The “QT” in 42CrMo4 QT stands for quenching and tempering. 42CrMo4 çeliği UNS sisteminde 1.7225 olarak adlandırılan, yaygın olarak kullanılan yüksek mukavemetli alaşımlı bir çeliktir.
42CrMo4'ün eşdeğer sınıfları şunlardır:
- ABD (ASTM/AISI): AISI 4140, SAE 4140H, ASTM A193 B7.
- Japonya (JIS): SCM440, SCM440H
- Çin (GB): 42CrMo
- İngiltere (BS): 708M40, EN19A
- Fransa (AFNOR): 42CD4
42CrMo4 steel exhibits deep hardenability, excellent comprehensive mechanical properties, and a low level of significant temper kırılganlıkMakine parçaları, bağlantı elemanları, krank milleri, dişliler ve kalıplarda yaygın olarak kullanılır.
42CrMo4 için standart ısıl işlem genellikle çeliğin ostenit oluşturmak üzere ısıtılmasını, ardından hızla soğutulmasını ve daha sonra daha düşük bir sıcaklığa tekrar ısıtılmasını içeren söndürme ve temperlemeden (Q&T) oluşur.
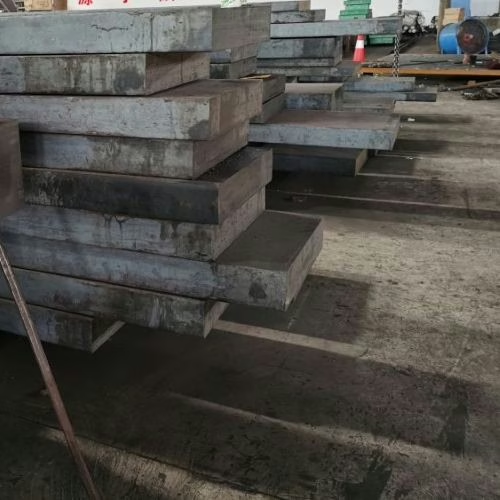
Lütfen aşağıdaki iletişim formunu doldurarak bizimle iletişime geçmekten çekinmeyin.
42CrMo4 Çelik Söndürme İşlemi
Söndürme, bir çelik nesneyi ostenitleme sıcaklığından hızla soğutarak ostenitin bir kısmını veya tamamını martensite dönüştürme işlemidir. Bu, çok sert ve güçlü, ancak kırılgan bir mikro yapıdır. Aynı zamanda, malzemenin kalıntı gerilimini ve deformasyonunu azaltabilir.
42CrMo4 çeliğinin ostenitleme sıcaklığı 800 ila 880°C (1475 ila 1650°F) arasındadır. Islatma süresi genellikle malzemenin kesit kalınlığına bağlı olup, her 25 mm (1 inç) maksimum kesit kalınlığı için minimum 1 saat veya 15 ila 20 dakikadır.
- Yağ Söndürme. 42CrMo4 çeliği genellikle yağda söndürülür. Yağda söndürücüler, soğutma hızlarına ve katkı maddelerine bağlı olarak hızlı, orta veya yavaş olarak sınıflandırılabilir. Yağda söndürücülerin normal çalışma sıcaklıkları 25 ila 70 °C (80 ila 160 °F) arasındadır. Bozulmayı en aza indirmek için 175 °C (350 °F) kadar yüksek sıcaklıklarda sıcak yağ kullanılabilir.
- Su Söndürme. 42CrMo4 genellikle yağda söndürülürken, daha büyük kesitlerde (örneğin çapı 75 mm veya 3 inçten büyük yuvarlak kesitler) tam sertleştirme elde etmek için suda söndürme kullanılabilir. Suyla söndürme banyoları genellikle 20 ila 40 °C (68 ila 104 °F) arasında tutulur ve soğutma homojenliğini artırmak için çalkalanır. Ancak suda söndürme, özellikle bu karbon seviyesinde çatlama ve bozulma olasılığını önemli ölçüde artırır.
42CrMo4 Çelik Tavlama İşlemi
As-quenched martensite in steel is very hard but also very brittle and contains high residual stresses. The purpose of tempering is to reheat quenched steel to below its lower critical temperature (Ac1) to increase its toughness and ductility, reduce hardness, and relieve internal stress.
The tempering temperature for 42CrMo4 steel is 175 to 705°C (350 to 1300°F), with a holding time of at least 1.5 to 2 hours. Different tempering temperatures determine the final hardness and strength of the material so that we can decide on the tempering temperature based on the hardness and strength required for the material. For “ultra-high” strength, tempering between 175 °C and 230°C (350°F and 450°F) is used, while for lower yield strengths (below 1380 MPa or 200 ksi), temperatures between 385 °C and 705°C (725°F and 1300°F) are applied.1 Tavlama sonrası soğutma hava veya su ile söndürme yoluyla yapılabilir.
42CrMo4 malzemesinin 250 ila 300°C (480 ila 570°F) arasındaki sıcaklıklarda temperlenmesinden kaçınılmalıdır. Bu sıcaklıklarda temperleme, 42CrMo4'ün darbe tokluğunun azalmasına neden olur; bu olguya Temperlenmiş Martensit Kırılganlığı (TME) denir.
Özet
The mechanical properties of 42CrMo4 steel are highly dependent on the oil quenching and tempering at various temperatures, generally, as the tempering temperature increases, hardness, tensile strength, and yield strength decrease, while ductility, toughness, and impact energy increase.
- ASM Uluslararası. (1991). ASM El Kitabı, Cilt 4: Isıl İşlem (s. 500-501). ASM International. ↩︎