A2 tool steel offers good to excellent wear resistance and abrasion resistance, making it a versatile choice for many cold-work applications. While superior to lower alloy steels, it doesn’t match the extreme wear resistance of high-carbon, high-chromium grades, such as the D-series, which represents a balance between wear resistance, toughness, and ease of heat treatment.
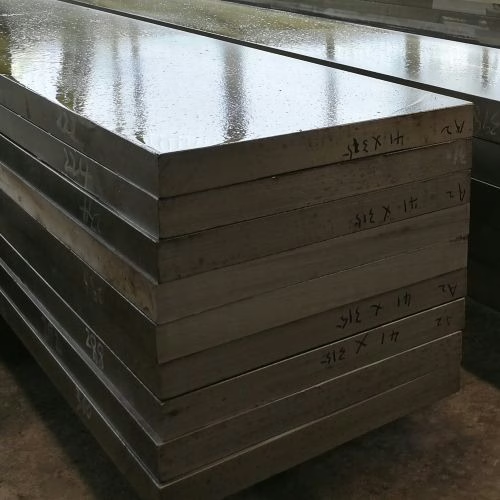
What Gives A2 Tool Steel Its Wear Resistance?
A2 tool steel’s reputation for reliable wear resistance isn’t accidental; it’s engineered into its very structure. As an air-hardening, cold-work tool steel, its performance characteristics stem directly from its chemical composition and the microstructure developed during heat treatment.
Key factors contributing to A2’s wear resistance include:
- Carbon Content: A higher carbon content is fundamental for hardness.
- Chromium Content: Approximately 5% chromium is added. This, along with the carbon, promotes the formation of hard alloy carbide particles within the steel matrix after heat treatment.
- Hard Martensitic Matrix: Proper heat treatment develops a complex martensitic matrix. This matrix is crucial not only for overall hardness but also for securely holding the hard carbide particles.
- Alloy Carbides: These microscopic, hard particles are distributed throughout the matrix. They are significantly more complex than the surrounding matrix and play a direct role in resisting abrasive wear by preventing material removal.
This combination allows A2 to achieve a desirable balance of properties suitable for demanding tooling tasks.
How Does A2 Tool Steel Compare to Other Tool Steels?
Understanding where A2 sits in the spectrum of tool steel options helps in selecting the right material for a specific job.
- vs. S-Series (Shock-Resistant): A2 generally exhibits higher abrasion resistance than typical S-series tool steels.
- vs. O-Series (Oil-Hardening): A2 offers wear resistance that is equal to or often exceeds that of common oil-hardening grades, such as O1 tool steel. For instance, A2 provides roughly 20-25% more wear resistance than A6, another air-hardening steel, which itself is about 15% better than O1.
- vs. D-Series (High-Carbon, High-Chromium): This is where the distinction becomes important. D-series steels, such as D2, are specifically formulated for maximum abrasion resistance, containing a higher volume of hard alloy carbides. D2, often a benchmark, offers 30-40% more wear resistance than A2. If extreme abrasion is the primary challenge, the D-series might be preferred, although this typically comes at the cost of some toughness. Read more about the compression of D2 and A2 tool steel by clicking D2 vs. A2 tool steel.
- vs. High-Speed Steels (e.g., M2, M4): Many high-speed steels also surpass A2 in wear resistance.
On a relative scale, if A2 is rated a 6 for wear resistance, D2 would be an 8, and a high-wear grade like M4 could be a 9.
Typical Applications and Hardness
A2’s blend of good wear resistance and reasonable toughness makes it a workhorse for various applications:
- Forming Dies
- Blanking Dies (especially for sizable lots, even on abrasive materials like unpickled hot-rolled steel)
- Drawing Dies
- Trimming Dies
- Thread-Rolling Dies (though D2 or M2 might offer longer life here)
The typical working hardness for A2 is often in the 56-64 HRC range, depending on the specific application and the balance desired between wear resistance and toughness. A hardness level of approximately 64 HRC is generally targeted when dealing with highly abrasive conditions.
Enhancing A2 Steel’s Wear Resistance
For applications demanding even better performance, A2’s wear resistance can be further improved through surface treatments:
- Boriding: This process can more than double the metal-to-metal wear resistance of A2.
- Titanium Nitride (TiN) Coating: Often applied via Physical Vapor Deposition (PVD) to minimize heat impact on the base steel, TiN coatings are a common way to significantly boost the surface hardness and wear resistance of A2 tooling.
A Note on Toughness
It’s crucial to remember the interplay between wear resistance and toughness. While A2 offers good wear resistance, its toughness is generally considered superior to the D-series steels. The choice between A2 and a higher-wear-resistance steel, such as D2 tool steel, often comes down to balancing the need for abrasion resistance against the need for toughness to prevent chipping or cracking in the application.
In summary, A2 tool steel offers a robust, reliable level of wear resistance suitable for a wide range of cold-work tooling, striking an effective balance between performance, toughness, and heat treatment characteristics.
Need Reliable A2 Tool Steel? Request a Quote & Benefit from Our Stable Supply Chain.
Aobo Steel has over 40 stable suppliers, ensuring a consistent and reliable source of high-quality A2 tool steel. Get a quick quote today and experience the confidence of working with an experienced partner.👇👇👇