في صناعة أدوات الفولاذ، معدل ترسيب كرات الدم الحمراء وسائل إعادة صهر الخبث الكهربائي.
لتحسين الجودة، تخضع بعض أنواع الفولاذ لعمليات إعادة صهر، مثل إعادة الصهر بالقوس الفراغي (VAR) وإعادة الصهر بالخبث الكهربائي (ESR). ومع ازدياد حجم القوالب وحاجتها إلى خصائص أكثر تخصصًا، ازداد استخدام الفولاذ المعاد صهره.
مقارنةً بتقنية التكرير الكهربائي المتغير (VAR)، تتميز تقنية ESR بمزايا عديدة. فهي أقل تكلفةً لعدم حاجتها إلى معدات تفريغ. كما تُحسّن عملية تنقية الخبث الكهربائي جودة سطح سبائك الفولاذ، مما يسمح حتى للسبائك ذات المقطع العرضي الكبير بتحقيق بنية موحدة.
على الرغم من وجود أساليب وتطبيقات تقنية متعددة لمعالجة خبث المعادن الكهربائي، إلا أن عملية إعادة تدوير المعادن بالكهرباء (ESR) تبقى تقنيتها الأساسية والرئيسية. ستقدم هذه المقالة شرحًا لعملية إعادة تدوير المعادن بالكهرباء وأهميتها. أوبوستيل يمكننا تزويد العملاء بأدوات الفولاذ المصنعة باستخدام عملية ESR.
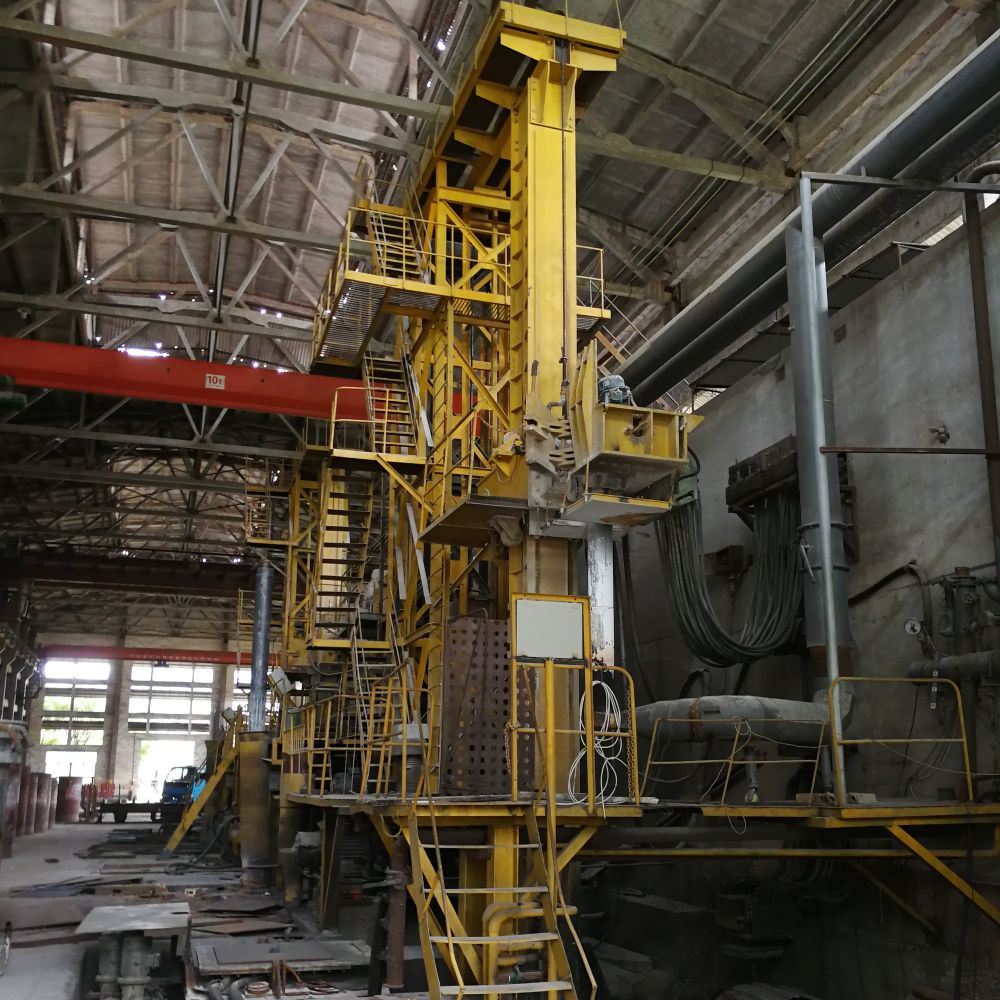

المبادئ الأساسية لعملية ESR
تستخدم عملية ESR التيار لتوليد حرارة مقاومة عبر طبقة الخبث الكهربائي. تُذيب هذه الحرارة القطب الكهربائي (المادة الأساسية) لتحقيق الأهداف التالية:
- يمكن تحقيق التكرير من خلال طبقة خاصة من الخبث الكهربائي.
