Die steel, as a variety of materials to shape the “mother”, is indispensable in industrial production. They are not uniform, but according to the different working environment and needs, finely divided into three categories:
Cold work die steel: As the name suggests, this type of steel is mainly used in molds at room temperature or near room temperature. Imagine those precise stamping dies and cold extrusion molds; they must withstand enormous pressure and friction; therefore, cold work die steel must have very high hardness and wear resistance to be competent.
Hot work die steel: This type of steel has to withstand high temperatures. Hot forging molds, die casting molds, etc., work at high temperatures and must withstand repeated thermal shock. Therefore, hot work die steel has to withstand high temperatures and have enough strength and resistance to thermal fatigue to ensure the mold’s life and stability.
Plastic mold steel: This type of steel is closely related to our daily lives. A variety of plastic products are molded in plastic molds, which are inseparable from the plastic mold. Injection molds, extrusion molds, etc., need to ensure the surface finish and dimensional accuracy of plastic products. Therefore, the plastic mold steel polish, corrosion resistance, and dimensional stability are critical.
Through the classification of die steel, we can directly find the material we want.
1. Cold Work Die Steel
Cold work die steel is used in making dies that operate at room temperature, accounting for 30% to 40% of the total mold output value. Common applications include:
- Cold stamping dies
- Drawing dies
- Cold heading dies
- Cold extrusion dies
- Thread rolling dies

These dies require materials with high wear resistance to withstand the friction and abrasion encountered when shaping metals at ambient temperatures. Key materials include high-carbon hypereutectoid steel, ledeburite steel, carbon tool steel, low-alloy oil-quenched die steel, and high-speed steel. The high carbon content, typically ranging from 1.0% to 2.0%, as seen in grades like D2 and D3, enhances hardness and wear resistance, making these steels ideal for demanding applications like drawing dies and thread rolling dies. Additionally, alloy steels such as carbon-chromium steels (e.g., D2) are widely used for their ability to maintain a sharp cutting edge. Heat treatment processes, including air hardening, are essential to achieve an optimal balance of hardness and toughness, ensuring durability under repeated use.
2. Hot Work Die Steel
Hot work die steels are used for molds that shape metals at elevated temperatures. For example, forging dies, hot extrusion dies, and die casting dies. These steels are added alloy elements like tungsten, molybdenum, chromium, and vanadium. The alloy elements provide high temperature strength. This property is critical for maintaining mechanical integrity under thermal stress in processes like hot forging and die casting. For instance, H13, the most popular hot work die steel, is very suitable for extrusion dies and other high-heat applications.
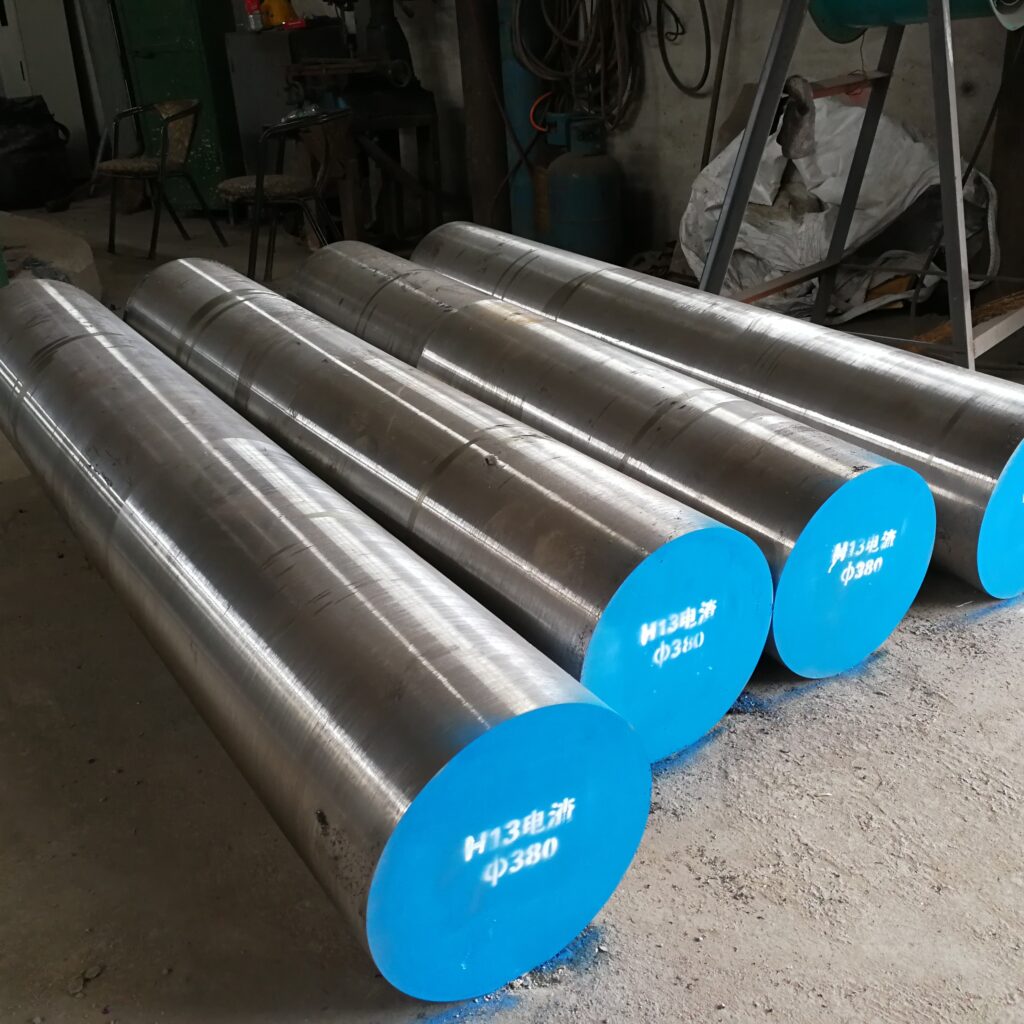
3. Plastic Mold Steel
The rapid expansion of the petrochemical industry has driven demand for plastic mold steels. Plastic mold steels are used to produce plastic products. These steels are tailored to meet specific needs, with types including:
Carbon structural steel
Carburized and pre-hardened mold steel
Corrosion-resistant steel
A key requirement for plastic mold steels is dimensional stability, which ensures molds retain their precise shapes over time, a critical factor for producing high-quality plastic parts with tight tolerances. For example, pre-hardened steel-P20 steel offers excellent polishability and machinability.
Conclusion
Understanding the classifications and properties of die steel is crucial for selecting the right material for specific applications. Feel free to contact us for more information about die steel.