Trong ngành công nghiệp thép công cụ, ESR có nghĩa Nấu chảy lại xỉ điện.
Để cải thiện chất lượng, một số loại thép trải qua quá trình nấu chảy lại, chẳng hạn như nấu chảy lại bằng hồ quang chân không (VAR) và nấu chảy lại bằng điện xỉ (ESR). Khi khuôn trở nên lớn hơn và đòi hỏi nhiều tính năng chuyên biệt hơn, việc sử dụng thép nấu chảy lại ngày càng tăng.
So với VAR, ESR có một số ưu điểm. Nó rẻ hơn vì không cần thiết bị chân không. Ngoài ra, quy trình tinh luyện xỉ điện cải thiện chất lượng bề mặt của thỏi thép, cho phép ngay cả các thỏi thép có tiết diện lớn cũng đạt được cấu trúc đồng nhất.
Mặc dù có nhiều phương pháp và ứng dụng kỹ thuật khác nhau cho luyện kim điện xỉ, ESR vẫn là công nghệ cơ bản và cốt lõi của nó. Bài viết này sẽ giới thiệu quy trình ESR và ý nghĩa của nó. AoboThép có thể cung cấp cho khách hàng thép công cụ được sản xuất bằng quy trình ESR.
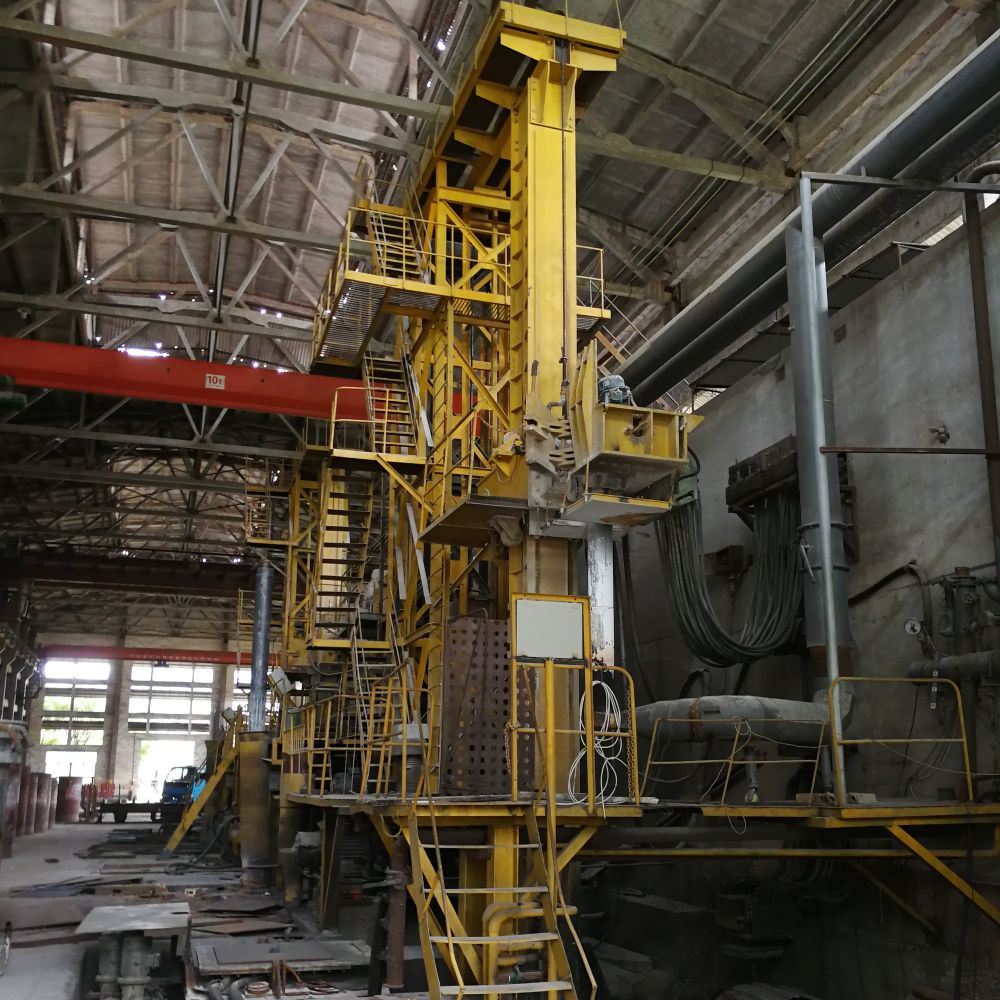

Nguyên tắc cơ bản của quy trình ESR
Quy trình ESR sử dụng dòng điện để tạo ra nhiệt điện trở qua lớp xỉ điện. Nhiệt này làm nóng chảy điện cực (vật liệu nền) để đạt được các mục tiêu sau:
- Một lớp xỉ điện đặc biệt có thể thực hiện quá trình tinh chế.