- تقليل الشوائب غير المعدنية وتحسين النقاء.
- يتشكل هيكل موحد ودقيق في اتجاهي المقطع العرضي والطول.
يمكن تبسيط عملية إعادة صهر الخبث الكهربائي (ESR) ومبدأ عملها الأساسي وتلخيصها على النحو التالي:
- إنشاء الدائرة: أدخل القطب الكهربائي القابل للاستهلاك في مُبلور نحاسي مُبرد بالماء يحتوي على خبث صلب أو سائل. ثم وصّله بمُحوّل عبر شبكة قصيرة لتكوين دائرة التغذية. تتضمن هذه الدائرة القطب الكهربائي القابل للاستهلاك، والخبث المنصهر، وحوض المعدن المنصهر في الأسفل.
- التسخين بالمقاومة: يمر التيار عبر مخرج المحول ويتدفق عبر الخبث في الدائرة. ونظرًا لمقاومة الخبث العالية، ينخفض معظم جهد المحول عبر الخبث، مما يؤدي إلى توليد قدر كبير من الحرارة. يُولّد الخبث الحرارة وينقلها إلى القطب الكهربائي (للصهر)، وإلى المعدن السائل الخارج من القطب الكهربائي (للتسخين الفائق)، وإلى سطح السبيكة، مما يُساعد في الحفاظ على تدرجات الحرارة المطلوبة في السبيكة المتصلبة.
- القطب الاستهلاكي: بسبب التسخين المقاوم، يكون الخبث المنصهر في درجة حرارة عالية، أعلى بكثير من درجة انصهار المعدن. هذه الحرارة العالية تُسبب ذوبان طرف القطب الكهربائي القابل للاستهلاك المُدخل في الخبث تدريجيًا.
- انفصال القطرات المعدنية:تتجمع المعادن المنصهرة في قطرات، وتنفصل عن طرف القطب تحت قوة الجاذبية وتمر عبر الخبث إلى حوض المعدن المنصهر أدناه.
- التصلب عن طريق التبريد:تعمل أجهزة التبلور المبردة بالماء على تبريد حوض المعدن المنصهر بالقوة، مما يتسبب في تصلب المعدن السائل وتشكيل سبيكة تدريجيًا.
خصائص معدل ترسيب كرات الدم الحمراء
تُعدّ إعادة صهر الفولاذ المُشكّل بالكهرباء باستخدام الخبث إحدى طرق التكرير الثانوي للفولاذ المُشكّل. ويُعدّ القطب الكهربائي المُستهلك المادة الخام المُستخرَجة من طرق صهر الفولاذ المُشكّل بالكهرباء، مثل أفران القوس الكهربائي، وأفران الحث، وأفران الحث الفراغي، وأفران الاستهلاك الفراغي. وتهدف إعادة صهر الفولاذ المُشكّل بالكهرباء باستخدام الخبث إلى تنقية الفولاذ والسبائك بشكل أكبر، وتحسين البنية البلورية للسبيكة، وذلك بالاعتماد على الصهر الأولي، للحصول على منتجات معدنية عالية الجودة.
المميزات الرئيسية (المزايا) لإعادة صهر الفولاذ بالقالب باستخدام الخبث الكهربائي:
- يساهم الصب تحت الضغط المنخفض في تعزيز الجودة وتقليل التلوث. تتم عمليات الصهر والصب والتصلب في بيئة شبه نقية، مما يقلل من تلوث الفولاذ المنصهر. تقلل ظروف الضغط المنخفض من محتوى الغازات الضارة كالأكسجين والهيدروجين، مما يمنع أكسدة المعدن أو امتصاص الغازات الضارة، مما يحسن جودة المسبوكات. يشبه هذا الصهر التفريغ، ولكن تكلفته قد تكون أقل.
- الظروف الملائمة للتفاعل المعدني:
- درجة الحرارة العالية: عادةً ما تكون درجة حرارة حوض الخبث أعلى من ١٧٥٠ درجة مئوية (٣١٨٢ درجة فهرنهايت)، وقد تصل محليًا إلى حوالي ١٩٠٠ درجة مئوية (٣٤٥٢ درجة فهرنهايت). ويمكن أن تصل درجة حرارة صهر الفولاذ إلى ٤٥٠ درجة مئوية (٨٢٤ درجة فهرنهايت). تُسرّع هذه الحرارة العالية من وتيرة التفاعلات الفيزيائية والكيميائية المعدنية.
- الاتصال والاختلاط الكافيين: يُجدّد التلامس الكامل بين الفولاذ والخبث، إلى جانب تأثير تحريك القوى الكهرومغناطيسية، أسطح التلامس بينهما باستمرار، مما يُكثّف التفاعلات المعدنية ويُعزّز إزالة الشوائب الضارة والشوائب غير المعدنية. وهذا يُترجَم إلى تحسين إزالة الكبريت والأكسدة وإزالة الشوائب.
