What is cold forging? Cold heading is a metalworking method used to make fasteners such as bolts and screws. Because the molds are subjected to a lot of pressure during the cold heading process, they are prone to problems such as giymek, adhesion, cracking, and even fatigue or the molds becoming misshapen.

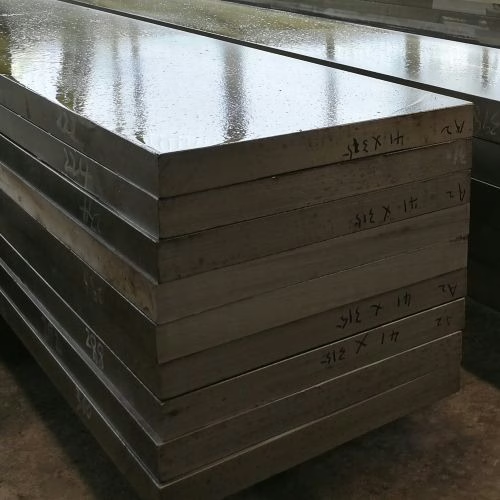
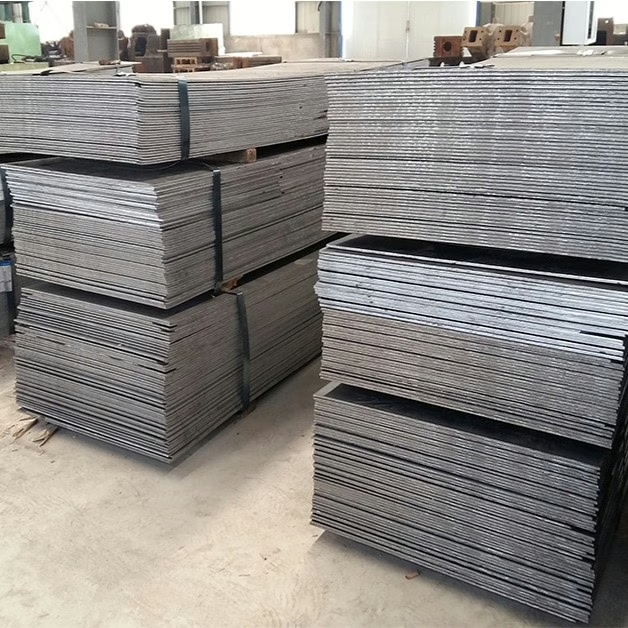
Soğuk başlık kalıpları neden arızalanır?
Soğuk başlık kalıpları çalışmalarında birkaç yaygın arızayla karşılaşırlar:
- Aşınma ve yıpranma: Kalıbın yüzeyi aşınır ve bu durum kullanım ömrünü etkiler.
- Adhesion: The metal material adheres to the mold, resulting in poor processing.
- Çatlama: Kalıp yüksek basınca dayanamadığı için çatlar.
- Yorgunluk: Uzun süreli kullanım sonucu kalıp içerisinde veya çalışma yüzeyinde yorgunluk hasarı meydana gelir.
- Shape Enlargement: The shape of the mold is propped up, which compromises precision.
Because of the high pressure in the cold heading process, the mold’s working surface needs to be very hard, usually with a hardness of 62 HRC (a hardness unit). Therefore, it is very important to choose the right steel.
Yaygın olarak kullanılan çelikler: W1 ve W2 su sertleştirilmiş çelikler
As mentioned in the article, the most common materials used for cold heading dies and punches (punches are the tools used with the dies) are W1 and W2 water-hardened steels. These steels have the following characteristics:
- Sığ Sertleştirme: Bu çelikler, su verildiğinde (çeliği sertleştiren bir ısıl işlem yöntemi) sadece yüzeyde sertleşir, iç kısım hala nispeten yumuşaktır.
- Sertleşebilirlik kontrolü önemlidir: Sertleşebilirlik, bir çeliğin söndürüldüğünde sertleşebileceği derinliktir. Sertleşebilirlik, kalıbın boyutuna göre ayarlanmalıdır.
Ancak W1 ve W2 çeliklerinin dezavantajları da vardır:
- Sınırlı aşınma direnci: 62-64 HRC sertlikte bile yeterince iyi değillerdir. Kalıp uzun süre kullanılacaksa, bu çelik yeterince dayanıklı olmayabilir.
Vanadyumun etkisi: Bazen çeliğe vanadyum (metalik bir element) eklenir, ancak vanadyum sertleşebilirliği azaltabilir. Bu sorunu çözmek için, çelikteki diğer elementler sertleşebilirliği garantilemek, çelik taneciklerini daha ince yapmak ve tokluğu artırmak için ayarlanabilir (tokluk, bir malzemenin kolayca kırılmama yeteneğidir).
Daha dayanıklı seçenek: yüksek alaşımlı çelikler (D2, M2, A2)
When it is necessary for a mold to last longer, choose a high-alloy steel such as D2, M2, or A2. The advantages and disadvantages of these steels are listed below:
- Avantajları: W1 ve W2'ye göre aşınma dayanımı çok daha yüksektir, seri üretime uygundur.
- Dezavantajları: Düşük tokluğa sahiptir (kolayca kırılır), doğrudan bütün kalıplara dökülemez.
Çözüm:
- Bu yüksek alaşımlı çelikleri insertlere (küçük kalıp parçaları) dönüştürün ve daha sonra bunları H11 çelikten yapılmış bir gövdeye monte edin.
- H11 çeliği, 48-50 HRC sertliğe sahip olup, ek parçaları koruyan ve tüm kalıbı hem aşınmaya dayanıklı hem de kırılmaya karşı daha az eğilimli hale getiren sağlam bir çeliktir.
Soğuk başlık kalıpları için çelik seçimi
Punch, soğuk şekillendirme işleminde kalıpla birlikte çalışan bir araçtır ve çelik seçimi de oldukça önemlidir:
- Kalıplar ve zımbalar gibi yaygın olarak kullanılan malzemeler de genellikle W1 veya W2 çelikten yapılır.
- Tokluk gerektiğinde, zımba kolayca kırılıyorsa veya aşınma direnci çok önemli değilse, S1 darbeye dayanıklı çelik kullanılabilir. Bu çelik toktur ve darbelere dayanabilir.
- Aşınma direncine ihtiyaç duyulduğunda: Zımbanın daha fazla aşınma direncine ihtiyacı varsa, D2 veya M2 çeliği kullanın.
In summary, the key to choosing steel
This article’s core idea is that different steels are suitable for different situations. The choice of steel is based on specific needs:
- If the mold or punch requires a hard, low-cost material, consider W1 or W2.
- If it needs to be used for a long time and has high wear resistance, choose D2, M2, or A2, but with a tough housing.
- Eğer delgeç kırılmaya müsaitse S1'i seçin.