4130 ve 4140 çelik: karşılaştıralım 4130 çelik ve AISI 4140 çelik, doğrudan çizim. Her ikisi de orta karbonlu, düşük alaşımlı çelikler olarak sınıflandırılır ve krom-molibden alaşımlı çelik ailesine aittir.
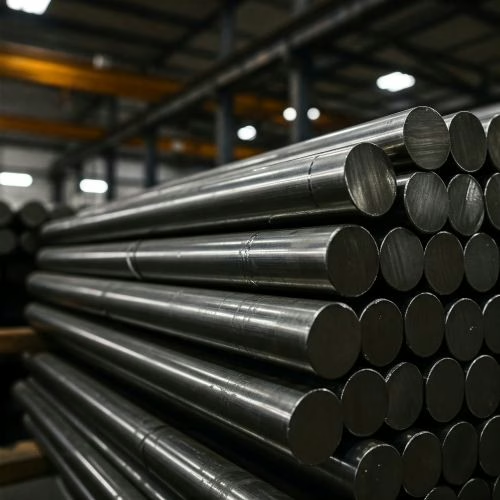
Kimyasal Bileşim
4130 ve 4140 çelik: bileşim karşılaştırması
Element | AISI 4130 (ağırlık%) | AISI 4140 (ağırlık%) | Notlar |
Karbon | 0.28-0.33 | 0.38-0.43 | 4140'ta daha yüksek karbon içeriği |
Manganez | 0.40-0.60 | 0.75-1.00 | 4140'ta daha yüksek manganez içeriği |
Silikon | 0.20-0.35 | 0.20-0.35 | |
Krom | 0.80-1.10 | 0.80-1.10 | |
Molibden | 0.15-0.25 | 0.15-0.25 |
Mekanik Özellikler
4130 ve 4140 çelik: özellik karşılaştırması. Mekanik özellikler, uygulanan ısıl işleme ve malzemenin kesit boyutuna büyük ölçüde bağlıdır. Bu bölümdeki veriler doğrudan ASM International (1991)'den alıntıdır. ASM El Kitabı, Cilt 4: Isıl İşlem (s. 500-503). ASM International.
Isıl işlem görmüş 4130 çeliğinin tipik mekanik özellikleri.
Tavlama sıcaklığı | Çekme dayanımı | Verim gücü | 50 mm (2 inç) cinsinden uzama, % | Alanda azalma, % | Sertlik, HB | Izod etki enerjisi | ||||
°C | °F | MPa | ksı | MPa | ksı | |||||
Suda söndürülmüş ve temperlenmiş. 25 mm (1 inç) çapındaki yuvarlak çubuklar 845 ila 870 °C (1550 ila 1600 °F) arasında söndürülmüştür. | ||||||||||
205 | 400 | 1765 | 256 | 1765 | 1520 | 10 | 33 | 475 | 18 | 13 |
260 | 500 | 1670 | 242 | 1670 | 1430 | 11.5 | 37 | 455 | 14 | 10 |
315 | 600 | 1570 | 228 | 1570 | 1340 | 13 | 41 | 425 | 14 | 10 |
370 | 700 | 1475 | 214 | 1475 | 1250 | 15 | 45 | 400 | 20 | 15 |
425 | 800 | 1380 | 200 | 1380 | 1170 | 16.5 | 49 | 375 | 34 | 25 |
540 | 1000 | 1170 | 170 | 1170 | 1000 | 20 | 56 | 325 | 81 | 60 |
650 | 1200 | 965 | 140 | 965 | 830 | 22 | 63 | 270 | 135 | 100 |
Yağda söndürülmüş ve temperlenmiş. 25 mm (1 inç) çapında yuvarlak çubuklar 860 °C'de (1575 °F) söndürülmüş. | ||||||||||
205 | 400 | 1550 | 225 | 1340 | 195 | 11 | 38 | 450 | / | / |
260 | 500 | 1500 | 218 | 1275 | 185 | 11.5 | 40 | 440 | / | / |
315 | 600 | 1420 | 206 | 1210 | 175 | 12.5 | 43 | 418 | / | / |
370 | 700 | 1320 | 192 | 1120 | 162 | 14.5 | 48 | 385 | / | / |
425 | 800 | 1230 | 178 | 1030 | 150 | 16.5 | 54 | 360 | / | / |
540 | 1000 | 1030 | 150 | 840 | 122 | 20 | 60 | 305 | / | / |
650 | 1200 | 830 | 120 | 670 | 97 | 24 | 67 | 250 | / | / |
Kütlenin ısıl işlem görmüş 4130 çeliğinin tipik özellikleri üzerindeki etkileri
