ما هو التشكيل بالطرق على البارد؟ التشكيل بالطرق على البارد هو طريقة تشكيل معادن تُستخدم لصنع أدوات التثبيت مثل البراغي والمسامير. ولأن القوالب تتعرض لضغط كبير أثناء عملية التشكيل بالطرق على البارد، فإنها معرضة لمشاكل مثل: يرتدي، الالتصاق، والتشقق، وحتى التعب أو تشوه القوالب.

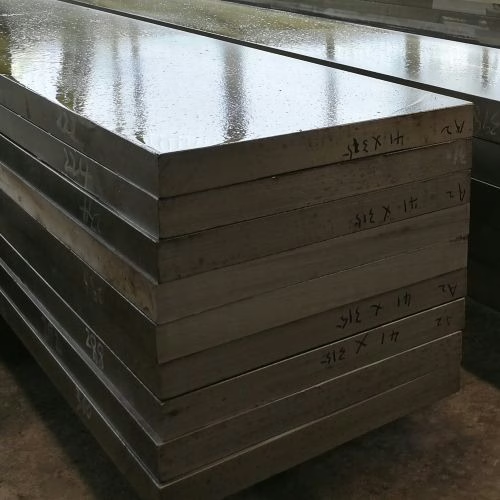
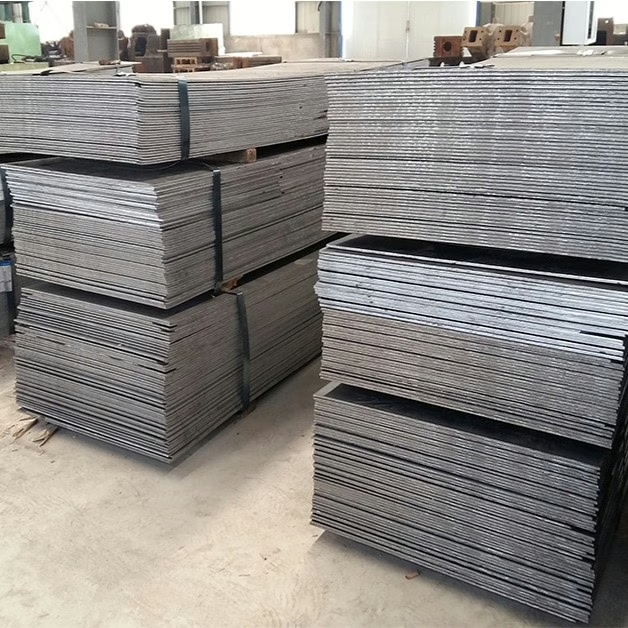
لماذا تفشل قوالب الرأس البارد؟
تواجه قوالب التشكيل البارد العديد من الأعطال الشائعة في عملها:
- التآكل والتلف: يتآكل سطح القالب، مما يؤثر على عمر الخدمة.
- الالتصاق: تلتصق المادة المعدنية بالقالب، مما يؤدي إلى معالجة سيئة.
- التشقق: يتشقق القالب لأنه لا يستطيع تحمل الضغط العالي.
- التعب: يحدث الضرر الناتج عن التعب داخل القالب أو على سطح العمل بعد فترة طويلة من الاستخدام.
- تكبير الشكل: يتم دعم شكل القالب، مما يقلل من الدقة.
بسبب الضغط العالي أثناء عملية التشكيل البارد، يجب أن يكون سطح عمل القالب صلبًا جدًا، وعادةً ما تكون صلابته 62 HRC (وحدة صلابة). لذلك، من المهم جدًا اختيار الفولاذ المناسب.
