinary carbon steel can handle 180-250°C, while chrome-molybdenum steel withstands 550-600°C.
- Compressive and Flexural Strength: Molds must endure pressure and bending. Strength tests reflect real-world use better than hardness alone.
- Toughness
- Molds should resist impacts without cracking or chipping. Toughness depends on steel composition, purity, grain size, and heat treatment. It’s a trade-off between toughness, strength, and wear resistance.
- Wear Resistance
- Molds need to withstand friction and wear. High hardness and well-distributed carbides reduce wear from mechanical action, oxidation, or melting.
- Heat Fatigue Resistance
- Hot work molds must handle high temperatures and repeated heating-cooling cycles without cracking. Key factors include thermal fatigue life (time before cracks form), crack growth rate, and fracture toughness (resistance to crack spreading).
- Bite Resistance
- Molds should avoid sticking or “tack welding” to the workpiece. Better resistance is measured through friction tests.
Process Performance (How Easy It Is to Make the Mold)
This section focuses on how workable the steel is during manufacturing.
- Machinability
- Hot Working: Steel should shape easily at high temperatures.
- Cold Working: Includes cutting, grinding, and polishing. Mold steel is hard and tough to process, but adding elements like sulfur or lead can improve machinability.
- Quenchability and Hardenability
- Quenchability: Steel should harden evenly, especially for large molds. This depends on its composition.
- Hardenability: Hardness relies mainly on carbon content, which is critical for cold work molds.
- Quenching Temperature and Heat Treatment Deformation
- A wide quenching temperature range simplifies production. Molds, especially precision ones, should deform minimally during heat treatment.
- Oxidation and Decarburization Sensitivity
- Heating can cause oxidation or carbon loss, lowering hardness and wear resistance. Steel is sensitive to this, and needs special treatment, like vacuum processing.
Tool steel applications
According to the application, we have categorized the TOOL STEEL offered by our company.
Category | Steel Grade | Main Application Areas | Specific Usage Examples |
Cold Work Tool Steel | D2 | Cold Work Dies and Tools | Stamping Dies, Forming Dies, Cutting Tools, Cold Extrusion Dies, Hand tools |
D3 | Cold Work Dies and Tools | Stamping Dies, Forming Dies, Cutting Tools, Cold Extrusion Dies,Hand tools | |
A2 | Cold Work Dies and Cutting Tools | Punches, Stamping Dies, Forming Dies, Woodworking Cutting Tools | |
O1 | General Purpose Cold Work Tools and Dies | General Purpose Cutting Tools, Stamping Dies, Cutting Tools, Springs | |
O2 | General Purpose Cold Work Tools and Dies | General Purpose Cutting Tools, Stamping Dies, Cutting Tools, Springs | |
Shock Resisting Tool Steel | S7 | High Impact Cold Work Tools | Punches, Shears, Short Run Dies, Stamping Dies |
Hot Work Tool Steel | H11 | High Temperature Processing Dies and Tools | Hot Forging Dies, Die Casting Dies, Hot Cutting Tools, Extrusion Tools |
H13 | High Temperature Processing Dies and Tools | Hot Forging Dies, Die Casting Dies, Hot Cutting Tools, Extrusion Tools | |
High Speed Tool Steel | M2 | High Speed Cutting Tools | Drill Bits, Milling Cutters, Saw Blades, Tapping Tools, Broaches |
M35 | High Speed Cutting Tools (Cobalt-containing, Higher Red Hardness) | Drill Bits, Milling Cutters, Saw Blades, Tapping Tools, Broaches | |
M42 | High Speed Cutting Tools (Cobalt-containing, Higher Red Hardness) | Drill Bits, Milling Cutters, Saw Blades, Tapping Tools, Broaches | |
Mold Steel | P20 | Plastic Injection Molds | Plastic Injection Molds, Mold Bases, Die Casting Molds, Large Mold Frames |
P20+Ni | Plastic Injection Molds (Enhanced Corrosion Resistance) | Plastic Injection Molds, Mold Bases, Die Casting Molds, Large Mold Frames | |
P20+S | Plastic Injection Molds (Enhanced Machinability) | Plastic Injection Molds, Mold Bases, Die Casting Molds, Large Mold Frames |