- Giảm tạp chất phi kim loại và cải thiện độ tinh khiết.
- Cấu trúc đồng nhất và mịn hình thành theo hướng cắt ngang và chiều dài.
Quá trình nấu chảy lại xỉ điện (ESR) và nguyên lý hoạt động cốt lõi của nó có thể được đơn giản hóa và tóm tắt như sau:
- Thiết lập mạch điện: Lắp điện cực tiêu hao vào máy kết tinh làm mát bằng nước bằng đồng có chứa xỉ rắn hoặc lỏng. Sau đó, kết nối nó với máy biến áp thông qua một mạng lưới ngắn để tạo thành mạch cung cấp điện. Mạch này bao gồm điện cực tiêu hao, xỉ nóng chảy và bể kim loại nóng chảy ở phía dưới.
- Sưởi ấm bằng điện trở: Dòng điện chạy qua đầu ra của máy biến áp và chảy qua xỉ trong mạch. Do xỉ có điện trở cao, hầu hết điện áp từ máy biến áp đều giảm qua xỉ, dẫn đến lượng nhiệt lớn được tạo ra. Xỉ tạo ra nhiệt và truyền năng lượng nhiệt đến điện cực (để làm nóng chảy), đến kim loại lỏng rời khỏi điện cực (để quá nhiệt) và đến bề mặt thỏi, giúp duy trì các gradient nhiệt độ cần thiết trong thỏi đông đặc.
- Điện cực tiêu hao: Do nhiệt điện trở, xỉ nóng chảy ở trạng thái nhiệt độ cao, cao hơn nhiều so với nhiệt độ nóng chảy của kim loại. Nhiệt độ cao này khiến đầu điện cực tiêu hao được đưa vào xỉ nóng chảy dần dần.
- Tách giọt kim loại:Kim loại nóng chảy tụ lại thành các giọt, tách khỏi đầu điện cực dưới tác dụng của trọng lực và đi qua xỉ vào vũng kim loại nóng chảy bên dưới.
- Sự đông đặc thông qua làm mát: Máy kết tinh làm mát bằng nước làm mát cưỡng bức hồ kim loại nóng chảy, khiến kim loại lỏng đông lại và dần dần hình thành thỏi.
Đặc điểm của ESR
Luyện lại thép khuôn bằng điện xỉ thuộc về phương pháp tinh luyện thứ cấp đối với thép khuôn. Điện cực tiêu hao là nguyên liệu thô có nguồn gốc từ các phương pháp luyện thép khuôn như lò hồ quang điện, lò cảm ứng, lò cảm ứng chân không và lò tiêu hao chân không. Mục đích của luyện lại thép khuôn bằng điện xỉ là để tinh chế thép và hợp kim hơn nữa và cải thiện cấu trúc tinh thể của thỏi dựa trên quá trình luyện sơ cấp để thu được các sản phẩm kim loại chất lượng cao.”
Các đặc điểm chính (ưu điểm) của phương pháp nấu chảy lại thép khuôn bằng điện xỉ:
- Đúc áp suất thấp giúp tăng chất lượng và giảm ô nhiễm. Quá trình nấu chảy, rót và đông đặc diễn ra trong môi trường gần như tinh khiết, cắt giảm ô nhiễm của thép nóng chảy và cắt giảm ô nhiễm. Điều kiện áp suất thấp làm giảm hàm lượng khí độc hại như oxy và hydro, ngăn ngừa quá trình oxy hóa kim loại hoặc hấp thụ khí độc hại, do đó cải thiện chất lượng của vật đúc. Điều này có điểm tương đồng với quá trình nấu chảy chân không, nhưng chi phí có thể thấp hơn.
- Điều kiện phản ứng luyện kim thuận lợi:
- Nhiệt độ cao: Nhiệt độ của hồ xỉ thường trên 1750℃ (3182℉) và có thể đạt tới khoảng 1900℃ (3452℉). Nhiệt độ nóng chảy thép có thể đạt tới 450℃ (824℉). Nhiệt độ cao này đẩy nhanh quá trình diễn ra các phản ứng vật lý và hóa học luyện kim.
- Tiếp xúc và trộn đủ: Tiếp xúc hoàn toàn giữa thép và xỉ, cùng với tác động khuấy của lực điện từ, liên tục làm mới bề mặt tiếp xúc giữa thép và xỉ, tăng cường các phản ứng luyện kim và thúc đẩy loại bỏ tạp chất có hại và tạp chất phi kim loại. Điều này chuyển thành quá trình khử lưu huỳnh, khử oxy và loại bỏ tạp chất tốt hơn.