الفولاذ المستخدم بشكل شائع: الفولاذ المقسى بالماء W1 وW2
كما ذُكر في المقال، فإن أكثر المواد شيوعًا المستخدمة في قوالب التشكيل البارد والمثاقب (المثاقب هي الأدوات المستخدمة مع القوالب) هي الفولاذ المقسّى بالماء W1 وW2. يتميز هذان الفولاذان بالخصائص التالية:
- التصلب السطحي: تتصلب هذه الفولاذات على السطح فقط عند تبريدها (طريقة المعالجة الحرارية التي تصلب الفولاذ)، ولا يزال الجزء الداخلي ناعمًا نسبيًا.
- من المهم التحكم في قابلية التصلب: قابلية التصلب هي عمق تصلب الفولاذ عند التبريد. يجب ضبط قابلية التصلب بما يتناسب مع حجم القالب.
ومع ذلك، فإن الفولاذ W1 وW2 لهما عيوب:
- مقاومة تآكل محدودة: حتى مع صلابة تتراوح بين 62 و64 HRC، فهي ليست جيدة بما يكفي. إذا كان من المقرر استخدام القالب لفترة طويلة، فقد لا يكون هذا الفولاذ متينًا بما يكفي.
تأثير الفاناديوم: يُضاف الفاناديوم (عنصر معدني) أحيانًا إلى الفولاذ، إلا أنه قد يُقلل من قابليته للتصلب. ولحل هذه المشكلة، يُمكن تعديل عناصر أخرى في الفولاذ لضمان قابليته للتصلب، وجعل حبيبات الفولاذ أدق، وتحسين صلابته (الصلابة هي قدرة المادة على مقاومة الكسر بسهولة).
الخيار الأكثر متانة: الفولاذ عالي السبائك (D2، M2، A2)
عند الحاجة إلى إطالة عمر القالب، يُفضّل اختيار فولاذ عالي السبائك مثل D2 أو M2 أو A2. فيما يلي مزايا وعيوب هذه الفولاذ:
- المزايا: مقاومة للتآكل أعلى بكثير من W1 و W2، ومناسبة للإنتاج الضخم.
- العيوب: صلابة منخفضة (سهلة الكسر)، لا يمكن تصنيعها مباشرة في قوالب كاملة.
حل:
- قم بتحويل هذه الفولاذات عالية السبائك إلى أجزاء صغيرة من القالب ثم قم بتركيبها في غلاف مصنوع من الفولاذ H11.
- يعتبر الفولاذ H11 قويًا، بصلابة تتراوح بين 48-50 HRC، مما يحمي الإدخالات ويجعل القالب بأكمله مقاومًا للتآكل وأقل عرضة للكسر.
اختيار الفولاذ لقوالب التشكيل البارد
المثقب هو أداة تعمل مع القالب في عملية التشكيل على البارد، كما أن اختيار الفولاذ مهم جدًا أيضًا:
- المواد المستخدمة بشكل شائع، مثل القوالب واللكمات، تكون أيضًا مصنوعة عادةً من الفولاذ W1 أو W2.
- عند الحاجة إلى المتانة، أو إذا كان المثقب سهل الكسر، أو إذا لم تكن مقاومة التآكل مهمة جدًا، يمكن استخدام فولاذ S1 المقاوم للصدمات. يتميز هذا الفولاذ بمتانته وقدرته على تحمل الصدمات.
- عندما تكون هناك حاجة لمقاومة التآكل: إذا كانت اللكمة بحاجة إلى مزيد من مقاومة التآكل، استخدم الفولاذ D2 أو M2.
باختصار، مفتاح اختيار الفولاذ هو
الفكرة الأساسية لهذه المقالة هي أن أنواع الفولاذ المختلفة مناسبة لظروف مختلفة. ويعتمد اختيار الفولاذ على احتياجات محددة:
- إذا كان القالب أو المثقب يتطلب مادة صلبة ومنخفضة التكلفة، ففكر في W1 أو W2.
- إذا كان من الضروري استخدامه لفترة طويلة ولديه مقاومة عالية للتآكل، فاختر D2 أو M2 أو A2، ولكن مع غلاف قوي.
- إذا كانت اللكمة عرضة للكسر، اختر S1.