- بنية موحدة وكثيفةيضمن التصلب المتتالي من أعلى إلى أسفل بنية بلورية موحدة وكثيفة لسبيكة المعدن المعاد صهرها. يحتوي الجزء العلوي دائمًا على حوض معدني سائل وحوض خبث ساخن، مما يوفر الحفاظ على الحرارة وكمية كافية من المعدن السائل لملء تجاويف الانكماش الناتجة عن التصلب. كما تطفو الغازات والشوائب بسهولة، مما يجعل بنية سبيكة الفولاذ كثيفة وموحدة، ويحسن الخصائص الميكانيكية للمادة، مثل القوة والمتانة ومقاومة التعب.
- سطح أملس ومادة نقية:يكتمل التحول من الحالة السائلة إلى الحالة الصلبة من خلال التبريد القسري في مُبلور مُبرد بالماء (بوتقة نحاسية). تتشكل طبقة رقيقة وموحدة من الخبث بين المُبلور المُبرد بالماء وسبيكة الفولاذ، مما يمنع التلوث الناتج عن الأكسدة والمواد المقاومة للحرارة. وهذا يضمن سطحًا أملسًا لسبيكة الفولاذ المُعاد صهرها ونقاءً للمادة. وهذا أمر بالغ الأهمية للقوالب ذات متطلبات جودة سطح عالية.
- مسبوكات كبيرة الحجم يمكن الحصول عليها:يمكن الحصول على مصاهر المواد الاستهلاكية بإعادة صهر الخبث الكهربائي من خلال الحصول على مصبوبات معدنية كبيرة الحجم وثقيلة، حيث يصل أكبر المصبوبات إلى 60-70 طنًا وأقطار تتجاوز 2 متر، لتلبية احتياجات الصناعات واسعة النطاق مثل القوالب الكبيرة ومكونات الطيران.
أهمية معدل ترسيب كرات الدم الحمراء
إعادة الصهر بالخبث الكهربائي (ESR) أمرٌ أساسيٌّ لتحسين جودة الفولاذ والسبائك المتخصصة. بالنسبة لفولاذ القوالب، تُعدّ التحسينات في البنية الدقيقة والخصائص الناتجة عن إعادة الصهر بالخبث الكهربائي بالغة الأهمية، ويتجلى ذلك بشكل رئيسي في الجوانب التالية:
1. تحسين البنية الكلية:
- تحسين البنية البلورية: أثناء عملية التصلب الكهربي الصدمية، يؤدي التصلب السريع للفولاذ المنصهر إلى تغيير اتجاه نمو البلورات، مما يحسن بشكل كبير البنية الكلية مقارنة بالسبائك المصبوبة بالطريقة التقليدية.
- تقليل المسامية والانفصال: يُحسّن ESR البنية الكلية للفولاذ بشكل ملحوظ. على الرغم من تساوي نسبة التشكيل، يُحسّن ESR المسامية المركزية والانفصال بأكثر من 0.5 درجة (وفقًا لمعايير ASTM) مقارنةً بفولاذ الصب العادي. يتميز الهيكل المركزي لفولاذ ESR بكثافة، وعادةً ما تكون أقل من الدرجة الأولى. ويتضح هذا التأثير بشكل خاص في الفولاذ المعرض للمسامية وتجاويف الانكماش في السبائك، مثل فولاذ الأدوات A2في إنتاج فولاذ القالب البلاستيكي، يؤدي تحسين التوحيد الهيكلي والكثافة إلى تحسين أداء تلميع الفولاذ ومقاومته للتآكل بشكل كبير.
2. تقليل محتوى الشوائب غير المعدنية في الفولاذ:
يُقلل ESR بشكل ملحوظ من محتوى الشوائب غير المعدنية في الفولاذ، وخاصةً شوائب الكبريتيد، التي تُظهر تغيرات وانخفاضات ملحوظة في الشكل والكمية. كما يُزال بشكل كبير شوائب السيليكات، مما يُحسّن نقاء الفولاذ بشكل كبير.
3. تحسين عدم تجانس الكربيد:
يُحسّن ESR بشكل ملحوظ عدم تجانس الكربيد والبنية البلورية لسبيكة الفولاذ، خاصةً في فولاذ القوالب الباردة عالي الكربون والكروم. وبنفس نسبة التشكيل، يُحسّن بمقدار 0.5 درجة، مما يُحسّن بشكل خاص البنية المركزية. يزيد تحسين الكربيدات من محتوى السبائك في المصفوفة بعد الإخماد، مما يُعزز تأثير التصلب الثانوي ومقاومة التلطيف. بالإضافة إلى ذلك، يُحسّن ESR أيضًا قابلية التشكيل الساخن ومتانة الفولاذ.
4. تحسين الخواص الميكانيكية:
يُحسّن ESR الفصل الدقيق والشوائب في سبيكة الفولاذ، مما يُنتج بنية فولاذية متجانسة وكثيفة. يُحسّن هذا الخواص الميكانيكية، ويُقلل بشكل خاص فروق الأداء بين مناطق الفولاذ الطولية والعرضية والمركزية والحافة. على سبيل المثال، بعد معالجة ESR لـ فولاذ الأدوات H13، وتتجاوز نسبة قوة الشد الطولية إلى قوة الشد العرضية واللدونة 0.90، في حين تتجاوز نسبة صلابة التأثير 0.78.