- Cấu trúc đồng đều và dày đặc: Quá trình đông đặc tuần tự từ trên xuống đảm bảo cấu trúc tinh thể đồng nhất và đặc của thỏi kim loại nóng chảy lại. Phía trên luôn có một vũng kim loại lỏng và một vũng xỉ nóng, vừa giữ nhiệt vừa cung cấp đủ kim loại lỏng để lấp đầy các khoang co ngót do co ngót đông đặc tạo ra. Khí và tạp chất cũng dễ dàng nổi lên, cuối cùng làm cho cấu trúc thỏi thép đặc và đồng nhất, đồng thời cải thiện các tính chất cơ học của vật liệu, chẳng hạn như độ bền, độ dẻo dai và hiệu suất chịu mỏi.
- Bề mặt nhẵn và vật liệu tinh khiết: Quá trình chuyển đổi từ pha lỏng sang pha rắn hoàn tất thông qua quá trình làm mát cưỡng bức trong thiết bị kết tinh làm mát bằng nước (lò nung đồng). Một lớp xỉ mỏng và đồng nhất hình thành giữa thiết bị kết tinh làm mát bằng nước và thỏi thép, ngăn ngừa ô nhiễm từ quá trình oxy hóa và vật liệu chịu lửa. Điều này đảm bảo bề mặt nhẵn và độ tinh khiết của vật liệu của thỏi thép khuôn nấu chảy lại. Điều này rất quan trọng đối với các khuôn có yêu cầu chất lượng bề mặt cao.
- Có thể đạt được đúc kích thước lớn: Vật liệu tiêu hao nấu chảy xỉ điện phân có thể thu được các sản phẩm đúc kim loại nặng và có kích thước lớn, trong đó sản phẩm đúc lớn nhất có thể đạt tới 60-70 tấn và đường kính vượt quá 2 mét, đáp ứng nhu cầu của các ngành công nghiệp quy mô lớn như khuôn mẫu lớn và linh kiện hàng không vũ trụ.
Ý nghĩa của ESR
Quá trình nấu chảy lại bằng điện xỉ (ESR) đóng vai trò then chốt trong việc nâng cao chất lượng của thép và hợp kim đặc biệt. Đối với thép làm khuôn, những cải tiến về cấu trúc vi mô và tính chất thu được từ ESR đặc biệt đáng kể, chủ yếu thể hiện ở các khía cạnh sau:
1. Cải thiện cấu trúc vĩ mô:
- Tối ưu hóa cấu trúc tinh thể: Trong quá trình ESR, quá trình đông đặc nhanh chóng của thép nóng chảy sẽ thay đổi hướng phát triển của tinh thể, cải thiện đáng kể cấu trúc vĩ mô so với các thỏi đúc thông thường.
- Giảm độ xốp và sự phân tách: ESR cải thiện đáng kể cấu trúc vĩ mô của thép. Mặc dù có cùng tỷ lệ rèn, ESR cải thiện độ xốp và phân tách trung tâm hơn 0,5 cấp (theo tiêu chuẩn ASTM) so với thép đúc khuôn thông thường. Cấu trúc trung tâm của thép ESR rất đặc, thường ít hơn loại I. Hiệu ứng này đặc biệt rõ ràng đối với các loại thép dễ bị rỗng và co ngót trong các thỏi, chẳng hạn như Thép công cụ A2. Trong sản xuất thép khuôn nhựa, việc cải thiện tính đồng nhất về cấu trúc và mật độ sẽ cải thiện đáng kể hiệu suất đánh bóng và khả năng chống ăn mòn của thép.
2. Giảm hàm lượng tạp chất phi kim loại trong thép:
ESR làm giảm đáng kể hàm lượng tạp chất phi kim loại trong thép, đặc biệt là tạp chất sunfua, cho thấy sự thay đổi và giảm đáng kể về hình thái và số lượng. Tạp chất silicat cũng được loại bỏ phần lớn, do đó cải thiện đáng kể độ tinh khiết của thép.
3. Cải thiện tính không đồng nhất của carbide:
ESR cải thiện đáng kể tính không đồng nhất của carbide và cấu trúc tinh thể của thỏi thép, đặc biệt là đối với thép khuôn dập nguội có hàm lượng carbon cao, crom cao. Trong cùng một tỷ lệ rèn, nó cải thiện 0,5 cấp, đặc biệt là tăng cường cấu trúc trung tâm. Việc tinh chế carbide làm tăng hàm lượng hợp kim trong ma trận sau khi tôi, do đó tăng cường hiệu ứng làm cứng thứ cấp và khả năng chống ram. Ngoài ra, ESR cũng cải thiện khả năng gia công nóng và độ dẻo dai của thép.
4. Cải thiện tính chất cơ học:
ESR cải thiện sự phân tách và tạp chất trong thỏi thép, tạo ra cấu trúc thép đồng nhất và dày đặc. Điều này tăng cường các tính chất cơ học, đặc biệt là giảm sự khác biệt về hiệu suất giữa các vùng dọc, ngang, trung tâm và cạnh của thép. Ví dụ, sau khi xử lý ESR Thép dụng cụ H13, tỷ lệ giữa độ bền kéo dọc và ngang và độ dẻo vượt quá 0,90, trong khi tỷ lệ độ dai va đập vượt quá 0,78.