Çubuk boyutu (mm) | Çubuk boyutu (inç) | Çekme dayanımı (MPa) | Çekme dayanımı (ksi) | Akma dayanımı (MPa) | Akma dayanımı (ksi) | 50 mm (2 inç) cinsinden uzama, % | Alanda azalma, % | Yüzey sertliği, HB |
25 | 1 | 1040 | 151 | 880 | 128 | 18 | 55 | 307 |
50 | 2 | 740 | 107 | 570 | 83 | 20 | 58 | 223 |
75 | 3 | 710 | 103 | 540 | 78 | 22 | 60 | 217 |
Not: 845 °C'de (1550 °F) yağda söndürülmüş ve 540 °C'de (1000 °F) temperlenmiş yuvarlak çubuklar; 12,83 mm (0,505 inç) çapında çekme dayanımı
Isıl işlem görmüş 4140 çeliğinin tipik mekanik özellikleri
Tavlama sıcaklığı (°C) | Tavlama sıcaklığı (°F) | Çekme dayanımı (MPa) | Çekme dayanımı (ksi) | Akma dayanımı (MPa) | Akma dayanımı (ksi) | 50 mm (2 inç) cinsinden uzama, % | Alanda azalma, % | Sertlik, HB | İzod darbe enerjisi (J) | İzod darbe enerjisi (ft·lb) |
205 | 400 | 1965 | 285 | 1740 | 252 | 11 | 42 | 578 | 15 | 11 |
260 | 500 | 1860 | 270 | 1650 | 240 | 11 | 44 | 534 | 11 | 8 |
315 | 600 | 1720 | 250 | 1570 | 228 | 11.5 | 46 | 495 | 9 | 7 |
370 | 700 | 1590 | 231 | 1460 | 212 | 12.5 | 48 | 461 | 15 | 11 |
425 | 800 | 1450 | 210 | 1340 | 195 | 15 | 50 | 429 | 28 | 21 |
480 | 900 | 1300 | 188 | 1210 | 175 | 16 | 52 | 388 | 46 | 34 |
540 | 1000 | 1150 | 167 | 1050 | 152 | 17.5 | 55 | 341 | 65 | 48 |
595 | 1100 | 1020 | 148 | 910 | 132 | 19 | 58 | 311 | 93 | 69 |
650 | 1200 | 900 | 130 | 790 | 114 | 21 | 61 | 277 | 112 | 83 |
705 | 1300 | 810 | 117 | 690 | 100 | 23 | 65 | 235 | 136 | 100 |
Kütlenin ısıl işlem görmüş 4140 çeliğinin tipik özellikleri üzerindeki etkileri
Çubuk çapı (mm) | Çubuğun çapı (inç) | Çekme dayanımı (MPa) | Çekme dayanımı (ksi) | Akma dayanımı (MPa) | Akma dayanımı (ksi) | 50 mm (2 inç) cinsinden uzama, % | Alanda azalma, % | Yüzey sertliği, HB |
25 | 1 | 1140 | 165 | 985 | 143 | 15 | 50 | 335 |
50 | 2 | 920 | 133 | 750 | 109 | 18 | 55 | 202 |
75 | 3 | 860 | 125 | 655 | 95 | 19 | 55 | 293 |
Not: 845 °C'de (1550 °F) yağda söndürülmüş ve 540 °C'de (1000 °F) temperlenmiş yuvarlak çubuklar; 25 mm çaplı çubukların merkezinden ve 50 ve 75 mm çaplı çubukların orta yarıçapından kesilmiş 12,83 mm (0,505 inç) çaplı çekme numuneleri

Isıl İşlem Prosedürleri
4140 Isıl İşlem
- Normalleştirme: 870 ila 925 °C'ye (1600 ila 1700 °F) ısıtın ve maksimum kesit kalınlığının her 25 mm'si (1 inç) için en az 1 saat veya 15 ila 20 dakika tutun; hava ile soğutun. Normalleştirmeden sonra, akma dayanımını azaltmak için genellikle 480 °C'de (900 °F) veya daha yüksek bir sıcaklıkta tavlama yapılır.
- Tavlama: 830 ila 870 °C'ye (1525 ila 1600 °F) ısıtın ve kesit kalınlığına veya fırın yüküne bağlı olarak bir süre tutun; fırında yaklaşık 15 °C/saat (30 °F/saat) hızla 480 °C'ye (900 °F) soğutun ve ardından havada soğutun.
- Söndürme: Suya dayanıklı alaşımlı bir çeliktir.
4130 ısıl işlem
- Normalleştirme: 845 ila 925 °C'ye (1550 ila 1700 °F) ısıtın ve en az 1 saat veya maksimum kesit kalınlığının her 25 mm'si (1 inç) için 15 ila 20 dakika tutun; havada soğutun.
- Tavlama: 830 ila 870 °C'ye (1525 ila 1600 °F) ısıtın ve kesit kalınlığına veya fırın yüküne bağlı olarak bir süre tutun; fırında yaklaşık 15 °C/saat (30 °F/saat) hızla 480 °C'ye (900 °F) kadar soğutun ve ardından havada soğutun.
- Söndürme: 855 °C (1575 °F) veya 845 °C (1550 °F) sıcaklıkta yağda söndürülür.
- Temperleme: Basit bir temperleme döngüsüne sahiptir ve genellikle 175 °C (350°F) kullanılır. Mavi kırılganlığı önlemek için, 4140 genellikle 230 ila 370 °C (450 ila 700 °F) arasında temperlenmez. Temperleme sıcaklığı ve süresi, istenen sertliğe bağlıdır.
Özet
4140 ve 4340 çelik arasındaki farklar, özelliklerine ve kullanım deneyimlerine göre özetlenmiştir.
Daha yüksek karbon ve manganez içeriğine sahip 4140, genellikle 4130'a kıyasla daha yüksek sertleştirilebilirlik ve daha yüksek mukavemet sunar. Bu, uygun ısıl işlem uygulandığı takdirde, 4140'ı daha ağır kesitlerde daha yüksek mukavemet gerektiren uygulamalar için uygun hale getirir. 4140 daha iyi sertleştirilebilirliğe sahiptir, ancak aynı geometriye sahip parçalarda aynı söndürme etkisini elde etmek için 4130'a göre daha yumuşak bir söndürme işlemi gerektirir. 4140, söndürme işlemi sırasında aşırı soğutma hızı nedeniyle belirli bir çatlama ve deformasyon olasılığına sahiptir. 4140'a söndürme uygulanırken, söndürme parametrelerinin sıkı bir şekilde kontrol edilmesi önemlidir.
İnce kesitler için sade karbon çeliği yeterli olabilirken, sertleştirme gerektiren daha ağır kesitler için 4140 gerekecektir. Ancak, 4140 yeterliyse, 4340 gibi daha pahalı bir alaşım seçmek (Nikel-Krom-Molibden içeriği sayesinde daha da yüksek sertleştirilebilirliğe sahip) gereksiz olabilir. Genellikle Cr-Ni-Mo içeren çelikler en pahalı olanlardır, ardından Cr-Mo ve ardından Cr-V gelir.
4140 ve 4130 Çelik için Rekabetçi Bir Teklif Alın
20 yılı aşkın dövme uzmanlığıyla Aobo Steel, yüksek performanslı 4140 ve 4130 alaşımlı çelik konusunda güvenilir ortağınızdır. Sadece malzeme değil, çözüm de sunuyoruz. Projenizin başarısı için derin sektör bilgimizden ve güvenilir tedarik zincirimizden yararlanın.
✉ Aşağıdaki formu doldurarak bizimle iletişime geçin.